Incremental change has long been the way of the automotive industry. The widespread development of reliable electric vehicles (EVs) has continued in this tradition, but today EVs are gathering increasing momentum as companies and governments around the world seek to wean themselves off of fossil fuel- based transportation.
The internal combustion engine (ICE) vehicle is a long way from disappearing, but it is expected that EVs will continue to make up an ever-growing portion of new car sales. As this happens, the EV industry needs to overcome a critical challenge: keeping batteries cool enough to function at peak performance throughout the life of the vehicle.
As EVs have evolved, batteries have become more powerful, and today demand more intense cooling regimes than traditional methods like air cooling can provide. Water-glycol cooling systems have been deployed as a replacement for air cooling but present some inhibitive challenges as batteries become more sophisticated.
So, what is to be done to address these thermal management challenges as EVs grow in prominence and importance?.
Heat dissipation in ICEs vs EVs
A comparison to traditional ICE technology is instructive to understanding the inherent challenges in EV thermal management. ICE vehicles traditionally generate significant amounts of waste heat—on average, 40% of the total heat generated helps keep components within the engine operating. The remaining 60% of the generated heat helps heat the vehicle’s cabin and run the catalytic system, among other things.
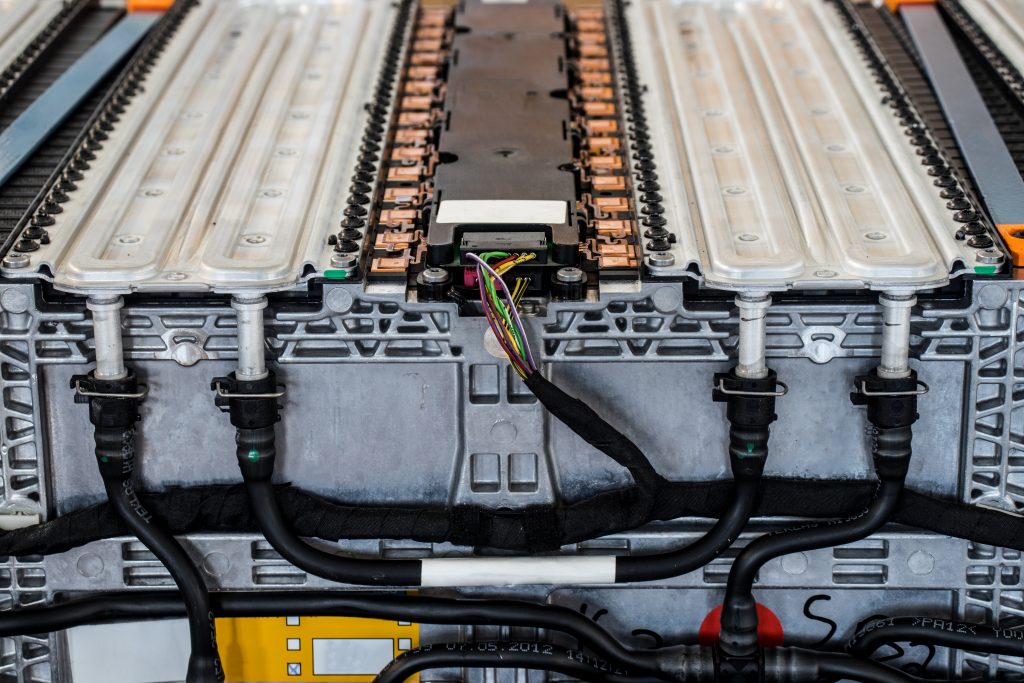
EVs are a different story. Excess heat generated during charging can damage a range of sensitive electrical equipment, all of which is vital to keeping the car in working order. And while EVs run at nearly a 90% efficiency rate and generate far less net heat than an ICE engine, the potential damage can be devastating. The most important concern is safety—an overheated battery is at risk for thermal runaway, which can cause a battery fire. But even if this catastrophic situation does not occur, batteries that are overheated tend to age more quickly, leading to diminished range, power, and overall performance.
Meanwhile, that heat can cause severe damage to the vehicle’s electric motor and power electronics. All of this can lead to potentially dangerous and expensive breakdowns.
Issues with conventional battery thermal management
Many of the first EVs to market used air-cooling methods for thermal management—which were quickly discovered to be primarily ineffective at dealing with the excess heat during rapid charging. They also inhibited the deployment of fast-charging infrastructure, a technology that again caused excess heat buildup. Not only did this pose a threat to the battery itself, but it was a fundamental hurdle to widespread EV adoption—consumer demand necessitates increasingly fast charging times.
Many OEMs quickly migrated to a water-glycol cooling system to contend with the overheating issue. These systems were adapted from comparable ICE systems: tubes are filled with a water-glycol solution, which surrounds the battery pack in the EV to keep temperatures within an optimal range (typically 20-32 degrees Celsius).
Water-glycol cooling proved significantly more effective than air cooling, allowing for faster charging speeds and helping to extend the life of the battery. It was, however, not without its own shortcomings. First, it can’t come directly into contact with the battery itself because water and electricity aren’t compatible. Water leaking from the cold plate or tubing could come into contact with electronics, leading to safety issues. Second, battery thermal runaway occurs when the heat isn’t dissipated properly within a battery pack, causing the battery to deteriorate. Unless the battery is cooled effectively, the temperature within the battery will continue to rise and cause structural and chemical integrity to be compromised. As this happens, an uncontrolled battery fire could result.
For these reasons, many EV automakers are currently working to identify ideal alternatives to water-glycol cooling methods. One of the most promising solutions can be found in immersion cooling.
Immersion cooling and its advantages
Though not yet in commercial production, automakers are exploring how immersion cooling can enhance their EV battery systems. At the simplest level, the technology is exactly what it sounds like. Immersion cooling allows a battery to be submerged in dielectric fluid, enabling a more direct cooling approach than a water-glycol system. No cooling jacket is needed, and the dielectric fluid comes into direct contact with the battery. The benefits are numerous.
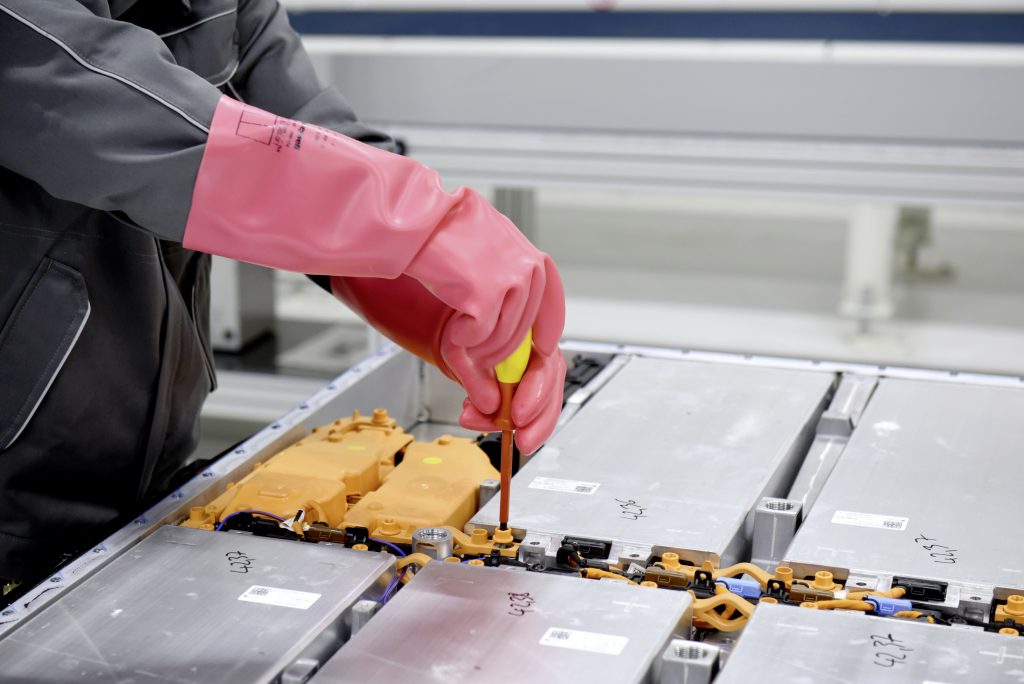
Because the fluid surrounds the battery cells directly, cooling is rapid and immediate if a battery fire does occur, preventing the spread of heat in one cell throughout the entirety of the battery pack and causing other cells to go into thermal runaway. In terms of operational benefits, it helps with prevention of battery degradation due to unexpected cell ageing; quick cooling of battery cells, reducing the chances of thermal runaway occurring through effective heat dissipation; and effective containment should thermal runaway occur in one cell. Immersion fluid will prevent heat from propagating to adjacent cells and avoid a cascade effect spreading within the entire battery pack. It also addresses leak protection—dielectric fluids prevent electrical shorts even if a fluid leak occurs due to damage.
This approach also facilitates high-speed charging. Battery simulations of high-speed charging have been performed to demonstrate the differences between water-glycol and immersion systems during rapid charging. Simulations demonstrated that immersion cooling extended the battery pack’s life by 8% over a water-glycol system and that peak and average temperatures were more effectively controlled with immersion cooling. It was also found to reduce peak battery temperature by 5% over water-based systems and promoted more uniform temperatures throughout the pack.
Lubrizol is working closely with several automakers to develop immersion cooling systems and to deploy them commercially as soon as 2025. Testing has reliably demonstrated its efficacy and advantages over water-glycol systems, and the expectation is that it will gain significant traction as the market for EVs continues to mature.
To the future
Moving forward, it will be important to remember that not all dielectric fluids are created equal, and such fluids will need to be carefully formulated to help these important systems meet their full potential. The next article in this two-part series will discuss what automakers should look for in dielectric fluid formulations and how they can deploy them effectively.
About the author: Andy Richenderfer is a Senior Research Engineer at The Lubrizol Corporation