What zero-emission powertrain will be the successor to diesel in the trucking sector? Since the economy and infrastructure necessary for hydrogen to play a significant role are still nascent, many truckmakers are investing heavily into more readily available battery-electric technology. Valued at US$2bn in 2022, the global electric truck market is forecast to be worth US$20bn by 2032, according to Precedence Research.
However, in doing so, OEMs and carriers must temporarily reconcile the need for zero-emission transport with trucks that cost more, carry less, travel shorter distances, and require new operational planning strategies. Battery-electric truck driveline systems are ripe for innovation, and recent developments suggest the limits of the technology haven’t yet been reached.
Unlocking range through e-axles
In 2022, Volvo Trucks began producing the FH Electric, a heavy-duty truck with 44 tonnes gross combination weight, up to 490kW of power, and 300km of range. Jonas Odermalm, Vice President of Electromobility Product Management at Volvo Trucks, notes that this specification has largely been “sufficient” for most customers. However, it still restricts the vehicles to short- and medium-haul routes. In September 2024, the company announced a new design to expand the model’s addressable market to include long-haul, generally considered routes 400km or greater.
To boost the FH Electric’s range, Volvo Trucks initially homed in on e-axles, which enable manufacturers to make significant weight savings by consolidating driveline components into the axle structure. “With an e-axle, there is no need for a driveshaft thanks to very compact integration of electric motors, transmission, and rear axle,” Odermalm tells Automotive World. “This frees up space for more batteries onboard.” Developing its e-axle allowed Volvo Trucks to add up to eight batteries instead of the previous generation’s maximum of six. Odermalm adds that the company also “improved” its lithium-ion batteries to boost both energy density by weight and volume, although he does not reveal what specific changes were made to the chemistry.
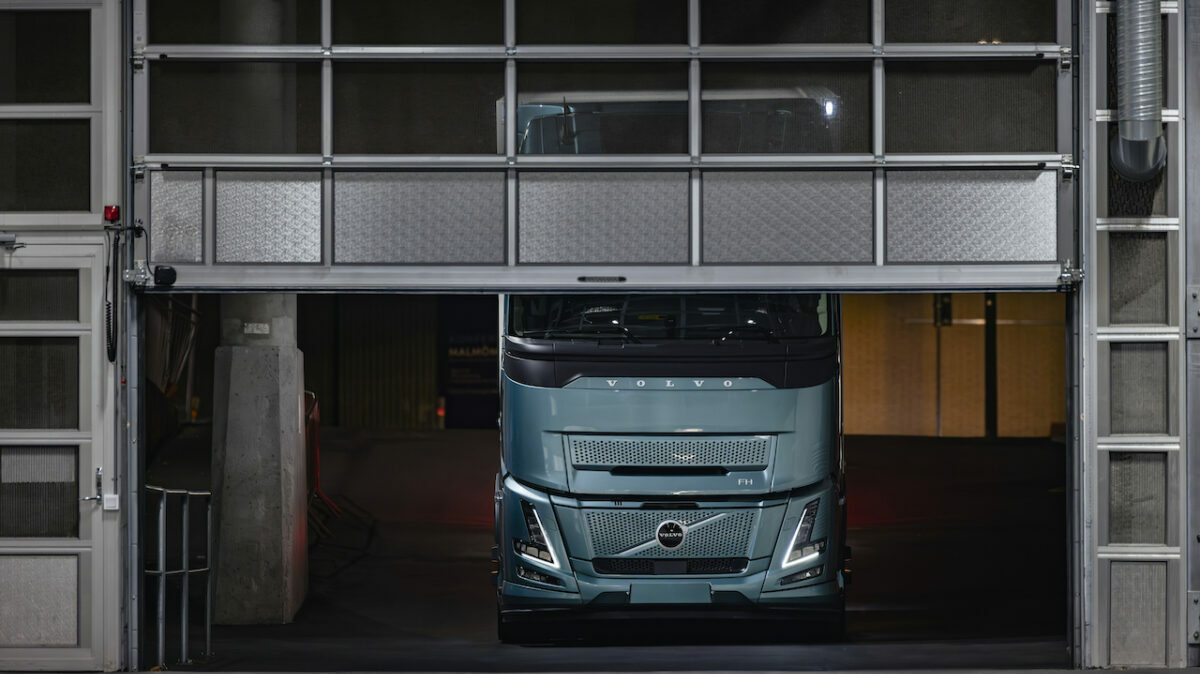
By combining these new batteries with increased driveline efficiency and an improved battery management system to achieve more optimal energy use, Volvo Trucks claims it has doubled the FH Electric’s range to 600km from a single charge. This new version is expected to be sold in conjunction with the 300km FH Electric from H2 2025. Further details will be withheld until production is completed. While Odermalm doesn’t confirm whether the findings will be applied to other electric models, he hints that Volvo Trucks is “continuously developing and improving” its portfolio.
Flexibility through e-drives
While Volvo Trucks is actively working to make electric trucks as versatile as possible, it has generally been reluctant to commit to any single powertrain. Instead, the company is developing multiple technologies in tandem, including cleaner internal combustion engine (ICE) systems, leveraging its significant resources to do so. Other manufacturers may not have this luxury.
Winfried Gründler, Senior Vice President for Driveline Technology at ZF Commercial Vehicle Solutions, informs Automotive World that the truck industry is at a crossroads. With no alternative capable of delivering the equivalent range and performance of ICE, truckmakers want to keep their options open without falling behind. “The future of zero emission drivetrains will therefore be a mix of new technologies,” he affirms, but the exact timeline for change inevitably varies between companies. To balance the need for change with their desire for an appreciable return on investment, flexibility needs to become a tenet of design.
In September 2024, ZF announced a new electric central drive—the CeTrax 2 dual—that enables OEMs to produce electric models while minimising overall changes to their existing platforms. ZF’s e-drive offers 380kW of continuous power, suitable for heavy-duty vehicles up to 44 tonnes, and includes two integrated 800V silicon carbide inverters and an integrated three-speed gearbox with e-actuators for optimised efficiency. Designed to fit the same mounting space as a conventional ICE transmission, the e-drive can facilitate a more efficient transition by keeping truck production lines broadly the same. By adding this flexibility, OEMs can more easily manage the gradual ramp-up of battery-electric trucks without sacrificing the profitability of their core ICE business.
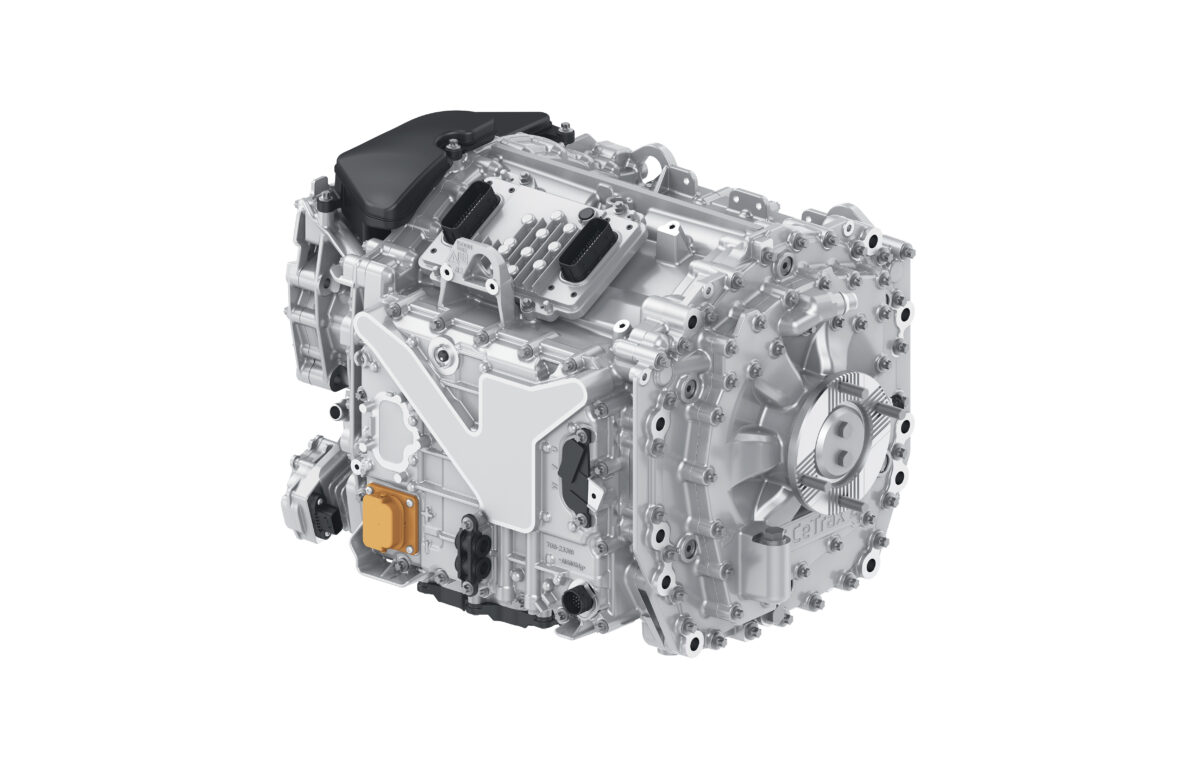
Ford Trucks will be the first to integrate the CeTrax 2 dual for its Electric Rigid Truck model, but as interest in e-mobility technologies continues to grow, ZF expects the production of e-drives for commercial vehicles (CVs) to double by the end of 2025. Gründler particularly anticipates greater adoption of e-drive systems in the Asia-Pacific and North American markets, where more varied and intense CV usage could make a full transition to battery-electric models impractical in the near term.
Creating a smoother transition
“With electric trucks, it is important to look at the transport assignment and the job it must do,” says Odermalm. “You do not want to carry more batteries onboard than needed.” Rather than simply make the revised FH Electric into a standard model design, Volvo Trucks will work together with its customers to find the right product for their use cases. Flexibility and receptivity to the market is key, and this is also ZF’s perspective with the CeTrax 2 dual. By offering versatile drivetrain solutions that meet specific trucking applications and business objectives, Gründler believes fleets and manufacturers can enjoy a smoother transition to zero-emission transportation.
There is a consensus in the trucking community that a unified commitment to decarbonisation will necessarily underpin any hope of that mission’s success. However, while OEMs, suppliers and carriers have made significant progress, the scale of the challenge means there can be no ‘one-size-fits-all’ solutions. “The industry is undergoing its greatest transformation since the invention of ICE,” concludes Gründler. Rather than a linear pivot from one paradigm to another, it could be the gradual improvement of adaptable electric systems that finally enables truckmakers to move away from ICE.