The manufacturing and distribution of vehicles are some of the most highly complex orchestrations of manual processes and workflows on the planet. One tiny misstep can wreak havoc on every subsequent activity, sending shockwaves up and down the supply chain. The good news is that there are only five ways that manual logistics processes can go awry: location, interaction, count, duration/time and sequence. By isolating the root cause of these five errors and implementing integrated solutions such as a real-time location solution (RTLS), automakers, vehicle processing centres (VPCs), third-party logistics (3PL) and finished vehicle logistics (FVL) providers can solve costly mistakes and minimise supply chain disruption.
The five errors
When distilled down, almost every issue in a manual logistics process can be attributed to one– or a combination of–these errors. A location error, which is the most common. is simply things being in the wrong place. This error is perhaps the most visible and typically manifests as workers being unable to find the vehicle, part or equipment they need because it was not where it was supposed to be. The error of location can also compound issues, having a domino effect. For example, if someone loads vehicle parts on the wrong truck, the cargo will arrive at the wrong destination, causing delays at the location where it was supposed to arrive as well as the location it actually did arrive. Now someone at the receiving location has to sort out what to do with or how to account for the extra items, or spend time rectifying the mistake.
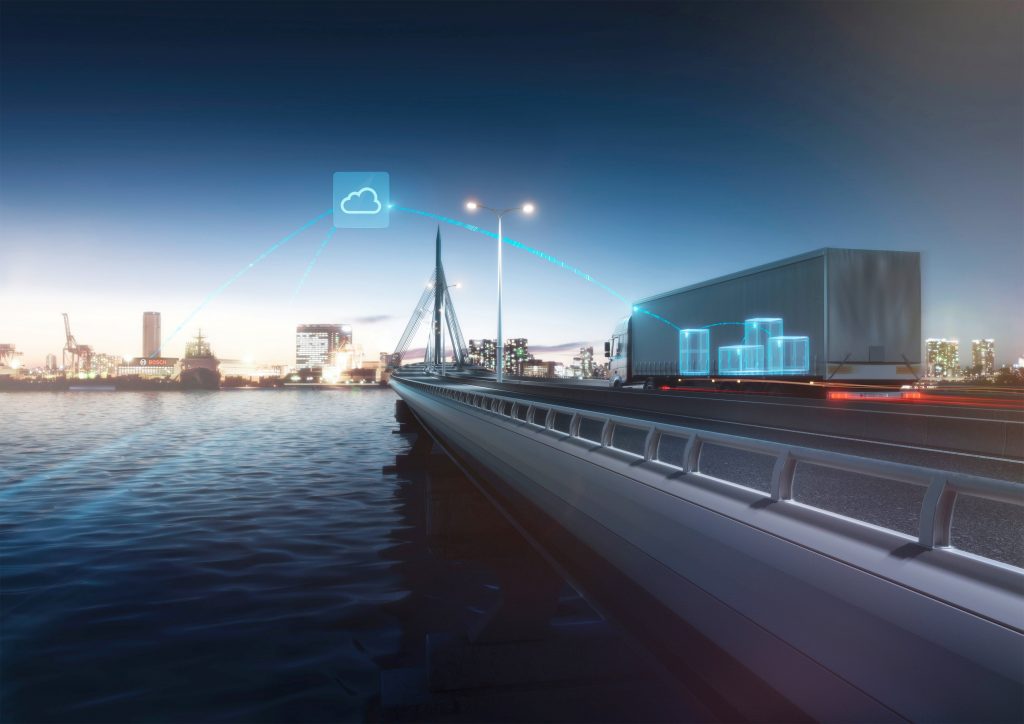
The second common error is interaction—when something is in a place that it shouldn’t be. A good example of this is if a part is loaded into a container using the wrong dunnage, causing the part to be damaged in transit. Next comes the count error—or having too many or too few things in one place—which could include excess equipment or a shortage in parts. Another way to think of count error is if there are more than zero things in a room or space where there should be nothing. A good example of this is if a vehicle is errantly parked in a space that should be empty.
Next comes the duration/time error when a thing is in a place for too long, or not long enough. An example of this might include a trailer at a dock door. Whether unloading or loading, moving too slowly will result in subsequent missed deadlines or even detention fees.
Finally, there is the sequence error, or things moving from place to place in the wrong order. In particular, a sequence error could be an unfinished vehicle accidentally being loaded on a hauler and delivered to a dealer.
The interconnectivity of the five errors
Not only is location the most common, but it is also the error that begets all other errors. Typically, the root cause of one problem stems back to something getting lost or misplaced. Take a blockage issue. If a truck is in front of the wrong dock door it will prevent the correct truck from unloading. While this scenario is technically a location issue, it will ultimately result in a timing issue because if the correct truck can’t unload, it initiates a cascade of ripples or delays in the supply chain.
Typically, the root cause of one problem stems back to something getting lost or misplaced
To demonstrate the interconnectivity of these errors, consider the chain reaction of a damaged vehicle in an FVL yard. With 15,000-20,000 cars moving multiple times a day, it’s not terribly uncommon for a driver to park a vehicle in a place where it doesn’t belong, creating an awkward pinch point that other drivers must narrowly navigate. Unfortunately, one minor miscalculation leaves a dent in the bumpers of both cars. This would likely be labelled an interaction error, but at the same time, it’s possible to label this incident as a location error, too, because one of the cars was parked where it shouldn’t have been. The damaged car will have to go back into the facility to get repaired, resulting in a sequence error since it was supposed to get loaded onto a freight rail. Ultimately, resulting in a count error due to a partial shipment.
Poka-yoke vs flexibility
Attempting to determine where the solution goes in a complex supply chain can be overwhelming. Take a puppy with a bad habit of stealing slippers. Should the owner hire someone to find the slippers or should they train the puppy to stop stealing the slippers in the first place? The traditional view of such a logistical challenge is a solution known as poka-yoke, a Japanese term originating from the Toyota production system, which means “mistake-proofing.” With poka-yoke, an operator creates a scenario where it is impossible to deviate from the set process. However, this method eliminates flexibility, which, in turn, makes responding to change an impossibility too.
Establish processes that are rigorously adhered to whenever possible, but elastic enough that they can be flexible when the unexpected arises, because it will
While it might be nice to prevent location errors from ever happening, the downside is that it becomes impossible to react to unexpected situations where the only solution is to depart from the set process.
An alternate solution is somewhere in the middle. Establish processes that are rigorously adhered to whenever possible, but elastic enough that they can be flexible when the unexpected arises, because it will. The key to achieving this flexibility: visibility. Recall that almost all logistics errors are meta-problems of location. Instead of hiring more employees to search for missing vehicles, OEMs and VPCs can implement an RTLS solution, empowering them to know where their vehicles are at all times. That in and of itself will provide a productivity boost, but the true magic of RTLS results from gaining new levels of visibility into processes. If you cannot see it, you don’t know how well a process is performing. RTLS fixes that, and enables the flexibility to respond confidently to supply chain challenges.
Considering the utter chaos afflicting the global supply chains today, automakers and VPCs can easily minimise the five errors that disrupt manual logistics processes through the use of RTLS. If evaluating RTLS, an ideal asset-tracking solution should be able to meet these three criteria: lightweight and easy to install; provide an accurate, current location for every tracked asset (not just the last time it was scanned or driven by a reader) as well as its movement history; and the vendor should be able to produce a hard-dollar ROI model that proves its value. In a post-RTLS implementation world, OEMs and VPCs will have visibility and insights that help prevent location errors from snowballing into disasters. Moreover, they will experience the true value of RTLS technology, not just finding lost things but ensuring that everything is always where it is supposed to be.
About the author: Adrian Jennings is Chief Product Officer at Cognosos