Time to market is a long-standing issue in the automotive industry. Between conception and eventual shipment, many complications can take place, including problems during validation and design revisions. The rise of connectivity features and electrification is extending design and manufacturing processes even further. In 2018, global manufacturing firm Jabil reported that only 29% of automakers had product development cycles longer than 24 months. By 2022, however, this had increased dramatically to 96%.
Reducing time to market will lower costs and help ensure that an automaker’s products stay relevant. Ignazio Dentici, Vice President of Global E-mobility and Automotive, Manufacturing Intelligence Division, at IoT and analytics firm Hexagon, believes AI has the potential to transform the product development cycle from end to end. With the increasing complexity of a vehicle’s journey towards eventual mass production, he believes it will become one of the most indispensable tools at an automaker’s disposal.
You cannot get by in modern vehicle design without leveraging data
Rapid advancements
The problem of increased complexity is compounded by a lack of accumulated knowledge about new technologies. “Traditional internal combustion engine (ICE) vehicles dominated the market for a century, and they didn’t change very much during that time,” Dentici tells Automotive World. “Even when testing or validating a new development, how it behaved was easy to predict. With electric vehicles (EVs), we are facing something totally new.” This can protract both the design and manufacturing phases, particularly for OEMs that were initially hesitant about embracing EVs.
During a period of rapid innovation, a slow time to market will not only lead to increased expenses; it could mean a product is already obsolete when it finally ships. Case in point, the range of an EV battery has increased by 10% every year since 2018, according to data from BloombergNEF. The softwarisation of vehicles also leaves OEMs exposed to the pace of innovation in processors and digital offerings. This could lead to design revisions, or worse, a product reaching the market that has immediately inferior performance compared to its competition. “Someone else could be out there with a much faster cycle than your own,” warns Dentici. To stay ahead, automakers must work to reverse the trend and achieve a time to market that is even faster than that of ICE vehicles.
Simulation in design
Dentici believes AI can help automakers increase their speed in the vehicle design phase. “You cannot get by in modern vehicle design without leveraging data,” he explains. “Consider its role in simulation. The more data you can input into a simulation, the more accurate it will be, and the more time you will save.”
Creating a digital twin can allow for most aspects of a vehicle’s design to be stress tested virtually, enabling issues to be monitored, identified, and corrected in real time. Furthermore, incorporating generative AI allows the simulated object to be tested against any number of potential scenarios and feasible object states, which can then be used to iterate on the design and make corrections. This can help mitigate product delays caused by redesigns at a later stage in the development cycle.
Dentici emphasises that more scenarios can be tested in a simulated environment than would be possible in physical prototypes, and at a significantly lower cost. Thermal management of the battery is an area that can take some time to perfect. He reports that OEMs, particularly those new to electrification, have expressed “huge interest” in generative engineering and design to Hexagon. Its potential in the context of battery cooling has already been demonstrated: AI firm Dessia demonstrated a dramatically shortened (3,000% faster) design phase for battery wiring and cooling system channels.
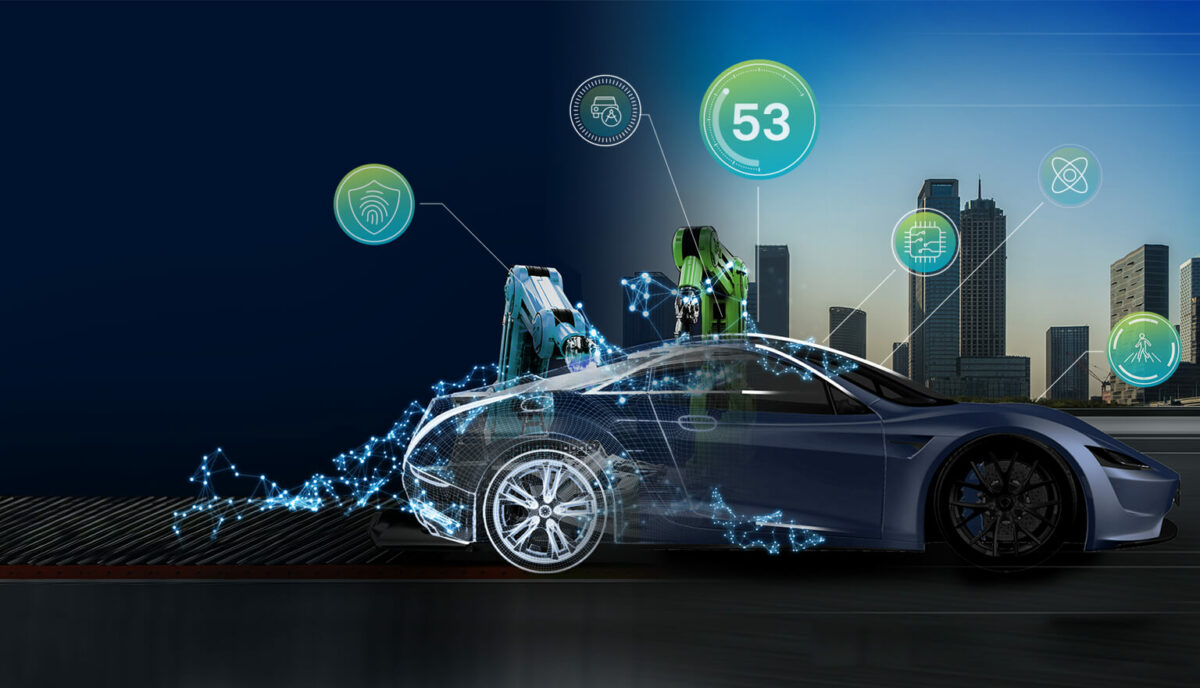
Manufacturing enhanced
“Data has become the new gold for automakers,” states Dentici. However, these are not the only players that can benefit from the data generated during a vehicle’s design phase. “They can also sell it on to the supply chain, helping suppliers understand what an OEM needs in future vehicle generations before an order for a component is even placed.” This can mitigate potential supply issues when going into the vehicle manufacture phase.
AI can also generate insights that increase the efficiency of manufacturing itself. “You need to monitor your existing processes and collect as much quality data as possible to be leveraged at a later point,” Dentici explains. By building models of production machinery, automakers can identify areas where excess energy is generated. Tools such as predictive maintenance and modelling can also be used to optimise machining parameters and reduce downtime.
A number of OEMs and suppliers have highlighted their concerns about manufacturing electric powertrains at higher volumes to Hexagon. Overcoming them will be crucial to meeting the challenge of widespread electrification. “It is paramount for automakers to have key performance indicators in place for powertrain production,” he remarks. “This is a new component for manufacturing at scale, and there isn’t pre-existing institutional knowledge on how to do it efficiently.” To help address the challenges, Hexagon is working on an ecosystem of tools, including on-machine sensors and environmental asset and monitoring systems, to enable better statistical process control during powertrain production.
Preparing for the AI future
While Dentici believes AI can streamline many aspects of a vehicle’s journey to market, its implementation will still be difficult. “The AI revolution will not be easy. Even from a computational perspective, leveraging all this data in the right way is quite complex.” It will take time for automakers to build out the necessary skillsets within their organisations to meet the challenge head on. He adds that many AI-driven solutions for reducing time to market have yet to be realised. “Right now, we have more data than actual applications for it, but that will soon change.”
It is paramount for automakers to have key performance indicators in place for powertrain production
Automakers are already pouring significant resources into leveraging AI. In August 2023, GM invested US$60m in AI and battery materials innovator Mitra Chem. In January 2024, Volkswagen announced the opening of a new AI lab and is currently in talks with various major players and start-ups for potential collaboration. However, resources will also need to be poured into securing talent in an increasingly competitive jobs market. In April 2024, Elon Musk shared that Tesla would raise its compensation of AI engineers—not just to help secure fresh talent but also prevent existing talent from being poached by competitors.
“If you were to ask me what the industry will look like in five years, I’d say there’s going to be a lot of AI in vehicle design and production,” Dentici concludes. “As much money as we’re seeing being poured in right now, it will only increase. By the end of the decade, it’s probably going to be among the top two areas of spending for automakers.” If AI can follow through on its promise to significantly reduce vehicle time to market, then such investments may be warranted.