Air quality in mature economies—particularly in major cities—is beginning to benefit from improvements in emissions technology associated with the latest sustainable electric propulsion vehicles. However, the vision of an emissions-free driving future promised by electric vehicles (EVs) is not quite as free from emissions some might believe.
According to findings from the LOW environmental impact BRAke SYStem (LOWBRASYS) project, brake wear can contribute up to 55% (by mass) of all harmful non-exhaust traffic-related emissions in high density urban environments. These emissions consist of carbon-based particulate matter (PM) which emanates from the fine dust created from braking. And this is as true for EVs as it is for combustion-based vehicles.
Although vehicle exhaust emissions in Europe have been significantly reduced, airborne particle emissions caused by brakes and tyres remain a considerable environmental and health issue, particularly as the overall number of vehicles on the road increases. Every time vehicle brakes are activated, tiny but harmful metal particles produced by the abrasion of the brake pads against the wheel are emitted.
Emission data from the UK National Atmospheric Emissions Inventory (NAEI) estimate that non-exhaust emissions (NEE) are now the dominant source of both coarse and fine particulate matter from road transport in the UK. And automotive particulates contribute up to 20% of all PM pollution in the air, with the rest coming from fires, power plants, construction sites and other industrial operations. The health risks related to the miniscule airborne particles have been extensively studied and it has been demonstrated that they can reach the outer areas of the human lung and therefore represent a severe health hazard. It is especially effective in doing so as PM concentrates in the air close to ground level, at child height. In addition to their physical properties. Brake emissions are typically sized in the PM10 range (that is a 10-micron diameter or smaller). At this size, it is inhalable and similar in size to pollen, but the particulates can be even smaller (at the PM 2.5 range), making it even easier to absorb.
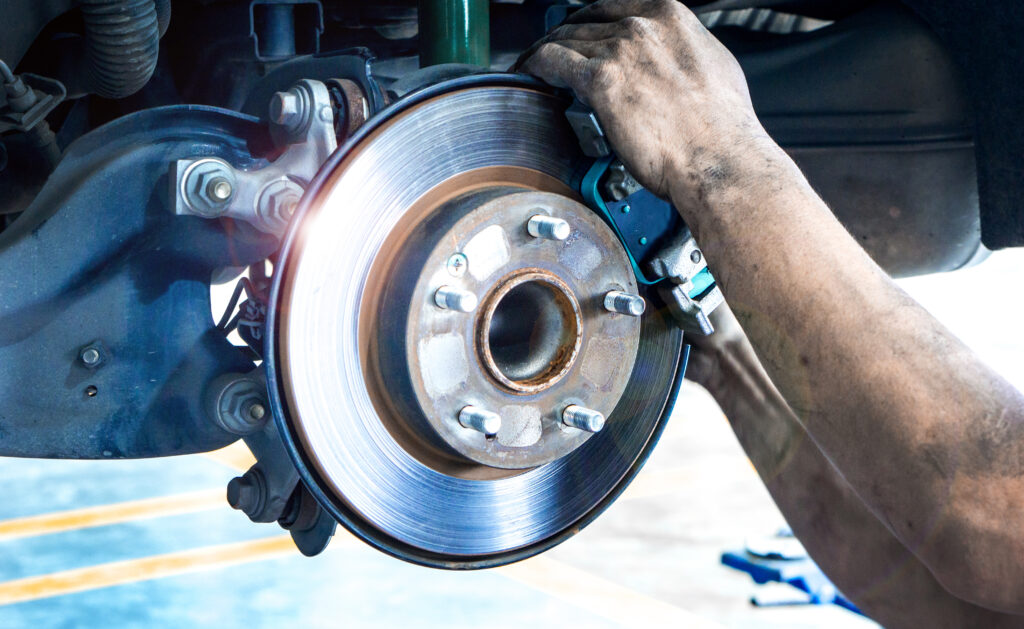
In its 2022 report on air quality, the European Environment Agency (EEA) stated that “96% of the urban population was exposed to levels of fine particulate matter above the health-based guideline level set by the World Health Organization.” It added that “exposure to concentrations of fine particulate matter above the 2021 World Health Organization guideline level resulted in 238,000 premature deaths in the EU 27.”
Dust busting with next generation brake coatings
While the European Parliament has agreed to delay stricter Euro 7 emissions until mid-2030—five years later than planned—there is little doubt that some of the new standards initially proposed in Euro 7 are shifting greater focus on to non-exhaust emissions. In a widely cited study by independent emissions testing company Emissions Analytics, it was found that the greater the vehicle mass and propulsion torque, the greater the amount of particulate emissions. And with the average EV housing half a tonne of battery weight, EV manufacturers will inevitably be affected, despite the recent delay in stricter legislation.
While ceramic brake pads generally create less brake dust compared to metallic ones (and the dust they do create is less toxic), they don’t represent a feasible solution for the average consumer car as they don’t work efficiently until they are warmed up and at optimal functionality. As a result, their use is mainly limited to racing vehicles and some high end luxury and performance cars.
An additional challenge is that due to the regenerative braking systems of EVs, brake usage is typically not as vigorous as found in combustion vehicles. With this reduced usage, metal brakes are more susceptible to corrosion which can impact functionality and safety, potentially resulting in frequent disc changes and even replacement of whole braking systems. The optimal solution to date is to coat brake discs with a combination of a metal alloy and ceramic powder—a very corrosion resistant material combination resulting in a coating so there is little to no resistance.
Thermal management of heat sinks in EVs
As EVs become more powerful and incorporate larger batteries, more powerful systems are needed for better cooling. The most advanced automotive heat sinks—essentially heat exchangers that help to transfer heat from the engine to the external environment—are now typically hybrid models made of copper and aluminium. Traditionally they were made of either pure copper or pure aluminium, but faced either weight or manufacturing issues. While copper can be soldered, it is heavy and results in decreased driving range; for every ten kilos a vehicle can drive one kilometre less. Equally, aluminium while lighter, cannot be soldered, causing challenges to efficient manufacturing.
By spraying a copper coating of between 100-200 microns onto an aluminium substrate, heat sink manufacturers enjoy the positive attributes of both materials—allowing for 30% better performance than aluminium alone. Copper has significantly better heat conductivity, and with the ability of the part to be soldered, heat transfer can be further improved by as much as 20%. The use of a copper coating can also help avoid hot spots that can reduce vehicle efficiency, reduce range and decrease the lifetime of the vehicle due to overheating. And the largely aluminium-based part can still deliver increased range.
While cold spraying of heat sinks has been a common application over the past couple of decades, the spraying of a copper coating onto aluminium is relatively novel. The automotive industry now needs an inexpensive solution that is highly efficient and effective.
Next generation cold spraying for next generation cars
Cold spraying is a material deposition technique where tiny metal particles of between 5 to 50 microns are propelled onto a substrate—in this case the brake—using high-pressure gases. The particles, which begin their life at ambient temperatures, are placed in a nitrogen or helium gas stream which is then heated and accelerated through a supersonic nozzle at incredible speeds of between 500 to 1200 meters per second. During the process, the temperature of the metal powder remains far below its melting point, ensuring the metal particles stay in their solid stage, so retain their unique properties and remain oxidation resistant. The coating created via this process is ductile which also prevents any risk of embrittlement under stress.
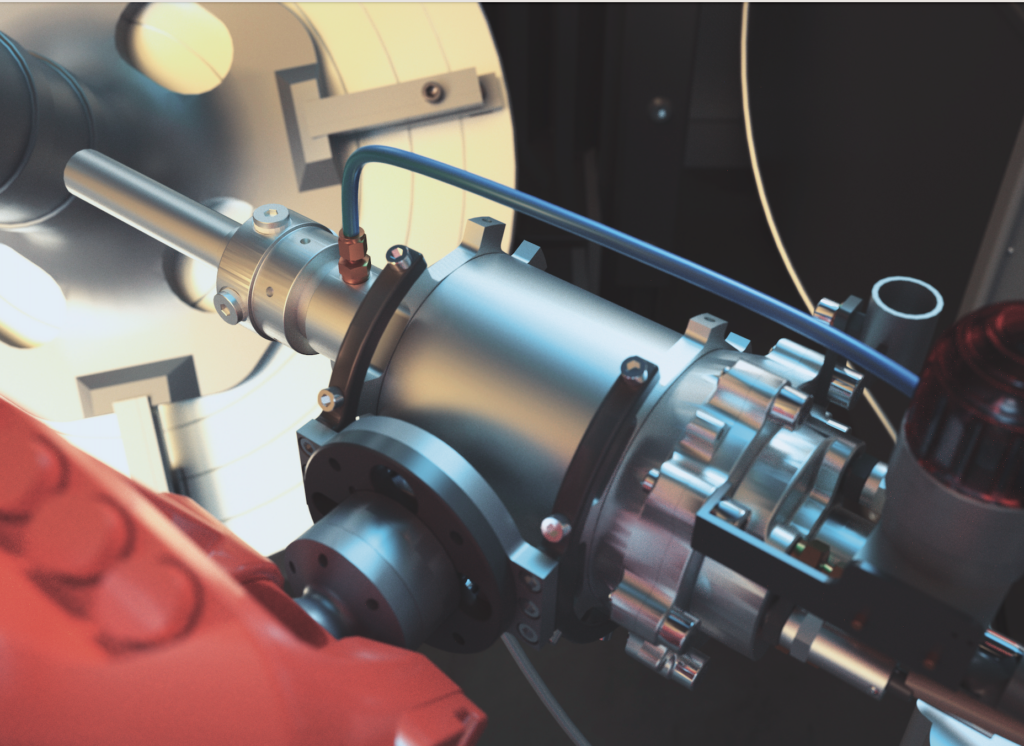
Due to the high temperatures required (up to 1,100 degrees Celsius) within the gas stream, the manufacturing of coated products is heavily dependent on a number of factors, including the supply of high purity gases and a stable and reliable gas flow with minimal pressure variation—all of which must be within a specified temperature range. Rapid temperature changes can damage both the gas heater and the nozzle at the tip of the spray gun. A constant, reliable pressure is needed to ensure a smooth gas flow which will ultimately influence the coating quality. Any fluctuations can potentially have an impact on delivering a uniform coating and ultimately a negative effect on overall product quality.
This is where the Linspray Connect system comes in to play. Develped by Linde in collaboration with German cold spraying technology firm Impact Innovations, Linspray is designed to ensure the delivery of a reliable, stable and high-quality gas flow with minimal variation. The innovative system enables automotive manufacturers to monitor such process parameters as pressure, temperature and filling levels of the nitrogen tank. It also has the capability to automatically send error messages in real time and can switch to an emergency gas supply or activate a safe shut-down of the system in case of incidents. And production volumes can easily be increased or decreased as required.
Such enhanced capabilities will not only enable automotive manufacturers to cost effectively meet new particulate emissions regulations when they do come into force, but can also improve brake corrosion resistance, providing OEMs with a competitive advantage. For EV drivers, it means they can be confident that their choice of electric car can make a real contribution to the reduction of air pollution as well as benefitting from greater driving range and less maintenance.
About the authors: Werner Krömmer oversees Business Development, Manufacturing Industry, at Linde Technologies. Paolo Kirchpfening is Global Commercialisation Manager at Linde Technologies