Battery electric and hydrogen fuel cell trucks may be stealing the headlines, but traditional combustion engines still have a long way to go in the trucking space. However, in order to keep pace with emissions targets and customer needs, manufacturers are widely expected to begin pursuing more advanced engine architectures.
In order to reduce fuel consumption, engine manufacturers are already using advanced boosting systems, electrification and waste recovery technologies to downsize and downspeed engines. However, a new approach known as ‘ITES’ has been devised by powertrain development specialist FEV, which combines turbocompounding, electrification and supercharging in a single package.
Along with a reduction in cost and size, this approach has been shown to provide a significant increase in engine efficiency for medium- and heavy-duty commercial vehicles (CVs).
Market trends
Heavy trucks are inherently inefficient, with large diesel engines operating over long periods and seeing single-digit miles per gallon. According to the US Environmental Protection Agency (EPA), medium- and heavy-duty trucks accounted for 23% of all transportation-related greenhouse gas (GHG) emissions in 2016. There are various factors pushing manufacturers to change things.
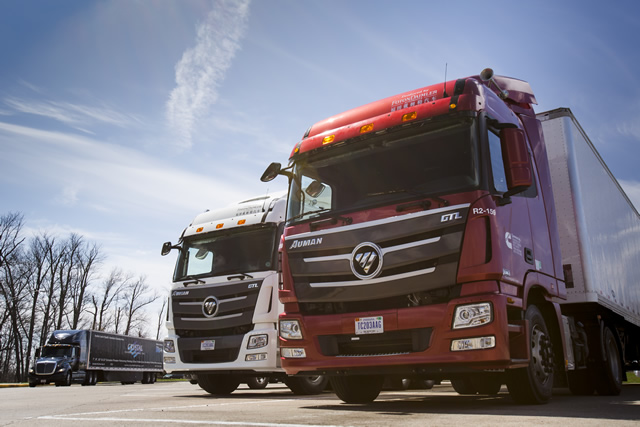
“In the US, GHG and Corporate Average Fuel Economy (CAFE) standards have been pushing manufacturers to increase engine efficiency,” said Satyum Joshi, Senior Engineer of Commercial Engines at FEV during a recent Automotive World webinar. “Customer requirements for annual fuel costs also determine the level of efficiency required. Oil prices impact engine efficiency at a macro level—they determine customer requirements and impact the amount of capital that is invested into engine improvements,” he explained.
On 19 February, the European Commission agreed to pursue a 30% reduction in CO2 emissions from new trucks and buses sold in the European Union by 2030. An interim 15% reduction is also in place for 2025. Earlier in January, the Chinese Ministry of Ecology and Environment voiced plans to rid roads of older trucks that do not comply with emissions standards. China VI fuel standards will gradually come into force between July 2019 and July 2021, at which point all new heavy-duty trucks and buses must comply. It is estimated that by 2030, particulate matter and NOx emissions from heavy-duty vehicles in China will have fallen by 82%.
While emissions regulations and fuel economy requirements are the driving forces behind technology shifts in the CV sector, market competition is also a factor to consider, noted Joshi. “Manufacturers clearly want to have the most efficient engine in the market,” he observed.
Invest in the engine
With these factors in mind, FEV has devised a solution dubbed ITES, which essentially merges a handful of well-known and proven technologies into one package. The idea is to combine the benefits of each system and create a significantly more efficient powertrain. In fact, the solution could go above and beyond what is asked of manufacturers. “We may be looking at even higher engine efficiency improvements than those that are being regulated,” noted Joshi.
He proposes that truck manufacturers could pursue either basic or advanced engine strategies in order to meet targets. In the first scenario, engine efficiency could be improved by the required 4.1%—based on GHG 2 engine regulations—but the remaining emissions reductions would need to be achieved via changes to the rest of the vehicle itself. Alternatively, manufacturers could opt for an advanced engine improvement strategy, seeing a 7% improvement in engine efficiency. This, says Joshi, places less pressure on manufacturers to make changes to the rest of the vehicle, and in short, means that the same engine platform can be more easily leveraged on a global scale.
“The advantage of making more aggressive engine improvements is that because the same engine is applied to multiple applications [around the world], the overall capital that is invested into improving the whole vehicle will be lower,” he explained. “If you want to meet emissions standards globally, investing more into the engine means you have to invest less capital overall.”
Combine and conquer
The ITES system integrates turbo-compounding, electrification and supercharging into one auxiliary component of a medium- or heavy-duty engine. This approach reduces cost and required space, and provides an increase in engine efficiency when compared to the independent integration of each of these technologies.
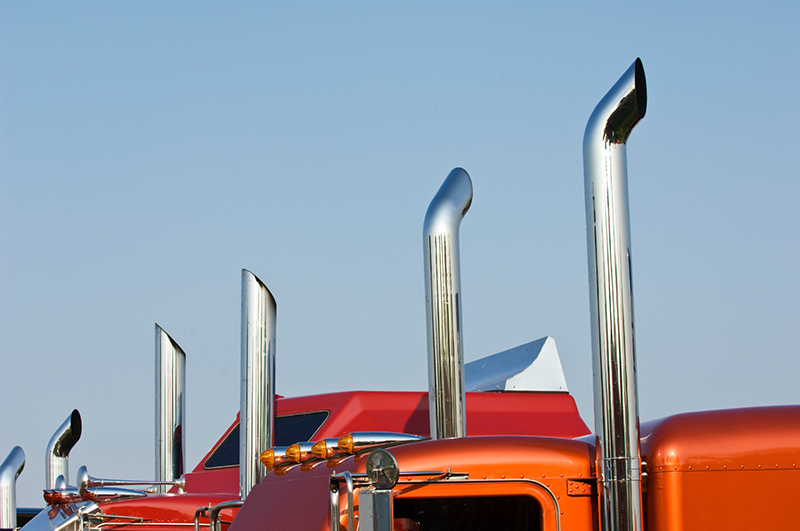
FEV predicts up to 15% fuel economy improvement for a medium-duty truck, based on a Federal Test Procedure (FTP) certification cycle with a downsized engine and ITES system. “It is a very compact package, and in terms of functionality, is able to provide mild-hybridisation, supercharging and turbo-compounding,” Joshi added.
Turbo compounding describes the process in which waste energy is converted back into mechanical energy, and allows a truck to maintain high torque even at low engine speeds. While it has been around for the last couple of decades in the truck industry, the technology dates back as far as the 1940s when it was used to improve the performance of aircraft engines.
To ensure each element runs at maximum efficiency, the ITES system operates in four different modes to cover specific regions of the engine map. For example, certain engine speeds can be targeted to engage the turbocompound turbine and avoid parasitic drag on the engine. At low speeds and high loads, the secondary compressor and power from the electric motor can be utilised. “The ITES system provides a low-cost, small package and high efficiency approach to the integration of waste heat recovery, low-voltage electrification and supercharging,” concluded Joshi. “You maximise the efficiency benefits when integrating these technologies within an engine.”