At times, innovation can be seen as a disruptor, and the natural reluctance to embrace change, combined with the perceived risks, can be a barrier to the development and adoption of new technologies. Fortunately, however, innovation can also serve as an enabler, and in many instances can be the catalyst for not just new products, but even the transformation of entire industries.
The automotive industry has reached the latter at this point, and autonomous and electric vehicle innovation is accelerating fast. New models are not only offering more new features, such as advanced safety, autonomous driving, internet access, and infotainment, but their technological agility has allowed them to evolve into an entirely new category: that of software-defined vehicles (SDVs).
Since the introduction of the automobile, consumers have always had to decide which car features to buy before or during the purchase experience. Then, those features were hard-wired into cars, with limited customisation capabilities possible afterward. The car they bought was the car they had to live with, with no additional functionality available outside of costly and often clunky aftermarket features.
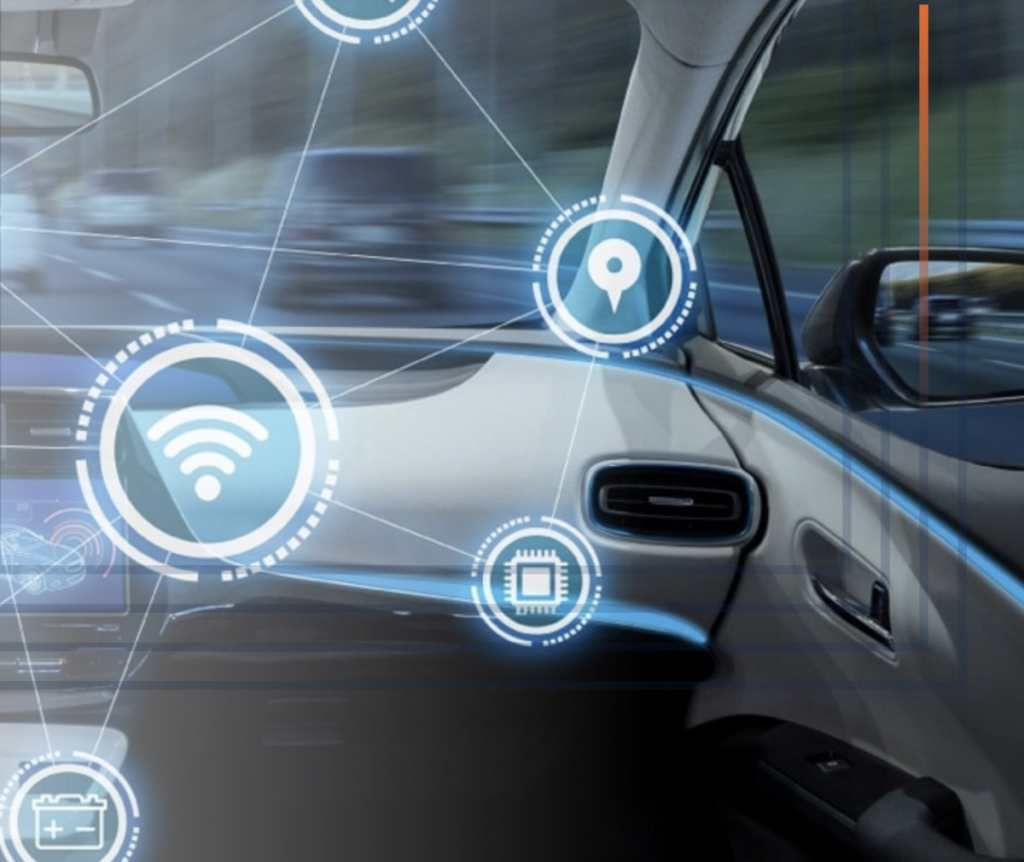
Now, however, that’s no longer the case. With SDVs, a car can be upgraded and enhanced with new functions with the same ease as a smart phone. And that customisation can happen at any time during the car’s lifecycle. Some automotive manufacturers are even developing plans to allow consumers to subscribe to features they may only use seasonally. For example, consumers in cold climates may opt for heated seats year-round, whereas others can subscribe to heated seats for only a few months a year.
How SDVs will change the market
With SDV architectures, car manufacturers can easily roll out new features that engage consumers, drive incremental revenues across the product lifecycle and increase customer lifetime value. So, how will this change how players design, develop, and deploy new solutions?
To start with, the market will drive to simplicity. Today, consumers choose among numerous car models and features. This focus on extreme customisation creates incredible supply chain complexity that can weigh on an auto manufacturers’ profitability. As cars become more software-driven, hardware complexity will decrease. Manufacturers, if they choose, can even offer just three levels of customisation: budget, mid-level, and luxury. Luxury cars will offer a full range of options, whereas mid-level cars will have a moderate number of software-driven application features. Buyers can decide which services they want initially, or add them later on-demand.
As a result, car content will increase, requiring that auto manufacturers deploy more semiconductors, connectors, and wiring. This physical layer will provide greater optionality, enabling consumers to switch on new features via software.
Component manufacturers and OEMs will also need to collaborate to develop electrical distribution systems with a higher level of standardised parts. These parts may be more expensive than the ones in use today, but will offer a higher ROI thanks to their ability to enable new subscription services and revenue models. Component manufacturers stand to gain by offering high-voltage, high-current interconnection systems and auxiliary systems that support the connected systems used by SDVs, with fuse boxes being replaced by semiconductors that manage and control circuits.
There will also be a move by manufacturers to standardise architectures. Today, auto manufacturers work with multiple suppliers to develop car systems. However, supply chain slowdowns and availability issues have negatively impacted manufacturers’ ability to drive throughput, and meet their production goals. In the face of those challenges, it was worth noting that NEV manufacturers in China who own their technology have been able to avoid some of this negative impact and bring innovative car designs to market faster than competitors. Other companies are looking to follow this model. In the future, it is expected that OEMs will control most of the software deployed in cars, enabling auto manufacturers to standardise more of the physical layer and streamline the distribution of key systems.
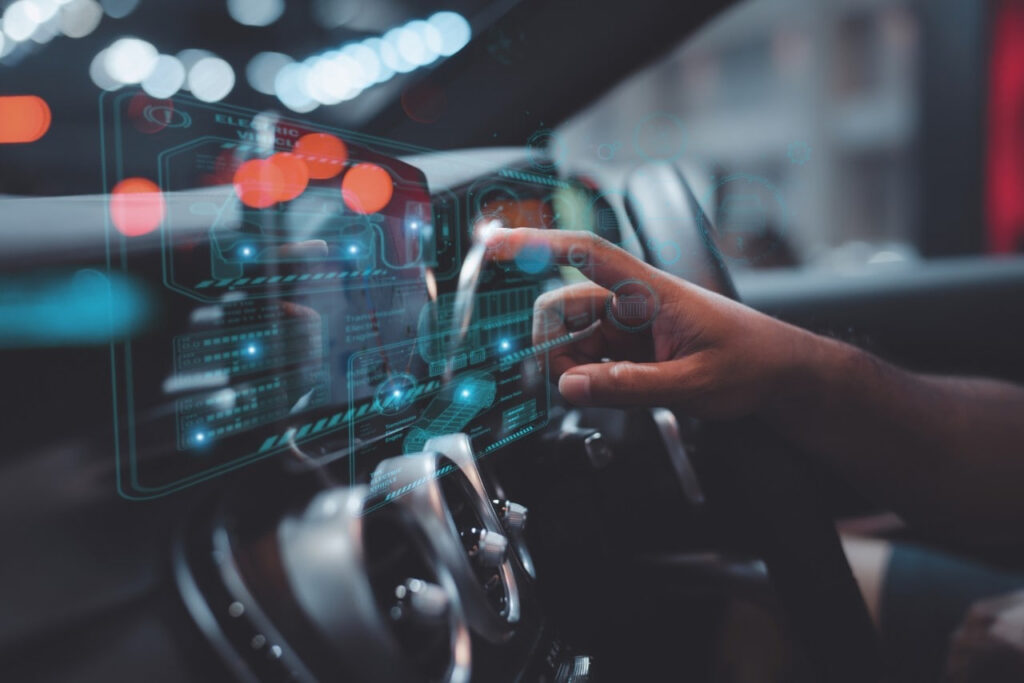
Centralising computing enables auto manufacturers to optimise the distribution of wires and connections, saving on solution weight and cost. Manufacturers can use point-to-point connections that are converging to space-saving jumper cables instead of wire harnesses that distribute power from part of the car to another. As a result of this trend, connector manufacturers will be able to create a greater number of standardised parts in larger volumes, increasing operation efficiency which will enable greater investments in even more innovation.
Another key impact will be that electronics and other components will also become modularised. OEMs are consolidating systems, such as power electronics modules, to create more space in car architectures for other solutions. Companies that supply connectivity should work with partners to develop and evolve solutions that keep pace with new modulariaed designs.
Meanwhile, robotics-driven assembly continues to improve. As harness size and weight decrease, robots will take on more duties on the factory floor. Robots can install new systems at greater rates than line employees without tiring, and with greater quality. Similarly, robots can install connectors with exceptional reliability, meaning component manufacturers can now offer solutions without secondary lock protection. As a result of these innovations, auto manufacturers can drive more throughput, better aligning production with rising customer demand.
Increasingly, data and AI will drive design. In the past, design professionals used consumer research and intuition to develop new models. Now, they’ll increasingly use generative AI to guide the development of standardised models and leverage discriminative AI-powered insights to create the better performing parts, and more innovative car models that consumers want.
Data connectivity is the key
Data connectivity is the tool that binds SDV processes together: from design to development of new architectures to manufacturing and consumer operation of NEVs.
While industry estimates vary, TE Connectivity expects new vehicles to produce more than 30TB of data daily due to the addition of new features like autonomous driving. Car data connectivity solutions ensure data transmission and processing reliability and performance at exceptional speeds in challenging operating environments. To keep passengers safe, NEVs must be able to manoeuvre to other lanes and stop instantly, avoiding potential accidents.
New business opportunities for ecosystem partners
The race to develop and popularise SDVs represents a once-in-a-generation opportunity for vehicle and component manufacturers, which will benefit from standardising and modularising solutions, enabling them to achieve economies of scale with production. Automakers can engage consumers and monetise new services throughout the vehicle lifecycle, unlocking profitable incremental revenue streams.
To realise this vision, industry participants must collaborate closely to develop new solutions and align operational capabilities. The pace of innovation will only increase, and those companies that can transform solutions and manufacturing capabilities at pace will reap most of the market spoils.
About the author: Ruediger Ostermann is Vice President and Chief Technology Officer for TE Connectivity’s Global Automotive Business