The complexity of automotive supply chains is unrivalled. Digitalisation, sustainability, and rapid urbanisation have pushed the industry toward electric vehicles (EVs), autonomous vehicles, and a more tech-focused mindset. Now, vehicles are producing up to 5,100 terabytes of data each year thanks to a rapid increase in connected sensors and devices, whilst EVs require a new set of materials and suppliers, in-built tech, and charging infrastructure.
The boom in EVs has changed the automotive industry for good. With global EV sales expected to leap 35% this year, manufacturers are under unprecedented pressure to produce vehicles at speed—with big players like Jaguar Land Rover even devoting entire sites to building EVs. And when it comes to smart vehicles, different bill of materials configurations, remote fixes, and specialist parts have turned vehicles into some of the most technologically advanced and intricate products to manufacture, subject to ever-increasing regulations and customer expectations.
Previously, a lack of integration, poor data, siloed decisions, and a reactive stance created disconnected and misaligned automotive supply chains. Now, manufacturers are squeezed further by the complexity of new vehicles and continual shortages, sparking a move into the new era of automotive supply chains.
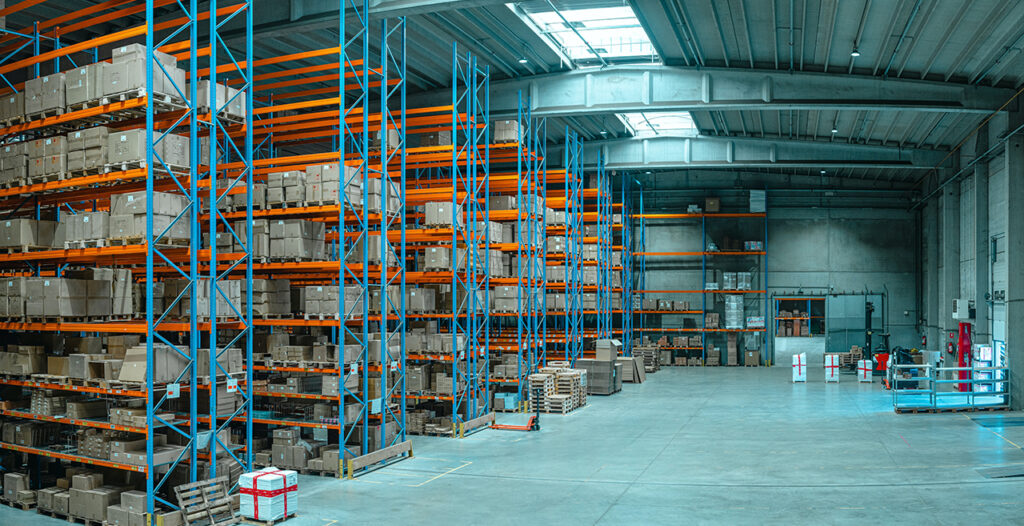
The new wave of complexity
Unprecedented demand shifts and uncertainty extend from the manufacturing stage, to charging stations, to software and firmware updates. Chaotic swings in automotive supply and demand can risk customer loyalty. If vehicles aren’t readily available, customers will head elsewhere, so manufacturers need to ensure a consistent supply.
Poor visibility of inventory across suppliers means poor visibility of supply risk. A single issue among thousands of suppliers over multiple tiers can make even the most efficient production lines grind to a halt. Due to the complexity of new vehicles and the myriad of component parts they require, manufacturers and suppliers often turn to overstocking as a solution. This not only exacerbates shortages but also ties up capital that can be put to better use elsewhere.
With a proliferation of configuration options, a shift from make-to-stock to make-to-order, and the surge in new suppliers for novel technologies, the complexity only grows. With disruptions spanning demand and supply, manufacturers must monitor every stakeholder from systems, components, and materials, right through to dealers, customers, and recyclers. Organisations must build new supplier relationships and have the visibility to ensure that this new complexity doesn’t equate to delays.
Shortages throw a spanner in the works
Shortages of semiconductors and metals for EV batteries continue to plague the automotive industry. In 2021 alone, it lost US$210bn in revenue due to chip shortages slowing down or stopping vehicle production altogether. And when the industry only uses 5-10% of semiconductors, with most going to consumer electronics, automotive manufacturers often find themselves at the back of the queue. Some are even having to pick and choose which features to include on vehicles to try to keep up with demand, leading to costly retrofits to give customers the functionality they want. With no end in sight for shortages, leaders are having to find creative ways to bolster their supply chains and meet demand.
As cars get smarter, supply chains must follow suit
Shortages aren’t fully solved by simply finding new suppliers and creating an even more complex, extended supply chain. More suppliers equal more risk of weather disruptions, port bottlenecks, and labour shortages, and every link of the chain must be closely monitored to proactively handle issues. Some have turned to nearshoring or reshoring to produce parts locally and alleviate these risks, but a lack of raw materials can mean that manufacturers must still source components from further afield—and the complexity continues. Short-term fixes need to be combined with longer-term planning, allowing automotive leaders to effectively balance suppliers and strengthen their supply chain.
The evolution to a connected automotive supply chain
Connecting this plethora of suppliers and stakeholders may seem daunting, but moving to modern, collaborative supply chains is building resilience for manufacturers. It’s no longer about individual suppliers, but their entire ecosystem. A multi-tiered, connected supply chain and supporting technology that brings data together in one platform will help businesses to understand the impact of delays or disruptions and take proactive, corrective action.
Integrating suppliers and trading partners across thousands of organisations, every tier, and various ecosystems builds resilience through secure connected data, real-time information exchange, and collaborative working. This develops trust, confidence, and agility, with accurate, harmonised data enabling decision-grade insights and streamlined regulatory compliance. Connected decisions ensure that the impact of any supply chain disruptions or delays is minimised and proactive steps are taken ahead of time to improve productivity, enhance supply assurance, and reduce lead times.
This visibility feeds into inventory optimisation, where leaders can create aligned plans across horizons that reflect material and capacity availability and make the best decision to adjust. Collaborative planning and enhanced visibility give leaders the data to reduce safety stock and rebalance inventory levels, saving time and money whilst improving forecast accuracy.
As cars get smarter, supply chains must follow suit, and the traditional automotive supply chain no longer drives success. Decades of cost-optimisation, outsourcing, and globalisation made automotive supply chains more cost-efficient but fragile. What worked before no longer stands, and automotive manufacturers need to evolve their supply chains now to be a success in the shift to EVs and smarter vehicles—or risk being left in their competitors’ dust.
The opinions expressed here are those of the author and do not necessarily reflect the positions of Automotive World Ltd.
Mike Hitmar is Director at e2open
The Automotive World Comment column is open to automotive industry decision makers and influencers. If you would like to contribute a Comment article, please contact editorial@automotiveworld.com