The way the world builds cars has always been driven by breakthroughs in technology. From the conveyor-belt production lines of a century ago, to the robotics revolution, each advancement has transformed car manufacturing. Today artificial intelligence (AI) is changing the process once again, but this time the technological advances are not limited to the factory. AI-assisted cameras on production lines detect defects faster and more accurately, and smart cameras are used to keep employees safe. At the racetrack, machine-learning algorithms are empowering race teams with the split-second data they need to win, and dealerships are using AI to offer convenient and more personalised services to their customers.
For leaders in the sector, the benefits of AI are real and measurable. Solutions like ‘smart’ AI-assisted cameras are enabling employees to be freed from repetitive tasks in production, such as routine inspections and delivery tracking, and instead be deployed elsewhere with the ability to use real-time data to make faster decisions. AI systems are also enabling manufacturers to cut workplace accidents, increase output quality and cut machine maintenance costs. But sector decision makers need to choose their AI partners carefully, integrate AI into their processes effectively, and listen to their own teams to ensure they choose an AI solution which will work for them.
Finding insights faster than a superbike
One of the key advantages of AI-powered tools is speed. Finding the golden nugget in a mass of data can now be automated, letting teams react faster than ever before. Nowhere is speed more important than in racing.
For example, the Ducati Lenovo Team in MotoGP often has just a few hours between track sessions to analyse data from the last one and make decisions about how to configure their bikes for the next one. Barrelling along racecourses at up to 220 mph, each Ducati Desmosedici GP bike is armed with about 50 sensors, allowing Ducati Corse to collect a total of 100GB of data every race weekend from their eight bikes racing on track. This is then processed by AI-optimised edge servers powering Ducati Corse’s machine-learning and deep learning tools, which can offer insights into everything from the type of tyres to be used up to the best trajectory to follow in a specific corner. These AI-powered insights are also making the riding experience safer, with direct consequences on the consumer facing side of the business. The design of Ducati’s street bikes such as the Panigale V4 are designed with the help of AI-developed riding simulations which are also informed by the data collected from the race team.
More efficient manufacturing
When it comes to building consumer vehicles, AI-powered analytics can perform certain key production-line tasks more efficiently than any single person. Manual and visual checks are necessarily slow, and always carry the risk of human error. Even the best-trained human eyes can miss defects which could carry a safety risk. By contrast, automated checks run constantly, and are more reliable, catching defects at each stage of the process, freeing assembly line workers to focus on their core tasks.
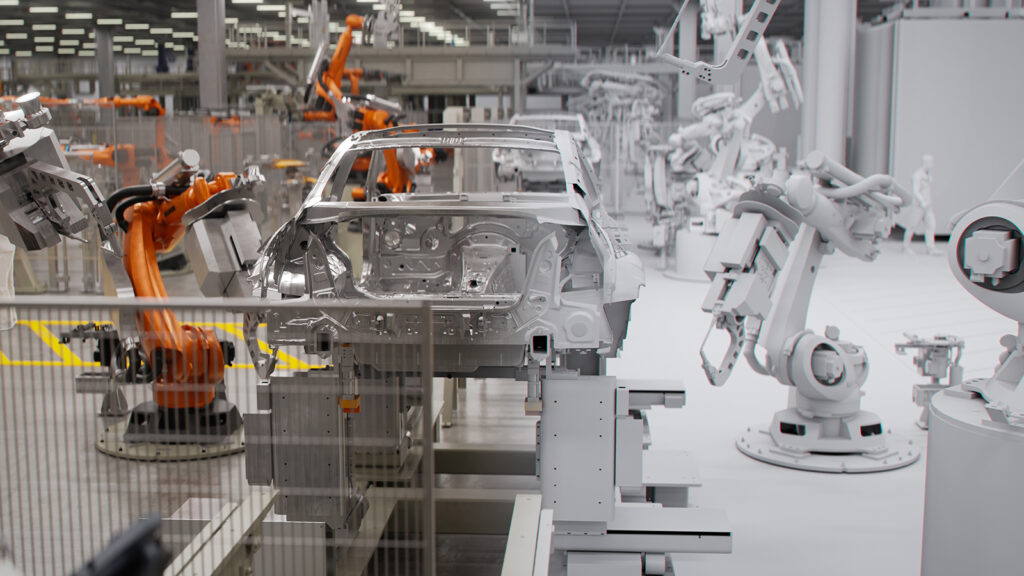
For example, Lotus Group’s all-electric business Lotus Technology is making electric vehicles for global markets, with a production capacity of 150,000 vehicles per year. The leadership team were acutely aware that routine quality inspections for this number of customised vehicles could all too easily create bottlenecks. Lotus Group opted for a machine vision solution which can analyse video data looking for potential defects with 99% accuracy, which keeps the production line moving fast without compromising on quality.
AI innovators such as ByteLake offer car manufacturers solutions which can inspect products and processes. Cameras armed with ByteLake AI can ‘watch’ production lines looking for defects, and even find ways to improve processes. These AI algorithms can also capture a range of parameters from the engine note to listen for defects and problems. This is a task which is difficult for workers in a noisy environment like a factory, where the quality of inspection can degrade if people are distracted. With ByteLake’s inspections running securely on edge computing hardware, results are delivered rapidly to workers on the factory floor.
AI cameras and computer vision can also revolutionise safety procedures by spotting possible dangers before they happen. Graymatics’ LabVista solution uses AI to spot hazards from workers failing to wear Protection Equipment (PPE) to loose objects on the factory floor or unauthorised people entering restricted areas of the facility. Computer vision also has an important role to play in logistics, tracking pallets and parts entering and leaving a factory to better manage and control inventory movement, as well as monitoring production lines so that raw materials are used efficiently.
In car factories, maintenance processes can require production to stop entirely, so it’s extremely helpful for business leaders to be able to plan ahead, rather than having to stop production at an unforeseen time. AI systems can predict when maintenance will be needed, offering business leaders a way to reduce the costs of halting production, and operating more efficiently.
From the factory floor to the dealership
Maintenance and servicing are a major concern for dealers, with 54% saying they face challenges with providing service and parts updates to customers, according to research from CDK.
General Motors is using AI to get ahead of this issue and has installed rapid defect identification scanners from UVeye in select dealerships already. Customers drive their cars through the scanner which uses computer vision to identify any issues on the vehicle which the service department can then fix. The system is over 90% accurate and can spot issues early on which get missed by even the most highly trained mechanics. The good news for dealers is that the new tool removes the need for time-intensive manual checks, reducing the amount of time waiting in the dealership for customers, and that time is being put to better use fixing the issues identified by the scanners.
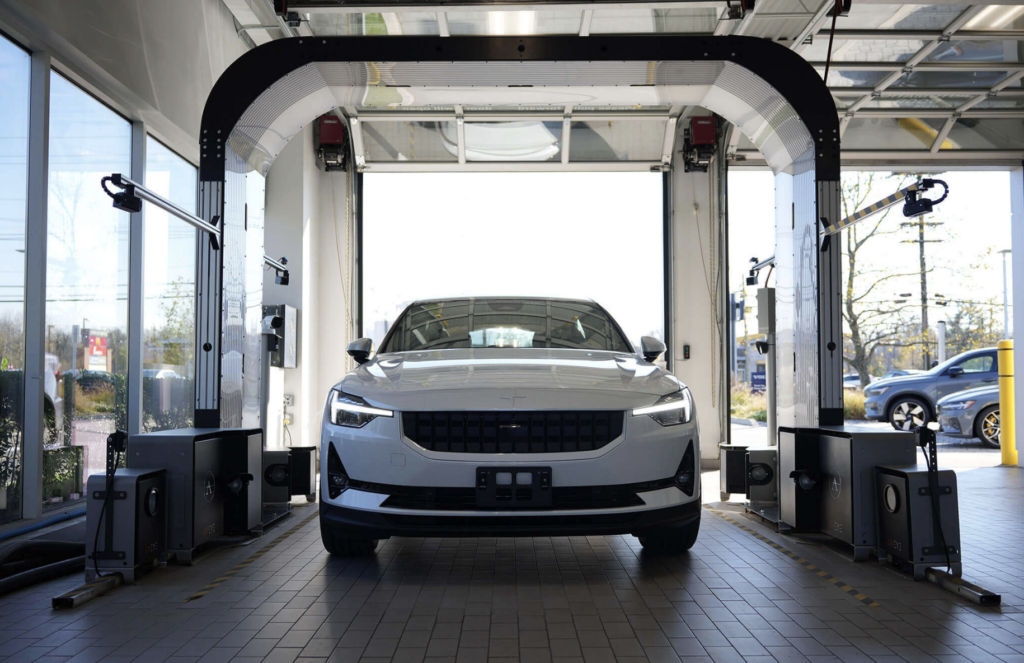
Getting the most out of AI
For IT leaders in the automotive sector, it’s important they have the right conversations with their teams before deploying AI, to work out which solutions will have the biggest impact on goals such as cutting costs or improving efficiency.
It’s also crucial that business leaders choose carefully and stay alert to everything they will need to make an AI solution work for their business. Some AI solutions may require development to work with a specific process, and every AI solution will require hardware infrastructure. It’s worth being aware that not every AI solution provider is a ‘one stop shop’ which can provide AI solutions for every area of operations.
The automotive industry’s rise has always been driven by the smart application of technology, and AI is the technological leap that will power the car and motorbike industries in coming years. From new efficiencies on the factory floor to insights uncovered from data from speeding racers, AI will be crucial to cutting costs and ensuring the production lines of tomorrow run faster, more cost-effectively and more safely than ever before.
About the author: Felix Marquez is AI Marketing Program Analyst at Lenovo