As the concept of a software-defined vehicle (SDV) expands, it is becoming apparent that the processing power OEMs require for connectivity, automation, and continuous optimisation will be substantial. “When I started in 2015, the market was talking about eight tera operations per second (TOPS),” says Philippe van den Berge, Vice President of EMEA Automotive Business at Nvidia. “Today, we simply don’t know where the limit might be.”
However, a continual rise of compute requirements is one thing of which he is certain—an inevitable consequence of new software, applications, and sensor hardware. Outside of vehicles themselves, the amount of compute required in the cloud to develop algorithms for autonomous driving is so large that it has the potential to cause a data centre CO2 crisis. Nonetheless, as innovators like Tesla build data centres to help advance vehicle artificial intelligence (AI), other automakers with similar goals might have no choice but to follow suit.
Add in the increasingly common requirement for simulation to test new functionalities virtually, and van den Berge determines that old ways of working cannot deliver the full potential of SDVs. “There needs to be a simplified end-to-end platform, and the software pipeline must be seamlessly integrated.” This is what Nvidia wants to facilitate.
Iterating software faster
Although automakers can contribute a piece of the puzzle, partnerships with the tech industry are key. Designed specifically to help automakers achieve automated and autonomous functionalities in cars, Nvidia’s Drive platform has been iterated several times since it first launched in early 2015. It has proven popular among OEMs globally—most recently, in September 2024, Volvo Cars announced that its all-electric EX90 SUV was built on the Drive Orin SoC.
Based on the Ampere architecture, Orin can deliver 254 TOPS, a significant upgrade over the previous generation, Xavier (32 TOPS). Van den Berge calls Orin a “homerun” for companies seeking to do more in the SDV space. “Volvo builds software by itself, but it needs a programmable computer in the car.” This is provided by Nvidia DriveOS, the foundation of the Drive stack, which the company claims as the first in-vehicle operating system of its kind. Using this system, Volvo is not only able to process real-time data from the EX90’s full suite of sensor hardware—including radar, LiDAR, cameras, and ultrasonic sensors—but also enable safety and infotainment features and essential electric vehicle functions like battery management.
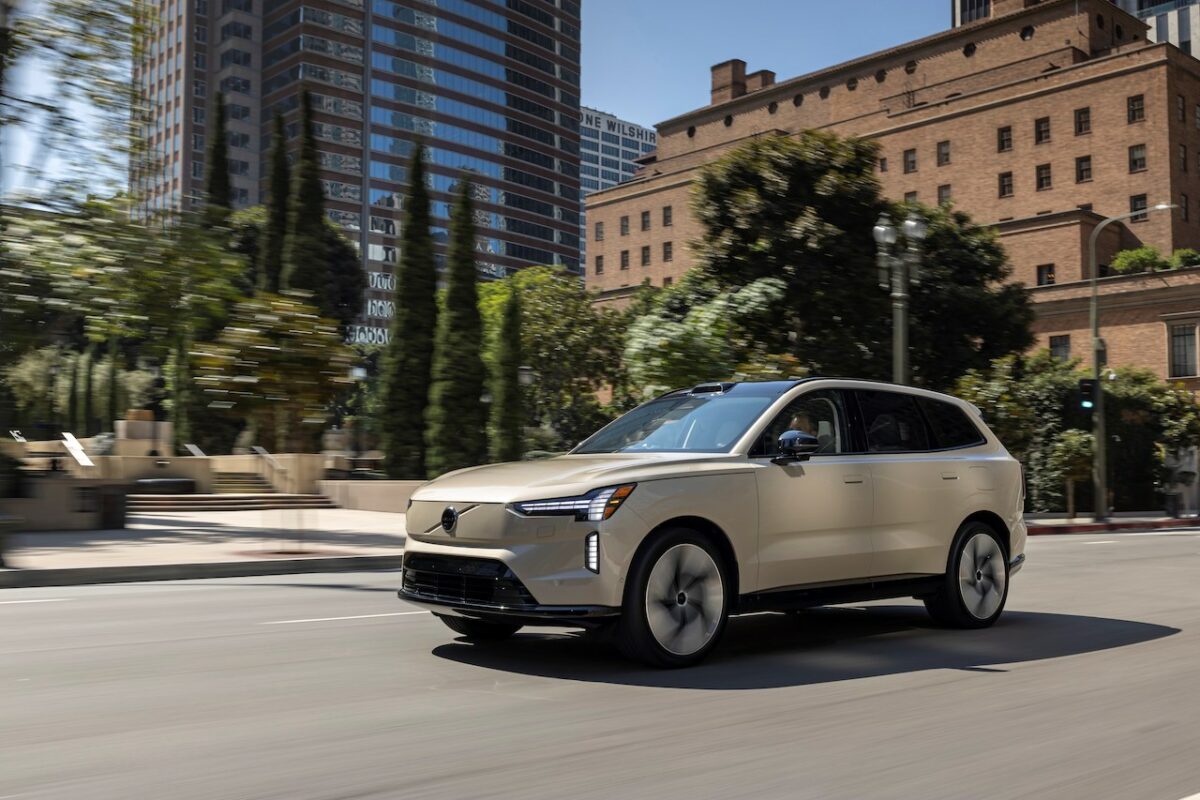
Crucially, the GPU in the Orin SoC and in the cloud are the same, meaning both environments use the same language—Nvidia’s Common Unified Device Architecture (CUDA)—to optimise software. Through this harmonisation, van den Berge states that customers can accelerate both software building and bug fixing. “Developers don’t just want TOPS, they want programmability, too. Orin is already helping automakers around the world iterate their software faster.”
Acceleration and compatibility
In March 2024, Nvidia announced the Blackwell architecture, which forms the basis for Drive Orin’s successor, Thor. Capable of 1,000 TOPS, Thor has already been picked up by Chinese automakers like BYD, Xpeng and Zeekr. According to van den Berge, this is for one reason in particular: generative AI (GenAI). “Blackwell was designed from the ground up with GenAI in mind. Automakers in China are really doubling down on these functions in the car, and although virtual in-cabin assistants are where they’re initially focused, I think the world hasn’t figured out yet where this technology could take us.”
A fourfold increase in vehicle compute power will likely encourage OEMs to explore the periphery of what their in-house software can achieve. However, instead of needing to replace entire systems between generations, van den Berge emphasises the importance of compatibility: Nvidia’s customers can transfer the same software from one generation of hardware to the next. “That’s a big selling point for open platforms; it’s very simple for a customer to port software made for Orin over to Thor.” He suggests this fundamental cultural shift will be important to help keep auto software innovation flowing.
In September 2024, Volvo stated that it will introduce Thor “later in the decade” with a view to future-proofing its products, scaling its software, and accelerating its AI training programmes. Regarding the latter, the company will co-create one of the Nordic region’s largest data centres with autonomous vehicle tech developer Zenseact, a Volvo-owned start-up that will acquire Nvidia DGX AI supercomputers for this purpose. Through deep learning—a type of machine learning that uses complex neural networks to simulate human decision making—Volvo believes Thor will help produce high-functioning, AI-enabled vehicles that are safer and delivered to market quicker than ever before.
Automation in every aspects
Although some automakers’ ambitions for autonomy are becoming highly ambitious, van den Berge states that developing central compute can also bring holistic benefits. Goals will inevitably vary depending on a brand’s desired outcomes, but he has observed that wanting to reduce the number of electronic control units (ECUs) per vehicle—which can run into “thousands” on premium models—is a common trend. ECUs are built for specific tasks like steering and braking, but each one adds both cost and complexity to software pipelines. “When you bring in a powerful central computer, you have the ability to simplify certain functionalities.”
It will take five or ten years for centralisation to pick up, but the industry will see SDV innovation go through the roof when it does
Some ECUs cover simple vehicles functions to which centralisation won’t add much value. However, tackling more complex examples like adaptive lighting could cumulatively simplify the vehicle architecture tenfold. “Bringing functionalities together is the very definition of a SDV, but that can’t happen today because so much of the car is kept separate,” says van den Berge. Therefore, the industry’s goal should be to move towards creating vehicles that operate as one centralised system instead of a “distributed architecture” of many. This will subsequently make automation increasingly more easy and efficient.
In terms of industry progress, van den Berge expects China to lead the way initially. However, the embodied AI approach of UK-based SAE Level 4 system developer Wayve indicates that it might not be a one-horse race. Part of Nvidia’s Inception programme and using Drive Orin—soon to upgrade to Thor—the company is pushing past rules-based autonomy and into self-learning using synthetic data enabled by GenAI. Although these systems are prohibitively expensive now, van den Berge anticipates that this “continuously learning” model could eventually become standard in SDVs as sensors and compute become cheaper over time.
“Overly complex architectures are holding the industry back,” he concludes. “Speaking frankly, cars today are still not very smart. It will take a while for the industry to adopt SDV technology, but there are signs things are speeding up. Once cars are software defined, they will quickly become very smart.” With Drive Thor and its future iterations, Nvidia aims to provide the end-to-end platform that catalyses quantum leaps for in-vehicle automation. “The car will know more about you and tailor the experience to your exact preferences, such as what music you like at what time of day and how loud. We’re going to see automation in every aspect.”