There are still improvements to be made in the design and development of passenger vehicles, not just during powertrain construction, but also throughout the entire vehicle formation process.
Tradition
There has been a 40% increase of models offered by OEMs across the globe in the last 15 years, explains Kevin Golsch, Technical Director, North America Ground Transportation, Exa Corporation. Speaking at Automotive Megatrends USA, Golsch examined the downfalls of design and development processes. He believes that it has changed dramatically over the past decade, but there are still significant improvements to be made.
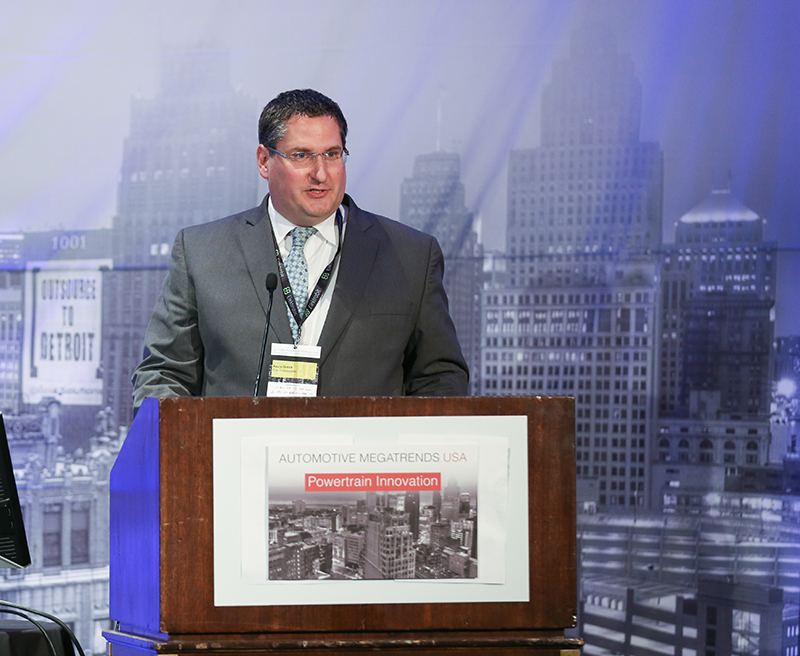
“The timing of model design to production has been reduced. There is conflict between the number of models being introduced and the time to develop these models, causing OEMs to have problems in the later stages of design. And model proliferation is ever increasing, and shows no signs of slowing,” he says.
Furthermore, there is greater consideration of the vehicle as a whole, rather than a focus on individual parts. Nowadays OEMs take into account other parts of the vehicle whilst designing and developing powertrains in order to optimise performance. Rightly so, suggests Golsch: “Traditionally, there was a contest between chassis and powertrain engineering. But if you look at them both as a system, that is when you can make some synergies.”
Imperfect test process
These potential synergies between the powertrain and other areas of the vehicle are all too often lost, says Golsch. This is primarily due to changes that are made late in the design stage of vehicles, which could be avoided if the process itself was altered.
“The process, in my opinion, is to blame for a lot of these late failures. Traditional test and measurement methods are inaccurate and unreliable, and simulations are often not representative of the road,” observes Golsch.
Criticising drive cycle tests, Golsch suggests that conditions within laboratories do not accurately represent real world environments. Consequently, components are not designed to perform well on public roads and under real conditions, but are instead optimised for laboratory conditions. “As long as you are in the laboratory, performance figures are pretty good in most cases. But when you get outside of your sandbox, you are going to start having problems which will have a big impact later on in the programme,” he warns.

To combat this, Golsch believes that two main areas must be addressed. To start with, thermal wind tunnels in laboratories do not accurately replicate real world conditions. He also suggests that test-track conditions are “hard to precisely control,” and even if OEMs maintain they have carried out on-road tests, these roads may not be representative of public roads.
Cutting out late stage changes
When manufacturers make late-stage design changes, “there is generally almost no time left before production begins to optimise the vehicle and its components,” explains Golsch. “Usually, at the end of the programme, the available solutions add a lot of weight and cost to the car.”
To reduce costs, weight and time,, Golsch is “proposing a new robust design process that will allow manufacturers to meet fuel economy and emissions targets.” He says that designs must be finalised early whilst there is still time to change subsystems and critical components. What is more, it is crucial for vehicles to be tested under the “full array of operating conditions” so that components can be optimised to perform best when in the real world, as opposed to during drive cycles.
He also sees computers playing an increasingly strong role in the design and development of vehicles, as OEMs look to expand their model portfolios and incorporate new powertrain architectures. “As human beings, we try one thing, make a change and evaluate the system before repeating the process. With computer systems, we can test systems and subsystems effectively, reduce the time of development and prevent late-stage design changes,” states Golsch.
Michael Nash