As electrification gathers momentum in the automotive industry, numerous steps have been taken to ensure vehicles are as sustainable as possible throughout their entire lifecycle. In the EU, for instance, the 2021 ‘Fit for 55’ package mandates greater supply chain transparency and digital passports that provide comprehensive information on a battery’s lifetime emissions. Battery production comprises a dominant proportion of electric vehicle production emissions—McKinsey estimates around 40-60% in research dated February 2023.
However, other avenues for emission reduction exist: curing processes account for 73% of all non-battery related emissions, according to research conducted on behalf of General Motors in 2013. Several attempts have been made to reduce these emissions in recent years, including by Sunstar Engineering, a subdivision of Sunstar Group that, among other things, develops sealants and adhesives for use in automotive. The company believes it can drive reductions of up to 50% through its innovations in low-temperature and low-energy curing solutions.
Less time, lower temperatures
Stephen Howe, R&D Director for Sunstar Engineering Americas, strikes a note of urgency on sustainability. “OEMs need all the help they can get to stay ahead of their targets,” he tells Automotive World. Today’s average vehicle, by his estimate, consumes 1,150-1,500kW of energy curing adhesives following the electrodeposition coating (ecoating—a method of painting that uses electrical currents for surface application), and a further 750-1,100kW curing adhesives and sealants in the paint shop. “Those two processes use most of the energy in a manufacturing plant by far,” he remarks.
Weld bond adhesives are cured alongside the ecoat and can take up to 50 minutes, with ovens running as high as 200 degrees Celsius. To meet the needs of lower-temperature ecoat processes, the company developed a proprietary adhesive technology that can both lower curing temperature and time-in-oven. According to Howe, it can work as low as 130 degrees Celsius, saving up to 50% energy in the body shop.
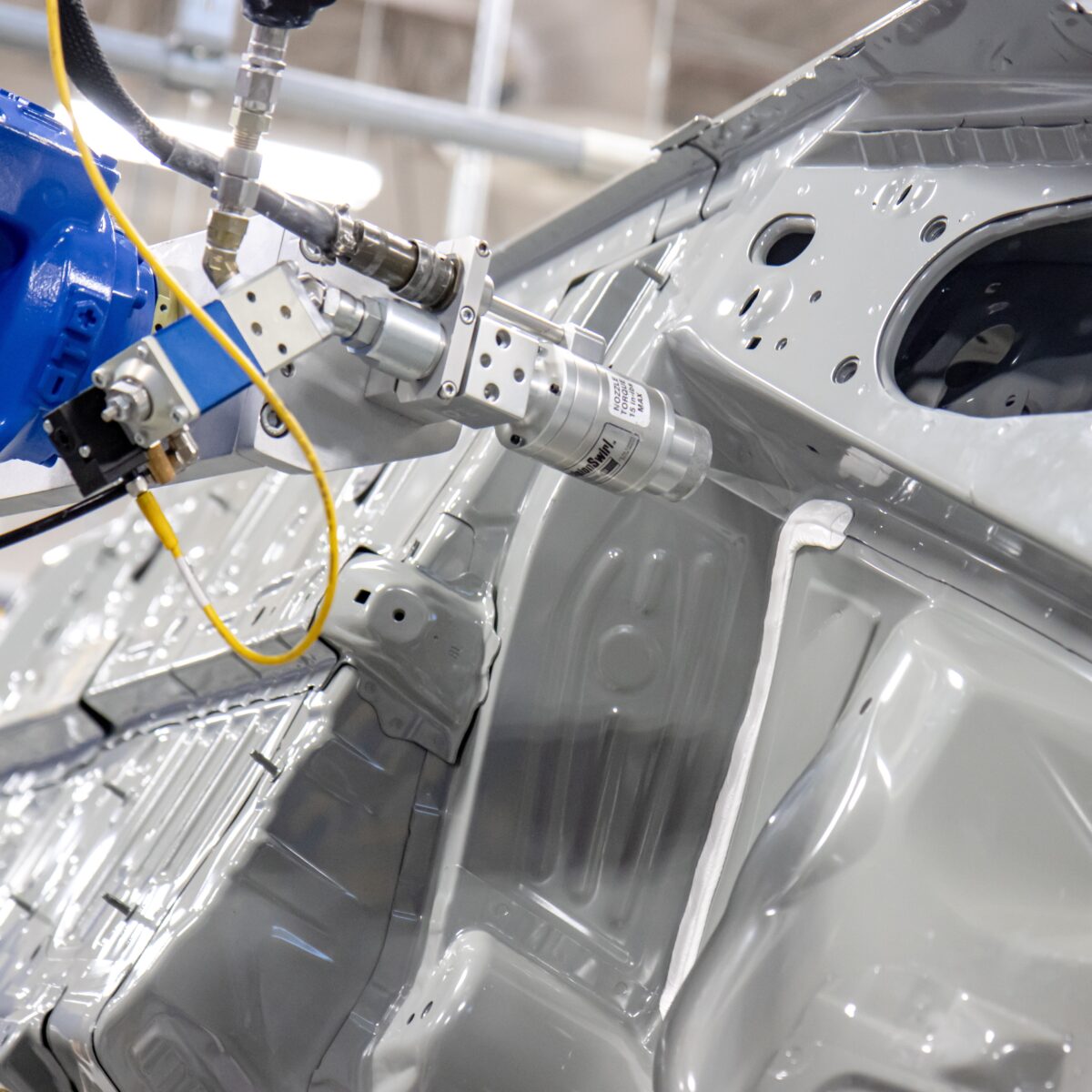
Likewise, Sunstar’s innovations in body sealants aim to reduce overall paint shop emissions by around half. Using one-component PVC sol/acryl sol materials means that multiple wet-on-wet coating applications can be applied quickly and baked simultaneously, saving multiple rounds of oven curing. Furthermore, while paint shop ovens normally run 130-150 degrees Celsius, Howe claims the company’s latest body sealants can be cured as low as 80-100 degrees Celsius.
Lighter is better
The lightweighting of sealer materials is also important for lowering lifecycle emissions. This is, in part, because lightweight materials can be easier and quicker to cure. However, some older generations of these materials have been problematic, particularly those using polymeric glass bubbles to capture and trap air. When sprayed on, the glass would often break, damaging application equipment and costing OEMs their sealant density targets. The weight savings are, effectively, cancelled out.
According to Nicholas Huff, Sunstar’s Team Leader of New Technology Development, many OEMs came to avoid using lightweight adhesives and sealants. “It was far too much of a headache for them,” he remarks. To tackle the issue head-on, Sunstar partnered with 3M (the inventor of the glass bubbles), which improved the crush strength of its glass from 5,500psi to 7,000psi. Once implemented into a new material, the company turned to equipment manufacturers Graco to identify process parameters that would nearly completely prevent glass breakage. “Optimising those parameters, we found, was more important than anything else.”
Lightweight sealers, when properly implemented, help lower lifecycle vehicle emissions by increasing fuel efficiency and extending battery range. According to the Environmental Protection Agency, every 45kg of weight removed from a vehicle leads to 1-2% fuel savings. If adhesives and sealants can deliver reductions on this scale then, “you end up with billions of pounds less CO2 being emitted—just by shaving off that tiny amount of weight.”
Sustainability and affordability
In order to make eco-friendly solutions a viable option for OEMs, it is also important to prove they can offer optimal results at a lower cost. Howe emphasises that Sunstar’s sealants and adhesives meet both of these criteria. While offering equal or superior results to their legacy counterparts, its products can also offer significant savings.
These products could lower OEMs’ energy costs by around 50%
For Howe, the benefits are straightforward: less time and lower temperatures means a lower energy bill. “These products could lower OEMs’ energy costs by around 50%,” he claims. Although energy prices fluctuate from state to state in the US, this could bring per-vehicle energy costs from US$130-$140 to around US$70. When the volume of vehicles an automaker produces per year is factored in, “that’s a whole lot of money.”
Beyond sustainability and cost-effectiveness, the next most important concern for OEMs is customisability. As Howe explains, targets for temperature, weight and sealant density will vary from client to client. As such, a willingness to collaborate is key to Sunstar’s sustainability mission—and to achieving Net Zero within auto manufacturing-at-large. “The future is coming fast. Really—it won’t wait for us,” he concludes.