First developed at the turn of the century, advanced high-strength steel (AHSS) could be called a subtle disruptor. Designed to behave and be used in the same fashion as traditional steels, its use in vehicle manufacturing requires nowhere near the level of investment required by alternatives such as aluminium. OEMs looking to take advantage of AHSS need not necessarily pour capital expenditure into retooling stamping shops that already work with mild steel.
Yet its advanced strength and ductility have made it indispensable to OEMs looking to realise major efficiency gains – and that’s just about every vehicle manufacturer in the world. Along with CAFE and European emissions regulations, consumers themselves are increasingly basing their vehicle purchasing decisions on environmental factors.
According to the Office of Energy Efficiency & Renewable Energy in the US, use of AHSS can result in components that are 25% lighter than their mild steel equivalents. As Rajeev Singh, Partner at KPMG India, Automotive, wrote in the Q4 2015 edition of Automotive Megatrends magazine, OEMs like BMW have discovered that CO2 reduction of 10-15g/km can be achieved for each 100kg (220lbs) of weight reduced, and use of AHSS can help to achieve overall weight savings of 20%.
The geometry of an individual part is one of the most influential factors when designing for mass-optimisation
As a result, AHSS has been adopted across multiple segments. A mass market offering such as the Opel Astra uses AHSS to stiffen its passenger cell, as well as hold up its seat frames, which are 10kg (22lbs) lighter than the previous generation model. Meanwhile, upmarket models make extensive use of hot-formed AHSS; for example, the Volvo XC90’s overall composition is 40% hot-formed boron steel, helping it achieve a 122kg weight saving compared with its predecessor.
But there are limits to what can be achieved – traditionally, higher strengths come at the expense of ductility. There are ways around this – hot stamping, or additional heat treatment cycles – but the technology required can have significant effects on both cost and production cycle time.
One company which thinks it may have a solution is NanoSteel. Originally a spinoff of the US Department of Energy’s Idaho National Laboratory, NanoSteel is an advanced materials company specialising in the design of steels built of microstructures that form on the scale of nanometres – smaller than those found in traditional steels. Unlike traditional steel giants, the company doesn’t handle production itself, allowing it to focus on design, and operate on the cutting edge of steel technology.
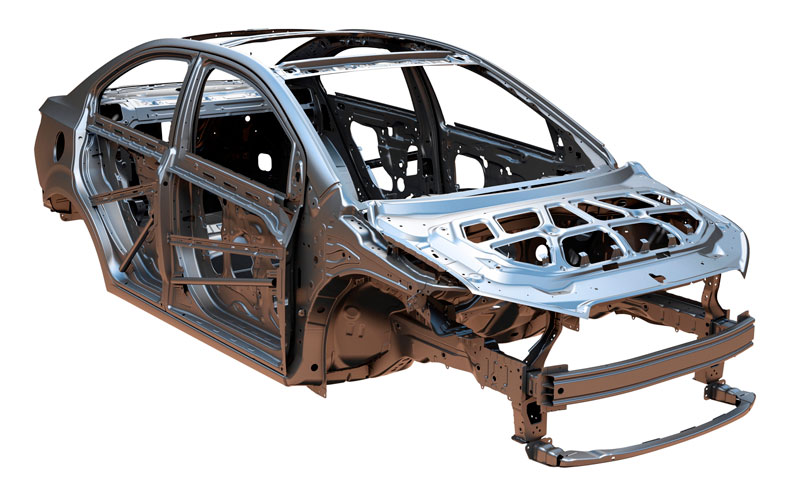
The company services numerous industries, including the 3D printing sector, for which it develops metal powders. However, it’s the automotive industry where the company sees the biggest potential, and for which it has developed what it calls a ‘third-generation AHSS’.
“Even the newest grades of steel have to make large sacrifices in formability in order to deliver strength for automotive part design,” explains Tad Machrowicz, Vice President, Automotive Engineering at NanoSteel. “Strengths available to customers have gradually increased over the last 25 years, resulting in materials with strengths in excess of 1000 MPa, but the trade-off with formability has been consistent.” So what makes ductility so important?
Strength and ductility – achieving geometric freedom with AHSS
NanoSteel’s AHSS, says Machrowicz, provides the high strength required by automotive engineers in combination with significant ductility – “the strongest available steels with the formability of mild steel,” as he puts it. This can provide what NanoSteel has identified as something every single OEM is looking for – geometric freedom, or the ability to create ultra complex shapes from sheet AHSS. A material from which complex shapes cannot easily be made, such as body parts, is limited in its application.
“The geometry of an individual part is one of the most influential factors when designing for mass-optimisation,” says Machrowicz. “The majority of parts in a vehicle structure must be stiff in multiple directions to function well and provide the smooth, confident and quiet ride that consumers expect.”
A material’s stiffness is a function of its geometry and modulus – a value used to measure its resistance to non-permanent, ‘elastic’ deformation. The higher the modulus, the stiffer the material. This, says Machrowicz, lends steel possibilities for optimisation that aluminium does not posses.
“Aluminium feels light because its density is a third that of steel,” he explains. “However, its modulus is also a third of that of steel. In reality, if you were to make two parts with equal geometries, an aluminium part would require three times as much material as the steel part to be equally stiff, thereby cancelling the density and subsequent weight advantage.”
In short, the higher a material’s formability, the more an OEM can optimise a part’s geometry, and thus the thinner the sheet needed. An AHSS that doesn’t sacrifice on strength but provides high ductility would give manufacturers the chance to reduce weight, whilst maintaining stiffness.
Buckling under pressure
NanoSteel has developed its product to contend with the problem of load-limit. Once a part is formed, it has to be able to handle the loads placed on it without suffering permanent deformation. A strong stiffness can help, but stresses can then build in the material that breach its limit, and cause failure. Traditionally, says Machrowicz, there are three ways to solve a load-carrying shortfall.
In reality, if you were to make two parts with equal geometries, an aluminium part would require three times as much material as the steel part to be equally stiff, thereby cancelling the density and subsequent weight advantage
The first is simply to use a thicker grade of the material that can share the stress load more evenly. This is unacceptable for vehicle designers, given the increased cost and mass involved, and thus defeating the purpose. The second option is use of a stronger material, “the ideal scenario,” says Machrowicz, “but not at the expense of geometric freedom.” The third option for engineers, says Machrowicz, is to pay closer attention to the geometries, and optimise them in ways that distribute stress-loads more evenly. “By doing this,” he explains, “peak load or so-called hot spots are minimised. When the hot spots are removed, and stresses are more evenly distributed through intricate geometries, engineers can use the thinnest material possible and thus optimise mass for a given functional load carrying requirement.” NanoSteel’s AHSS allows them to do this without reverting back to an easily formable, low-strength steel.
Here to stay
The global steel industry may have experienced turbulence in 2015, but analysts agree that there will be little if any effect on the automotive steel sector. ArcelorMittal has predicted that cost savings on offer will see OEMs currently exploring alternative materials such as aluminium eventually return to steel as the lightweighting material of choice.
The steel supplier argues that whilst aluminium has clear benefits, being up to 66% lighter than steel, it is ultimately an expensive, last-minute fix that can cost an OEM anywhere between €3 and €15 (US$3.29 and US$16.44) per kilo of weight saved. If steel suppliers are involved early in the vehicle design process, it says, they can achieve in steel everything that they are developing in aluminium – but at a far lower cost.
NanoSteel goes further, arguing that at some point in time, aluminium will not create cost effective weight savings for a number of automotive applications, even as a last-minute fix. “We believe that once a material like NanoSteel is available, aluminium will not create weight savings at any stage in the design for most non-exterior structural parts, given the need to increase the part gauge to deliver required stiffness,” says Machrowicz; confidence abounds in a manufacturing landscape that grows more complex by the day.
This article is part of an exclusive Automotive World report on lightweighting. Follow this link to download a copy of ‘Special report: Vehicle lightweighting‘