The UN’s “Race to Zero”, which calls for halving the world’s emissions by 2030 and for reaching net zero emissions no later than 2050, has captured the full attention of the C-Suite and more than 11,000 organisations have joined the campaign and are committed to its objectives.
The automotive and components industry is taking a leading role, having committed to reducing Scope 1 and Scope 2 emissions by 52.8% over a period of about 12 years. In general, the automotive sector is more ambitious than other sectors. However, fewer companies are committed to Scope 3 than they are to Scope 1 and 2, and for those that are, the targets they’ve set for Scope 3 are less ambitious.
Why are there fewer commitments on Scope 3? Many companies are focusing basically on reducing CO2 emissions for Scope 1 and 2 (the smallest portion of carbon emissions), because they are easier to control and offer a good place to start. Scope 1 emissions are direct emissions from owned or controlled facilities. Scope 2 emissions are indirect emissions from, for example, electricity usage. The bigger challenge, however, is to reduce the Scope 3 emissions which are incurred through an organisation’s entire value chain. This would include materials like resins and metals, as well as transportation, and even packaging.
Facing the Scope 3 challenge
While Scope 3 emissions represent 7.5% of an average firm’s emissions, they can represent as much as 98%of the emissions for an OEM in the transportation industry. Unfortunately, they’re also the hardest to impact, as they occur outside a company’s purview.
The good news is that the automotive manufacturing and components industry has critical momentum for driving change for not only Scope 1 and 2 emissions, but for Scope 3 as well. And the best place to start is with product design, as the choices made during the design phase determine 80% of a product’s environmental impacts. By selecting sustainable materials with reduced emissions, optimising product design, selecting sustainable manufacturing processes and logistics, and more, designing with sustainability in mind can have a major impact on reducing emissions.
While Scope 3 emissions represent 7.5% of an average firm’s emissions, they can represent as much as 98%of the emissions for an OEM in the transportation industry
But even when considering Scope 1, 2 and 3, companies can still go much farther, and begin to become an overall zero emission company by relentlessly seeking to eliminate all types of emissions or waste by defining a true North Star that pushes them to continuously get better each and every day. For example, focusing on a zero-emission framework that encompasses the following five goals:
- zero defect: no scrap, all output produced according to specification
- zero waste of material: all ingoing material goes into the product
- zero waste of water or air: no pollution: all water and all air used comes out the same or better than it came entered the facility
- zero waste of time: all products flow from one value addition to another
- zero waste of human capital: all humans involved gain an improved quality of life while adding value.
Such zero emission company goals should serve as that aspirational North Star, going beyond the mere focus on reducing greenhouse gas emissions to describe an ideal state of pure sustainability devoid of any waste whatsoever.
How to holistically strive toward the goal
So, what does this look like in practice? The automotive industry can work with OEMs and all suppliers along the complete value chain to push zero emission company innovation further and faster than before. Companies can use multiple strategies to reduce the carbon emissions, pollution and any kind of waste.
To start with, manufacturers can determine the current carbon footprint of their products and analyse ways to reduce them. This typically requires precise sustainability data of all potentially utilised material (e.g. resins, metals). Sustainable materials with a low global warming potential (GWP) have to be utilised. The weight of any product has to be minimised, and with waste in the production the aim is zero. Production processes have to be selected that do not pollute the environment.
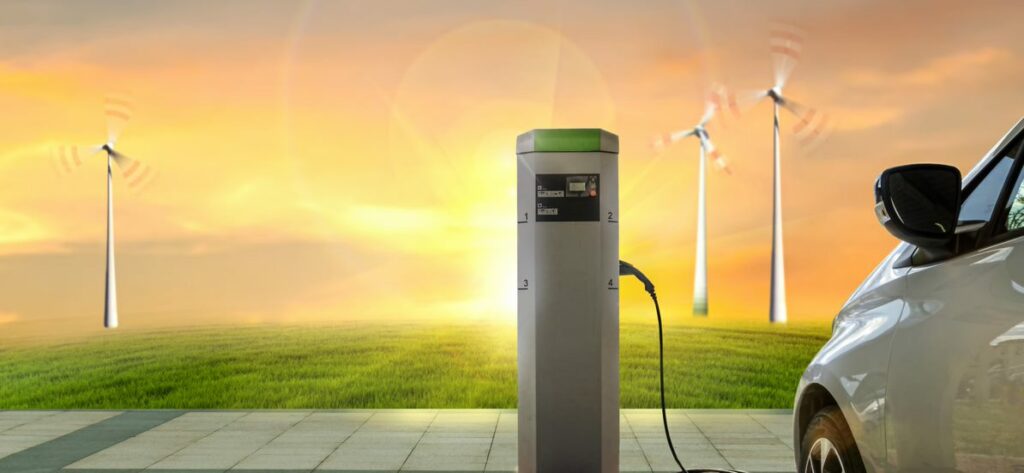
A circular approach to product design is pivotal. Manufacturers can take cradle-to-grave responsibility for products and packaging. That typically means designing products for reuse; collecting and recycling them; re-grinding, re-compounding, and re-pelletising materials; and using these materials to develop new products.
At the same time, manufacturers can use new materials and designs to decrease the weight and size of products. That is already happening in the industry, with the miniaturisation of connectors and terminals that free up more space for advanced systems, making battery electric vehicles (BEVs) more attractive to consumers and helping spur their adoption. Lighter-weight products also reduce storage and distribution costs.
Many companies are developing or sourcing eco-friendly and bio-based materials. These materials include innovative formulations of polyamide (PA), polybutylene terephthalate (PBT), and liquid crystal polymer (LCP) resins that have different moisture absorption and electrical performance qualities. By adopting these resins at scale, automotive manufacturers should be able to reduce their material carbon dioxide emissions by hundreds of thousands of tons.Similarly, metallic plating is being reinvented. Electroplated silver can be swapped for ‘green’ coatings that use fewer precious metals, consume less energy and water than prior solutions, and reduce pollution, while new surface high-voltage plating technologies can reduce the wear and tear on electrical terminals due to fast charging, improving vehicle performance.
Energy-efficient production processes are also key. Manufacturers can map their energy use globally to identify opportunities to increase efficiency. They can then source renewable energy to use at production sites and adopt energy-efficient processes such as turning off equipment that’s not being used, presetting temperature ranges for HVAC equipment, and identifying and repairing compressed-air leaks on processing equipment. A leading automotive components manufacturer used this approach to improve its energy performance by 10% in 2021 and reduce its greenhouse gas emissions by 30% compared to 2020.
When it comes to reducing material waste, manufacturers can optimise production processes to treat every material as a valuable resource, decrease equipment downtime and other problems that harm product quality, and avoid scrap. In addition to running more material on product lines, companies can filter air and purify wastewater, enabling these resources to be used again.
It’s also worth taking a second look at packaging. Here, companies can analyse packaging for components to identify ways to decrease or eliminate it. For example, Suppliers Partnership for the Environment provides 18 different sustainable packaging strategies OEMs and their suppliers can implement. They include building business cases for packaging and logistics, implementing returnable packaging, avoiding using foams in packaging that include spacers and dunnage, and separating pallets and containers, among others.
And finally, manufacturers can consider social factors as they redesign and produce products. For example, automating manual processes can provide a better work experience, improve plant safety, and enhance product quality. Reducing water consumption helps future-proof production processes, while benefitting communities in water-stressed areas. And higher-performance product design can extend the lifespan of components, decreasing waste and enhancing customer satisfaction.
Manufacturers and their suppliers will need to collaborate more closely and innovate more to make faster progress to achieve net-zero emissions. Halving emissions by 2030 and reaching net-zero status no later than 2050 will require a strong collaboration among all companies across the value chain, who will have to join forces and share strategies on the journey to create holistic zero mission companies.
Adopting these eight strategies—and others—can help industry participants reduce carbon emissions at scale, future-proofing their business models and driving new revenues and cost savings from innovative products and services.
About the author: Ralf Klädtke is Chief Technology Officer for Transportation Solutions at TE Connectivity