Currently, 30% of global CO2 emissions are transport based, making electric vehicles (EVs) a key step in protecting the planet. With governments and automakers making a sizeable push to shift to electric, battery production in Europe is expected to grow sixfold by 2030, with similar growth expected in the US. In Europe this would put planned annual capacity high enough to produce almost 15 million EVs—14% of the global total.
Batteries need to be built, though, and to do so they need raw materials. High up on the list of battery ingredients is graphite, which makes up nearly 30% of battery cell mass. Graphite is arguably the perfect mineral to be used in batteries, as it has a magnificent capability—reversibility. It can actually get the lithium ions intercalated as the battery stores energy. When that energy is drawn from the battery, it can reverse it and retrieve the energy in an efficient manner.
The need for graphite presents an issue. Compared to 2018 levels, the global demand for graphite could grow up to 500%, with the bulk of this demand being split between two industries: furnaces used in the production of steel and lithium-ion batteries. The Hague Centre for Strategic Studies (HCSS) predicts that 26% of graphite’s future demand will be for batteries. The large expected increase in the demand for graphite introduces economic, strategic and climate considerations. Despite technological developments and increased production of lithium-ion batteries reducing overall costs by 90%, raw material prices are still set to rise. That means either EV affordability or manufacturers’ margins will suffer, while the economics of large-scale energy storage projects would also be hurt. It will be pivotal to secure raw materials, especially graphite, as the industry accelerates the transition to clean energy systems.
Graphite is arguably the perfect mineral to be used in batteries, as it has a magnificent capability—reversibility
To meet future battery demand the supply chain across the world needs to improve. In order to mitigate risks, OEMs and cell manufacturers are getting involved further and further upstream in what could be seen as a modern-day gold rush. In January Tesla signed a deal to procure 80% of its graphite from one of the world’s largest graphite mines in Balama, Mozambique which is operated by Syrah Resources and more recently secured three years of lithium from Ganfeng Lithium. In a bid to reduce costs and secure supplies, VW recently announced a joint venture with Huayou Cobalt and Tsingshan. GM, Toyota and Ford are all making similar moves, and with US President Joe Biden triggering the Defense Production Act to secure US sources of battery raw materials to ramp up US battery production, this scramble seems set to accelerate.
Importance of raw materials
Mining is a big issue when it comes to the battery supply chain. Raw materials are often located in geopolitically challenging areas, and while the mining industry has the capacity to have transformative effects on local communities and the environment, these can be either positive or negative.
To make matters worse, not all graphite is suited to meet the rising demand. While many different sources of graphite exist, each industry has its preferences. Synthetic graphite is preferred for EV batteries, as they have longer lifecycles and fast charging capabilities, meaning that the market for synthetic graphite will become tighter and tighter as time goes on. Environmental issues are also at play, and could lead battery producers to shift their focus toward natural graphite and new processing methods.
Graphite could experience significant disruptions to supply in the coming decades. Demand for graphite is predicted to exceed supply as early as 2023. There are a few key reasons for this, the first being that the production process is expensive and energy intensive. The graphitization cycle is emission-intensive, due to its reliance on carbon-rich needle coke, as well as the high temperatures needed through processing. Today’s Chinese production process for synthetic graphite is highly energy intensive, and means that it’s harder for manufacturers to justify using materials like synthetic graphite in products promoted as green.
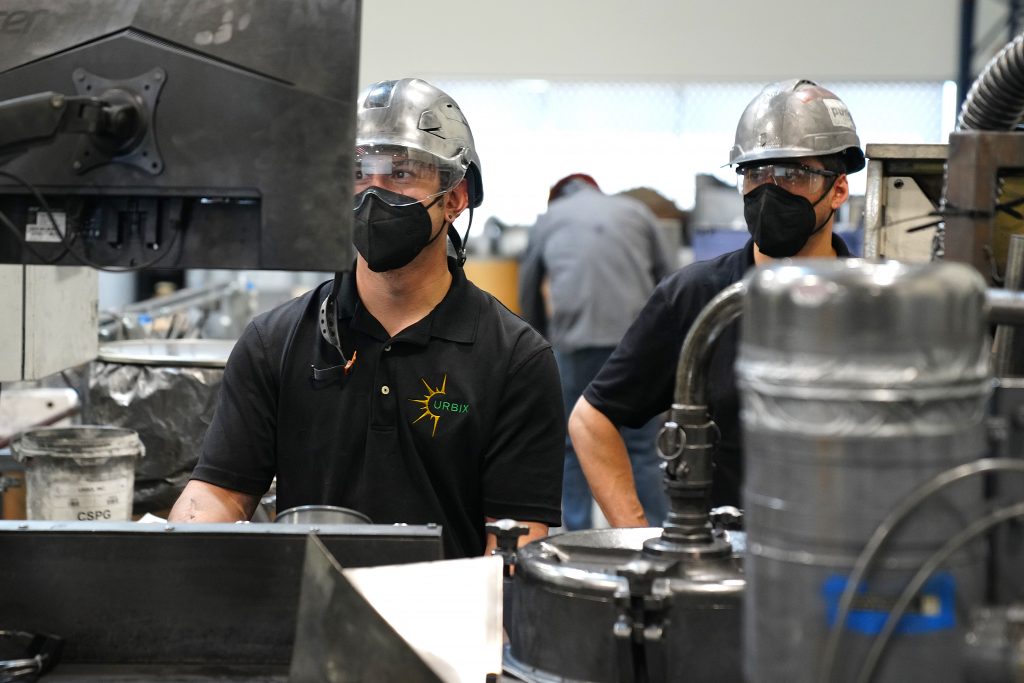
Perhaps the biggest issue with the current graphite supply chain is China’s graphite hegemony. It doesn’t make sense to be reliant on one specific point of coursing for your most critical products, and China has a dominant position across the graphite supply chain, which creates significant challenges for economic powers like the EU and US.
In 2021 China remained the world’s largest producer of natural graphite, with a global market share of 79%. In comparison, Europe only produces about 3% of global natural graphite, with Ukraine being the largest producer, providing approximately half of all European production. China also controls the processing of both natural and synthetic graphite—about 60% of the production of natural graphite anodes and 90% of synthetic graphite anodes are concentrated in China.
Depending on a single country for material supply that is deemed critical for clean energy technology is a significant risk, as China is able to restrict the export of processed graphite— for geopolitical reasons or domestic consumption—cutting off other economic powers from essential graphite feedstock. That poses a worrying prospect considering that as of 2022, the production of purified spherical graphite is taking place 100% in China.
Depending on a single country for material supply that is deemed critical for clean energy technology is a significant risk
The strained critical battery material supply chains, such as graphite, pose a very palpable threat that could potentially delay any green energy transitions. Developing a mine and bringing critical minerals to market is a time and cost intensive process. Graphite is no exception, and an extremely necessary area for improvement. However, US companies such as Urbix, which recently announced plans to expand to the UK, pose a solution to many of the problems with the supply chain. Specialising in processing raw graphite, Urbix is able to produce CSPG (coated, spherical, purified graphite) via a novel processing technique which uses a fraction of the energy, acids (only 6%) and physical space used in conventional Chinese graphite processing plants. This limits environmental impact and energy intensity, while also improving the yield from natural flake graphite processing, from a recovery rate of up to 45% in current methods to more than 72%. This is important as it also bypasses the current situation of creating synthetic graphite in the UK or US, shipping it to China for processing and shipping it back to turn it into battery cells.
Companies like Urbix are the living proof that the West, which may have some catching up to do, does indeed have the ability to become a leader in innovative technical solutions for the processing of critical minerals like graphite, widening the supply chain and adding diversity to the market. With Urbix expanding capacity to 30,000 tonnes annually by 2024, with the aim of providing graphite for anodes in 30% of the US’s and Europe’s EVs by 2030, the current landscape could be poised for a shift towards a more diverse supply. In turn, this diversity will breed more creative and sustainable solutions, hopefully kick-starting a new status quo for the battery supply chain.
About the author: Nico Cuevas is Chief Executive and Founder of Urbix