The transition to an electric future hinges on battery innovation. Electric vehicle (EV) batteries need to store a huge amount of energy to offer the sort of range consumers are demanding. However, storing so much energy in a confined space poses significant safety risks, including fires, explosions, and the release of toxic smoke. Research teams around the world are hard at work innovating new battery designs, chemistries and formats, and all of them need to be thoroughly tested and verified before they have a chance to hit the market.
Dedicated testing facilities help suppliers and automakers ensure that batteries, cells, and associated electrical components meet all the applicable regulations governing safety, reliability, durability, and performance. With EV sales only set to grow in the coming years, the testing industry will become increasingly important to the future of electric mobility. A February 2024 report from 360 Market Updates predicts a huge growth for the global EV battery testing market, from US$512.26m in 2022 to US$2.32bn 2031.
UL Solutions is an expert in applied safety science, offering testing and inspection services for various markets, including automotive. In the wake of growing interest in EVs, the company expects demand for battery testing services to accelerate. In August 2024, it opened a new testing facility in the Auburn Hills Oakland Technology Park complex near Detroit, the historic home of American vehicle manufacturing.
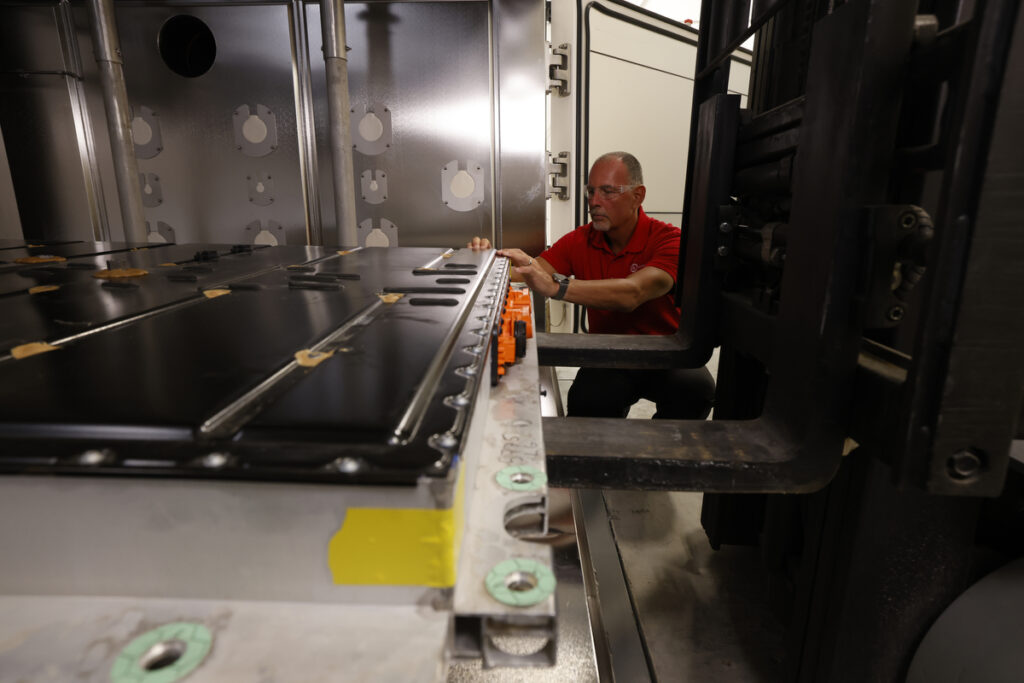
This new 100,000 sq-ft North America Advance Battery Laboratory represents not just the company’s largest laboratory investment to date but also one of the automotive industry’s most extensive in terms of testing equipment. It offers facilities for numerous safety and performance tests, including thermal fire propagation, electrical, mechanical abuse, and environmental evaluation based on various International Electrotechnical Commission standards, United Nations goals and initiatives, and Society of Automotive Engineers and OEM specifications. From UL Solutions’ perspective, this marks a pivotal piece of the supporting infrastructure needed to safely commercialise new battery innovations and speed the transport industry’s energy transition.
Spotlight on fire safety
“For many years we have been helping battery makers on the industrial side, but increasingly we are working with automakers to help prove their battery performance and safety within an automotive setting,” explains Milan Dotlich, Vice President and General Manager of UL Solutions’ Energy and Industrial Automation group. “Fire safety is the biggest part of the lab.”
Battery fires have grabbed considerable headline space over the years. While the number of fires in EVs remains far short of the number of fires in gasoline or diesel models, the severity of fire incidents is what has people worried. EV fires, the result of thermal runaway, burn much hotter and can take hours to extinguish. “This lab has three major test cells where we can run three fire tests at once,” Dotlich tells Automotive World. “No other laboratory in North America can do that.”
As well as fire testing it also offers equipment for vibration, crush, puncture, and shaking tests. In fact, the facility boasts one of the largest battery vibration tables, one of the largest battery crush testers, and one of the largest test cells—50 ft high with four-foot thick concrete walls—in North America. “We can safely test up to a 350kW battery in that space, as well as smaller hybrid or EV batteries,” he notes. “Importantly, we also do this in an environmentally-sound way. Wet scrubber technology outside makes sure there’s no release of any emissions in the event of a fire.”
Keep it local
Governments around the world are keen to build up domestic supply chains to support the EV transition. The Biden Administration’s Inflation Reduction Act has allocated billions towards this end, supporting US-based manufacturing of EVs, batteries and other key components. “There are hundreds of new battery supply chain manufacturers in North America right now due to the incentives on offer,” notes Dotlich. More will likely follow, and many of them won’t have in-house testing facilities in place, or at least not an extensive offering.
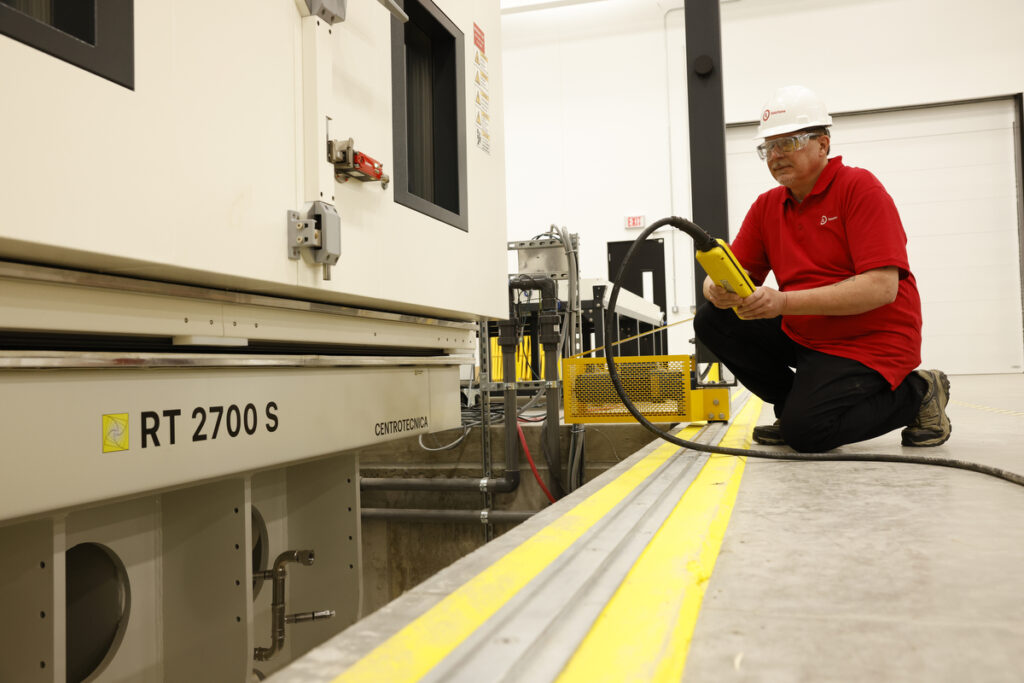
The importance of this new facility in the transition to zero-emission mobility and Michigan’s continued relevance within automotive was evident in the opening ceremony. The event attracted a number of governmental figures, including members of Congress, the Lieutenant Governor of Michigan, the Oakland County Commissioner, and the Mayor Pro Tem of the City of Auburn Hills. Michigan Governor Gretchen Whitmer described the new battery testing lab as a testament to Michigan’s “growing leadership in the future of mobility and electrification.” She added: “With this cutting-edge testing facility in Auburn Hills, we can test the technology we will need for EVs close by to the manufacturing plants where the batteries, cars, and trucks themselves are getting built by hardworking Michiganders.”
This is just one of several such testing facilities in the region, and just one within the global UL Solutions’ network. “With all these facilities, we are helping the world and our customers work through the energy transition,” concluded Dotlich. “We’re seeing the automotive part really start to pick up now, and there’s going to be greater demand—particularly around fire testing—for batteries. We are here to help companies prove their products are safer and more secure.” And in so doing, UL Solutions could help realise an electric future.