Today’s automotive industry is awash with players who, ten years ago, had little to do with transportation, or didn’t even exist. The entry of tech giants, start-ups and service providers is testament to the profit potential of greater vehicle connectivity and autonomy, with Silicon Valley and its global equivalents all scrambling to carve out their own piece of the pie.
One consequence of this is greater demand for rapid prototyping (RP), as OEMs race to bring advanced features to the roads first. Demonstrator vehicles are a common feature of modern automotive shows, and for these purposes, traditional tooling isn’t necessarily practical. Instead, designers are turning to technologies such as additive manufacturing and computer numerical control (CNC) machining. Not only can they provide the required parts far quicker, with turnaround times of weeks as opposed to months, but the volumes they produce are far more suited for today’s purposes. As Daniel Konrad explains, “customers want to see results relatively quickly, and in most cases, they build only around five vehicles, as opposed to a more traditional number like 100, because the rest of what they’d like to achieve can be done in a simulated environment.”
Our ability to respond quickly to these changes keeps our customers happy. Sometimes, a part will go through multiple iterations in a week
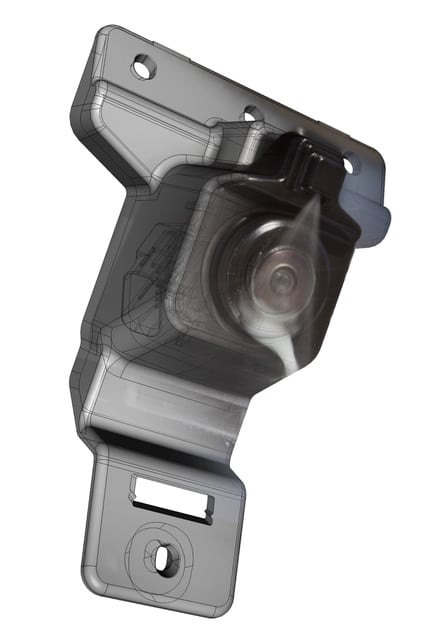
Konrad is Vice President, Engineering at dlhBOWLES, a leading supplier of fluid management assemblies to the automotive industry. Applications include sensor cleaners, headlight washers, and a number of body and chassis components. The company offers customers a full RP service, leveraging its unique position as one of the few suppliers of its kind in the industry. This is particularly the case with washers, says Konrad, with greater vehicle autonomy and ADAS requirements which demand robust cleaning for sensors. For example, it may mock up a subassembly where a camera sensor and wash nozzle have been integrated, requiring brackets and housing.
This RP service is available to everyone from The Big Three to start-ups with minimal staff. Alan Romack, Manager of Product Development and manager of the company’s 3D printing lab and machine shop, says that all players are now short-cutting their way through the traditional development processes, and that as a result, requirements are changing frequently. “Our ability to respond quickly to these changes keeps our customers happy,” he says. “Sometimes, a part will go through multiple iterations in a week.”
Manufacturers want to put the hardware out there for people and investors to see. They need to be able to do this quickly, and in a visually appealing way. Rather than mocking something up and using camouflage, companies are showing off ready-looking vehicles
The technical know-how
3D printing is hardly a new technology, but one of the key challenges hindering RP in previous years has been its finished quality. As Romack explains, companies will often send vehicles to be retrofitted with functional, mounted systems. These need to be attractive, as quite often, these demonstrator vehicles are for the benefit of executives, potential funders, and the public at large.
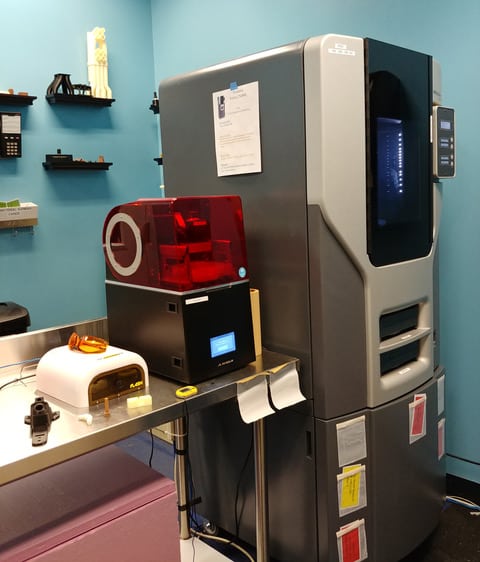
“What we see in the industry today is, manufacturers and players in the market want to put the hardware out there for people and investors to see,” he says. “They need to be able to do this quickly, and in a visually appealing way. Rather than mocking something up and using camouflage, companies are showing off ready-looking vehicles, partly because in some cases it’s about securing the venture-capital.”
Companies offering such services have had to develop methods to produce near-finished quality components, carefully combining the right material with the proper resolution. The importance of the former, says Romack, cannot be underestimated, and represents one of the big limitations that remains for fused deposition modelling (FDM) 3D printing. From a mechanical point of view, he explains, the best performing materials are the ones designed for machines with low resolutions, the attractiveness of which is low – in other words, the resulting parts clearly look like they’ve been 3D-printed. Such parts are ideal for structural uses, in which case they do not play a visual role.
Meanwhile, high-resolution parts with an attractive finish tend to be made from photo-sensitive materials, meaning they become brittle with exposure to UV. The 3D printing industry continues to pour effort into material developments, says Romack, and new materials are released on a virtually weekly basis. Size-wise, dlhBOWLES faces no limitations, says Romack, given that virtually all of its parts are smaller than a shoebox, which is easily within the range of smaller, high-resolution printers.
One development we’re keeping an eye on is hybrid CNC-3D printing machines. These allow you to deposit metal where you like, even at a resolution you may not be happy with, but you can use the CNC to machine it back to shape, giving you the best of both worlds
The other trend in 3D printing which Konrad points to is the use of materials other than plastics, and in particular, steel for rapid tool building. For now, he says, dlhBOWLES remains committed to more traditional additive manufacturing methods, in which the part is built directly on a 3D printer, but keeping abreast of developments remains important.
The company also relies on CNC machining for prototype part production. Like 3D printing, the process uses digital files, but with subtractive methods, using tools to create parts from bricks of material. By now, the process is mature, with the roots of its development in the 1950s, and many companies are now well-versed in its applications.
However, says Romack, in this field, the company also expects developments. “In terms of what we can expect in the years to come, one development we’re keeping an eye on is hybrid CNC-3D printing machines,” he says. “These allow you to deposit metal where you like, even at a resolution you may not be happy with, but you can use the CNC part of the equipment to machine it back to shape, giving you the best of both worlds.”
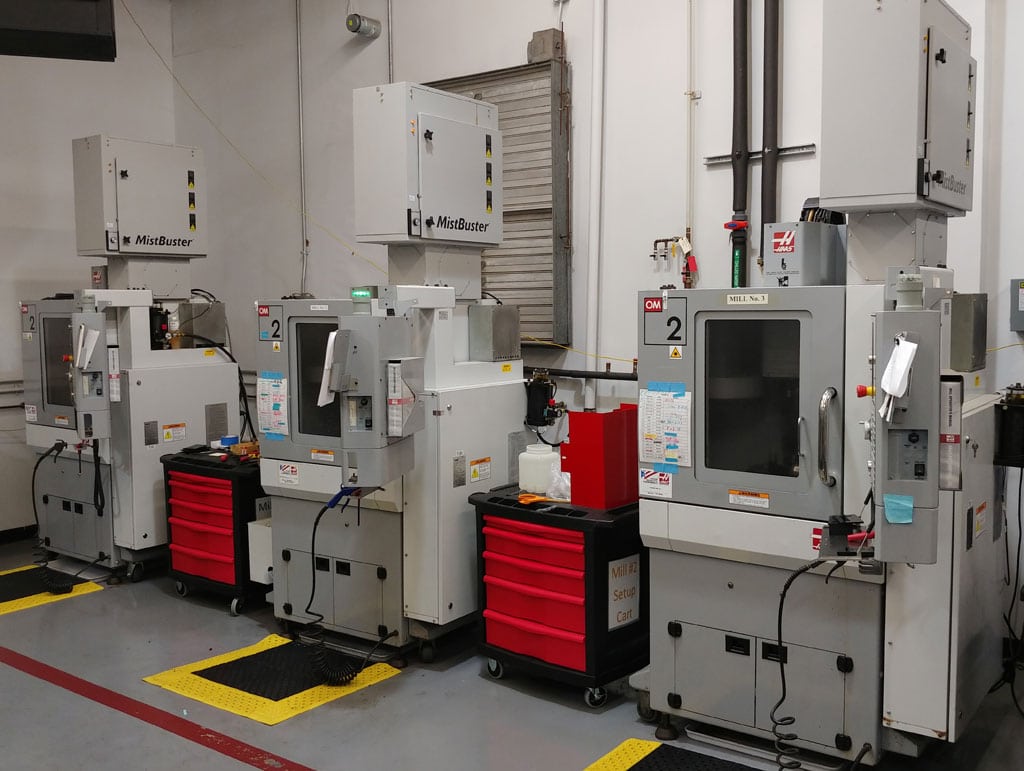
But what is to stop OEMs bringing such operations in-house? Ultimately, says Konrad, the expertise that dlhBOWLES has developed as a supplier means that it knows best when it comes to integration, including how to set up a part, the correct angles for spraying, the correct spray for cleansing applications, and so on. It comes with challenges, one being the capability to work with a customer’s computer-aided design (CAD). Without this, it would be much harder for a supplier to effectively integrate its components within a vehicle’s tight packaging.
Ultimately, says Romack, dlhBOWLES’ own commitment to RP is what enables the company to do what it does. “We have a dedicated lab within the confines of our building managed by the R&D group, so that we have the necessary speed,” he concludes. “An engineer can come to me on Monday morning and ask for parts. In some cases, we can have it back in their hands within as little as eight to ten hours. This is made possible by continuous support from management, and capital to invest in machines. It’s hard to put dollars on time, but there’s nothing like the smile you get from an engineer when, just hours later, you hand them a part they can show their customer.”
This article appeared in the Q2 2018 issue of Automotive Megatrends Magazine. Follow this link to download the full issue