Autonomous technologies and advanced driver assistance systems (ADAS) require a number of cameras and sensors to operate. Whether they are substitute cameras for rear visibility, or sensors for autonomous emergency braking and lane keeping, the key to their unhindered operation is cleanliness.
Cameras and sensors are the eyes and ears of modern vehicles, and without them autonomous driving would be impossible. Their operation is based on being able to detect the world around them, but the world in which they operate is not a simple one. A vehicle’s surroundings consist of other vehicles, pedestrians, road signs, lane lines, animals and far more besides. Due to the complex environment facing an autonomous vehicle, even in ideal weather conditions, multiple sensor types including cameras and infrared, ultrasonic, radar and LiDAR sensors are required to read the environment clearly.
The reason that so many different pieces of autonomous technology are necessary is because, individually, they have limitations. Cameras, for example, can struggle with glare and low light scenarios, hence the need to supplement them with sensors.
Keep it clean
Both cameras and LiDAR must be clean in order to operate correctly, but the environment in which they operate rarely offers this luxury. In normal driving, an autonomous vehicle will typically encounter any number of the following; dirt, salt, water, snow, tyre debris, guano and other contaminants. When these contaminants deposit on cameras or other sensors such as LiDAR, they can severely hinder their performance. In order to prevent this, the sensors must either be positioned in locations which are shielded from contamination, or include some form of self-cleaning system.
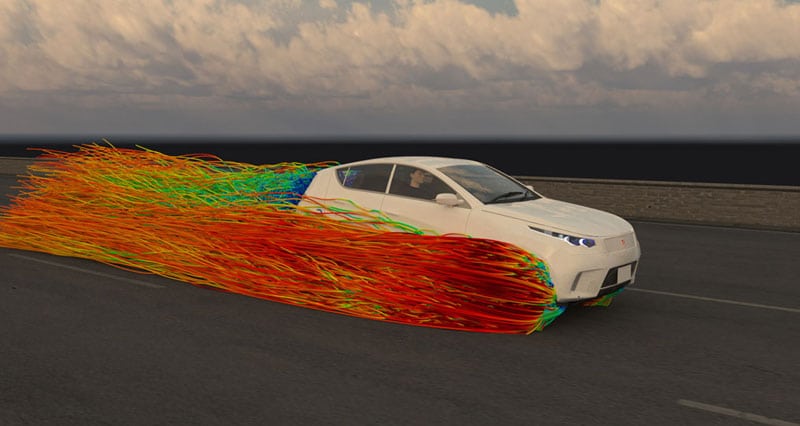
“Sensors get dirty and there are different sources of contamination, and we can help with that in three ways,” explains Jonathan Jilesen, Director of Soiling and Water Management at Exa Corporation, which in 2017 became a Dassault Systèmes company.
Exa’s PowerFLOW simulation software can be used by OEMs to predict surface contamination patterns in the real world environment in which autonomous vehicles exist, including rain, wheel spray and wind conditions. This information is vital to aid sensor positioning decisions, or to change the vehicle design to better protect the desired sensor location from contamination.
“The first way we can help is that we can predict where dirt, bugs or other matter are going to hit the vehicle,” explains Jilesen. “Then, we can help by advising how changes to the vehicle will affect issues such as how many drag counts that might cost.” The drag count can be used to assess whether a design change or the alteration of a camera position will impact fuel economy, or create a noise issue.
“The third way we can do it is with sprayers. We can predict how the sprayers are going to spray the surface and we can tell whether or not at different vehicle speeds or under different yaw conditions, the spray will hit the target, and with enough force to effectively clean anything.”
Cleanliness costs less
With the speed of change in sensor technology, it seems prudent to suggest that the need to keep sensors clean may simply be something of a sticking-plaster solution to the limitations of current technology. Could it be that in even just a few years’ time, technology will have advanced to a point where there may no longer be a need to keep sensors clean, as they work even when obstructed?
“We’ve researched into different coatings, for example, but such solutions all still come with associated costs,” says Jilesen. “There will always be a balance between investing in, for example, an expensive coating on a surface, and just moving a sensor by a couple of inches. We can still help.”
We’re also getting into electric vehicle cabin comfort. To cool or heat the cabin is a substantial power drain from the vehicle. And that includes how the vehicle heats up when it’s exposed to the sun, and keeping the cabin at a certain temperature
Exa’s simulation technology is not exclusive to light vehicle applications, however. “We developed this technology without really seeing how important it was going to be for autonomous vehicles,” said Jilesen. “When I started thinking about autonomous vehicles, I realised there’s a big marketing potential. But it’s also about trucks, buses, and off-road vehicles.”
Water ingestion can create particular problems for heavy trucks, he notes. “Big trucks can draw in water and that can cause issues if it gets into their filters. The brakes of a train can cause dust particles to get ingested into the motor that’s on the underbody. The same can happen with car brakes, because if you have brake dust from your car, certain rim designs will get more brake dust deposits on them than others. And if you get that brake dust depositing on the side body, it causes rust issues. We can help with that.”
When it comes to the location of sensors, Exa works not only with the sensor manufacturers and the sprayer manufacturers, but also directly with vehicle manufacturers. At the 2014 Paris Motor Show, Jaguar displayed the all-new XE, the first car to have moved into production without a prototype build for aerodynamic testing. The OEM used Exa’s digital simulation for all aerodynamic testing, as well as key thermal management applications such as heat exchanger performance, grille sizing (with active shutters), brake cooling and aeroacoustic wind noise design evaluation. More recently, Land Rover used Exa’s simulations to during the development of the 2017 Discovery to optimise water and soiling management, and BMW has used Exa’s PowerFLOW solution to understand windscreen sprayer location.
Dirty aero
From aerodynamics to soil and water management seems a strange leap, but where air goes, so goes whatever is being carried along by that air, including dirt and water.
There will always be a balance between investing in, for example, an expensive coating on a surface, and just moving a sensor by a couple of inches. We can still help
“The aerodynamic performance strongly impacts the soiling,” nods Jilesen. “We’re able to accurately predict the transient aerodynamics, which you need to do in order to correctly predict the soiling line. But at the same time, there are trade-offs, because if I make the vehicle more aerodynamic, it’s likely to get very dirty, especially for square-backed vehicles. But there are other situations where the side body soiling will get better because you’re going to manage your wheel weight better, for example.”
This raises an interesting question; in today’s automotive industry, is it the aerodynamic performance, or the sensor location which generates greater demand for a company such as Exa? “It depends how fast the vehicle is moving,” grins Jilesen. “In trucks, aerodynamics definitely is more important because fuel economy is king for trucks. But at the same time, you can’t have a failure issue due to water ingestion, so that’s a priority.”
Thermal and acoustic
Beyond aerodynamics and the path of water, Exa’s software can also be used for assessing thermal and acoustic performance. “And now we’re also getting into cabin comfort,” says Jilesen. This is an area that he expects to play a significant role in the development of electric vehicles. “To cool or heat the cabin is a substantial power drain from the vehicle. And that includes how the vehicle heats up when it’s exposed to the sun, and keeping the cabin at a certain temperature.”
Aerodynamic performance strongly impacts the soiling. We’re able to accurately predict the transient aerodynamics, which you need to do in order to correctly predict the soiling line. But at the same time, I make the vehicle more aerodynamic, it’s likely to get very dirty
In terms of acoustics, Exa uses the Lattice Boltzmann Method, the underlying digital physics methodology used for all Exa’s simulation, including acoustics. “We can get out the noise, and tones, and predict design performance, such as the acoustic implications of moving a mirror, and how it will sound in the ear of the driver. Or if you change the design of the windshield wipers, you may introduce an annoying tonal noise. We can predict that based on the airflow. Then, we use other software to extrapolate that inside the cabin and predict what the driver will hear.”
Location, location, location
The ultimate goal is to create vehicles where sensors are placed optimally for minimal dirt deposition. Sensors must not be placed where they are exposed to large droplets of water. PowerFLOW has the capability to simulate the lifecycle of raindrops as they approach the vehicle, splash on its surface, are entrained into the wake, and become deposited on the vehicle’s surfaces. This capability liberates vehicle manufacturers to position sensors early in the design process to avoid costly cleaning devices.
However, if such devices are needed, the software can also be used to correctly position sprayer cleaning systems, thereby accounting for the impact of local airflow at any given vehicle speed. This allows for the comprehensive assessment of sprayer properties, such as cone angle, spray velocity and droplet size, on the cleaning power of the sprayer once installed on the vehicle.
We can predict how the sprayers are going to spray the surface and we can tell whether or not at different vehicle speeds or under different yaw conditions, the spray will hit the target, and with enough force to effectively clean anything
Speak to any automotive supplier, and one of the main complaints they have regarding is that they are not included early enough in the OEM’s vehicle design process. When asked what advice he might have for the vehicle manufacturers as they develop future vehicles, Jilesen echoes this concern: “The advice that Exa is giving to the vehicle manufacturers and customers is that if you do the simulation early, you will find all those problems in simulation, and you could make considerable financial savings. You can eliminate a problem as opposed to fixing it later.”
By doing this work virtually, manufacturers can optimise designs in the development phase, saving hundreds of millions of dollars in expensive physical models, and identifying camera and sensor placement issues while they can still be fixed, relatively cheaply.
Previously, he notes, an OEM had to build a car to test its soiling and water management, with costs running into millions of dollars simply to change an A-pillar mould. “You don’t want to do that!” he says. “We can give you that feedback much earlier, before you’ve even built anything.”