The recently concluded United Auto Workers strike against General Motors in North America highlighted the broad implications of a tightly knit supply chain and the rapidly evolving nature of vehicle architectures. Much is made in the media of the automation of the automotive industry and its impact on employment, but a more profound impact is expected from the accelerating shift to electrified drivetrains and consolidated electronic control units (ECUs).
The magnitude of that anticipated impact was made clear in warnings expressed by Hyundai Motor’s union chief who warned his worker colleagues that they may face a crisis similar to the UAW adding, according to a Reuters report, that “electric cars were ‘evil’ and will destroy jobs.” To be clear, the Reuters interview with union chief Ha Bu-Young touched on a range of other potential negative influences from flagging sales of particular car models and brands to trade conflicts. But EVs were the focal point, and a hard-to-overlook factor in the context of worsening global climate forecasts and air quality issues.
In the US, the Trump Administration is working diligently to undermine the influence of California tailpipe emissions regulations, which themselves have a global impact on emissions policies. Automakers have been somewhat conflicted over whether to contest the potential unwinding of that California leadership, previously supported in Washington, DC, as it provided some consistent long-term guidance.
To address emissions and fuel efficiency, automakers have been focusing on refining powertrains and emphasizing the lightweighting of vehicles
The even broader issue, though, is the onset of the four horsemen of automotive disruption—Connectivity, Automation, Sharing, and Electrification—known collectively as CASE. (President Trump is arguably the fifth horseman of disruption, adding trade wars and anti-regulation to the mix.)
To address emissions and fuel efficiency, automakers have been focusing on refining powertrains and emphasizing the lightweighting of vehicles. The most extreme case of lightweighting and fuel efficiency may be the Munich start-up Sono Motors, which is turning to solar energy and the liberal use of plastic body components.
The greater impact, though, is coming from changes to vehicle architecture motivated by the onset of electrification and autonomous technology. There is a broad industry consensus that electrification of vehicle powertrains threatens approximately 40% of the total vehicle content of a traditional internal combustion engine (ICE) vehicle.
The onset of automated vehicle technology has been set in motion by companies such as Google/Waymo and Tesla Motors, but the increasing demands of regulators and safety agencies—such as NCAP—are driving up safety content. The growing array of cameras and other sensors on the outside and inside of cars (for driver monitoring) has introduced a requirement for greater on-board storage and faster embedded networks to support sensor fusion applications.
There is a growing need to aggregate sensor data and accelerate the processing of this information for integration with vehicle controls and for communication to the driver in the form of alerts. These demands, in turn, have forced the wider adoption of more powerful SoC processors with all of the implied cost.
To compensate for these added costs, and to capitalise on new vehicle network technologies, car companies throughout the industry are moving rapidly to consolidate the dozens of ECUs in cars. Cockpit domain controllers are rapidly emerging to coordinate the operation of safety systems with driver information and infotainment systems. Elsewhere in the vehicle, so-called “geographic” controllers are emerging to consolidate multiple ECUs into single devices capable of sharing resources such as processing and storage while also reducing vehicle content.
The industry is entering a brave new world of always-connected driving, where automakers and dealers will live with and stand behind cars for the full life of the vehicle on the road
These reductions in content are expected to translate directly to cost savings on components and on production. While the impact is more direct and pronounced on the electrification side, the reduction in complexity in support of safety and collision avoidance-related applications is also significant.
Counter-intuitively, the consolidation and convergence of safety and infotainment systems in support of collision avoidance systems and electrified powertrains will actually stimulate the implementation and deployment of electrical content in cars. Sensors, microprocessors, and the related networks, storage, and software, will see continued rapid growth even as vehicle sales growth tapers off.
The demands for safety systems, often driven by mandates or the requirements to achieve five-star safety ratings, are having a global impact on vehicle design and overall content. This is good news for suppliers that might otherwise be facing unmitigated disaster derived from the reduction of mechanical content.
The shift has put a premium on hiring software developers—forcing automakers and their suppliers to compete with technology companies for the same talent. This hiring tear has, until recently, over-shadowed production concerns, but it makes clear that talent on the factory floor is likely to continue to be deprioritised in favour of the hiring of programmers.
No two automakers are taking an identical path to respond to the demands of CASE requirements. There is ample room for differentiation and for gaining market advantages
Connectivity, too, cannot be underestimated in its impact on automotive design and manufacture. The onset of C-V2X and 5G technologies will require new thinking regarding vehicle gateways and antenna configurations. This is especially so in the context of the convergence of safety and infotainment systems and the need to communicate vehicle diagnostic data.
The concept of product life-cycle management is rapidly taking hold in the automotive industry in consideration of the availability of faster and higher capacity embedded wireless connections. Private 5G networks are already being deployed in factories by companies such as Daimler, replacing Wi-Fi technology which has been found to be inferior.
In the near future, car companies will have full cradle-to-grave access to vehicle diagnostic and performance data to measure and manage the behaviour of on-board systems during production, in transit, while on dealer lots, and in the driveways of consumers. Sensors are being introduced by Tier 1 suppliers such as ZF, Bosch, Continental, and others to monitor the performance of mechanical devices in the car in order to anticipate failures—while wireless connections are increasingly being leveraged for over-the-air software updates necessary to correct system failures or shortcomings.
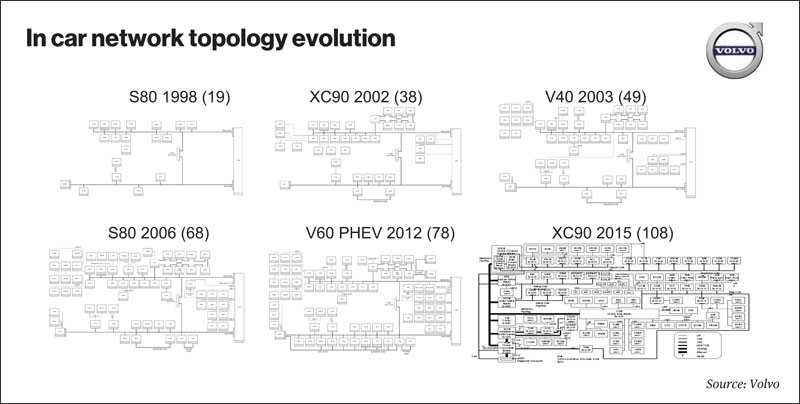
The monitoring and measurement of vehicle performance in real-time creates new demands for vehicle data collection, normalisation, and interpretation. A growing roster of OEM partners are emerging to assist automakers in collecting and interpreting vehicle data.
This new product-lifecycle-centric process of product delivery means that product designers and even the production line are “on the hook” for any issues that might emerge and can be traced back to designers or factory workers. The industry is entering a brave new world of always-connected driving, where automakers and dealers will live with and stand behind cars for the full life of the vehicle on the road.
Of course, connectivity is only relevant and useful if embedded connectivity devices in the cars are provisioned onto wireless networks and operational. Until recently, this was a problem for the industry, with only Tesla Motors and a handful of Chinese automakers offering lifetime connectivity. Volkswagen’s recent re-launch of Car-Net in the US includes five years of free remote access to vehicle functions via the company’s mobile app which will require, of course, that that wireless device in the car is functioning.
Greater impact is coming from changes to vehicle architecture motivated by the onset of electrification and autonomous technology
Live in-vehicle connections mean that automakers can extract vehicle diagnostic data and deliver software updates. At the same time, live connections will allow for cyber security related messaging and monitoring. In this respect, connectivity is becoming a lynchpin in the process of car makers evolving to support more sophisticated solutions and stronger customer relationships.
Until recently, connecting cars was more or less an unnatural act for a car company. Almost overnight, connectivity has come to be seen as essential and transformative to all links in the supply chain.
As with most things in the automotive industry, these changes are happening both slowly and suddenly. Some decisions are driven by regulatory requirements and mandates, others are seen simply as a wise choice to future-proof the industry, the production line, the supply chain, and even the distribution network.
No two automakers are taking an identical path to respond to the demands of CASE requirements. There is ample room for differentiation and for gaining market advantages. The ultimate objective is to produce safer, cleaner, and better performing cars. That is a goal worthy of the sacrifice.
About the author: Roger Lanctot is an Associate Director, Global Automotive Practice at Strategy Analytics
This article is taken from Automotive World’s November 2019 ‘Special report: How will future vehicle tech shape the automaker supply chain?’, which is available now to download.