Batteries are arguably the most vital component of the entire electric vehicle (EV) powertrain, and the automotive industry continues to debate what chemistries and compositions will be a true game changer. However, nearly every stakeholder agrees on one key principle: existing battery technology could always be better.
Suppliers in the battery ecosystem are making fast progress. Summer 2024 saw a streak of breakthroughs and new funding to improve lithium-ion batteries (LIBs) or diversify the market through alternative chemistry research. Automotive World spoke to range of innovators to discover some of the latest trends taking EV battery design forward.
Durability through electrolytes
Although many automakers and governments around the world are on a mission to grow EV uptake, current LIB technology has a restriction that limits its scope: temperature. Most cells have an optimum range of between ten and 45 degrees Celsius, and anything below or above can lead to undesirable effects. This is problematic for growing EV markets in countries with demanding climates and weather conditions.
“Low temperature environments can have a severe effect on power output and battery capacity,” explains Yuto Iizuka, Manager of Corporate Research and Development at chemical company Asahi Kasei. “As the battery temperature drops, the resistance of the lithium ions increases, resulting in lower output and diminished capacity.” On the other end of the spectrum, high-temperature environments lead to accelerated degradation and ultimately shorter service life. “This is caused by a battery deterioration due to repeated charging and discharging, resulting in a gradual decrease in battery capacity,” he explains.
In June 2024, Asahi Kasei achieved a technological breakthrough to address both scenarios. By using acetonitrile as a solvent, the company created a low viscosity and high permittivity electrolyte that enables lithium ions to move and dissociate easily. As a result, the company claims its electrolyte has around twice the ion conductivity of conventional electrolytes. In addition, by establishing a strong passive film (solid-electrolyte interphase) on the surface of the battery’s anode, Asahi Kasei solved the issue of deteriorating durability under high temperatures. “This technology suppresses the decomposition of acetonitrile, overturning the common belief that it can’t be used as a solvent for electrolyte solutions,” says Iizuka.
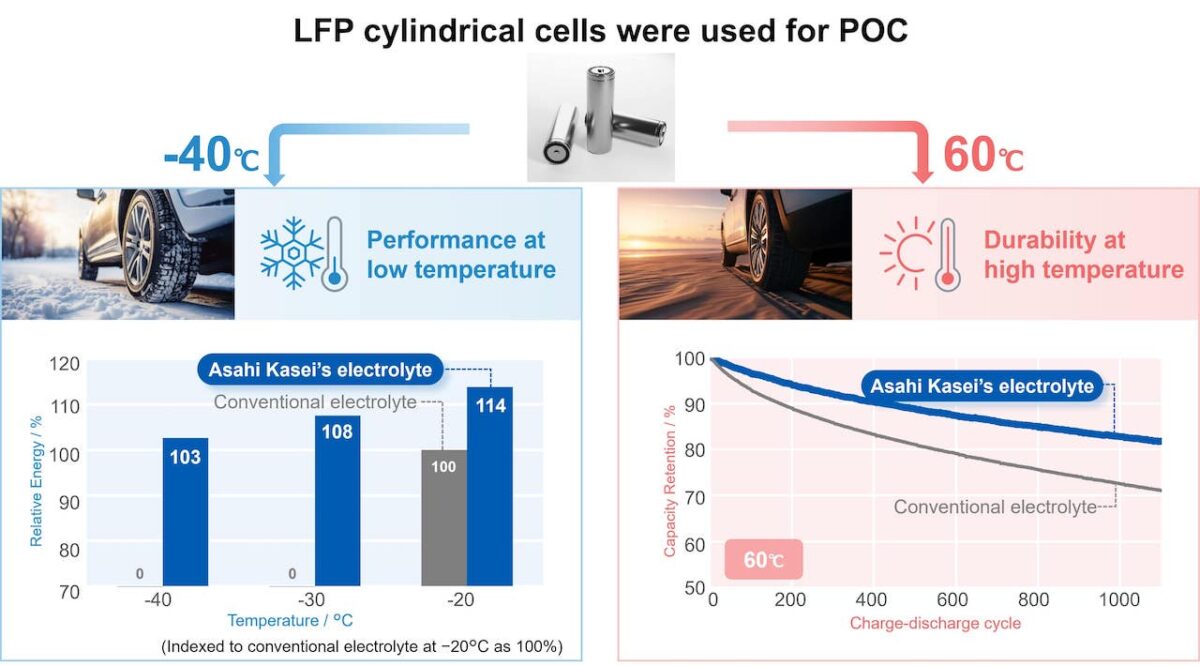
Commercialisation of the new electrolyte is expected in 2025, although Asahi Kasei will initially target energy storage and power tool applications. After establishing a track record in these segments, Iizuka states that it will next target applications in cars and scooters: “We are already having good discussions with several car manufacturers.” The company will license the technology to cell manufacturers, which can then sub-license to electrolyte producers. The impact of this innovation on EV uptake could be significant: “We’re convinced that by expanding the temperature range in which batteries can operate efficiently, this electrolyte will contribute to the spread of EVs in regions with demanding climate conditions.”
New anode materials
In a LIB discharge cycle, the anode is a vital component, releasing lithium ions to the cathode and creating a flow of electrons. Anode materials can add up to 15% of a LIB’s overall cost, and graphite, which combines affordability with high electrical conductivity and durability, has become the automotive standard material. Nonetheless, the industry’s constant pursuit of better EV performance means automakers are exploring other anode possibilities.
One of the most widely touted alternatives, silicon, could unlock 50% greater energy density than graphite. However, silicon’s fragility currently makes it unsuitable for the rigours of mobility applications. In June 2024, a three-way project between Toshiba, Sojitz Corporation, and Brazilian metals and technology company CBMM added another potential alternative: niobium titanium oxide (NTO). Toshihiko Takaoka, Vice President of the Battery Division at Toshiba, tells Automotive World that NTO anodes have twice the volume density of graphite. In practice, this means a LIB can fast charge to 80% in ten minutes, while the robustness of NTO means it can maintain more than 80% capacity even after 10,000 cycles.
“The characteristics of NTO batteries make them suitable for intensive commercial applications, like buses and trucks,” adds Takaoka. The project’s prototype cell, SCiB Nb, is being developed with Volkswagen Truck & Bus Brazil for this purpose, although he doesn’t rule out light vehicle applications in the future. A commercially viable NTO anode is currently scheduled for Q1 2025.
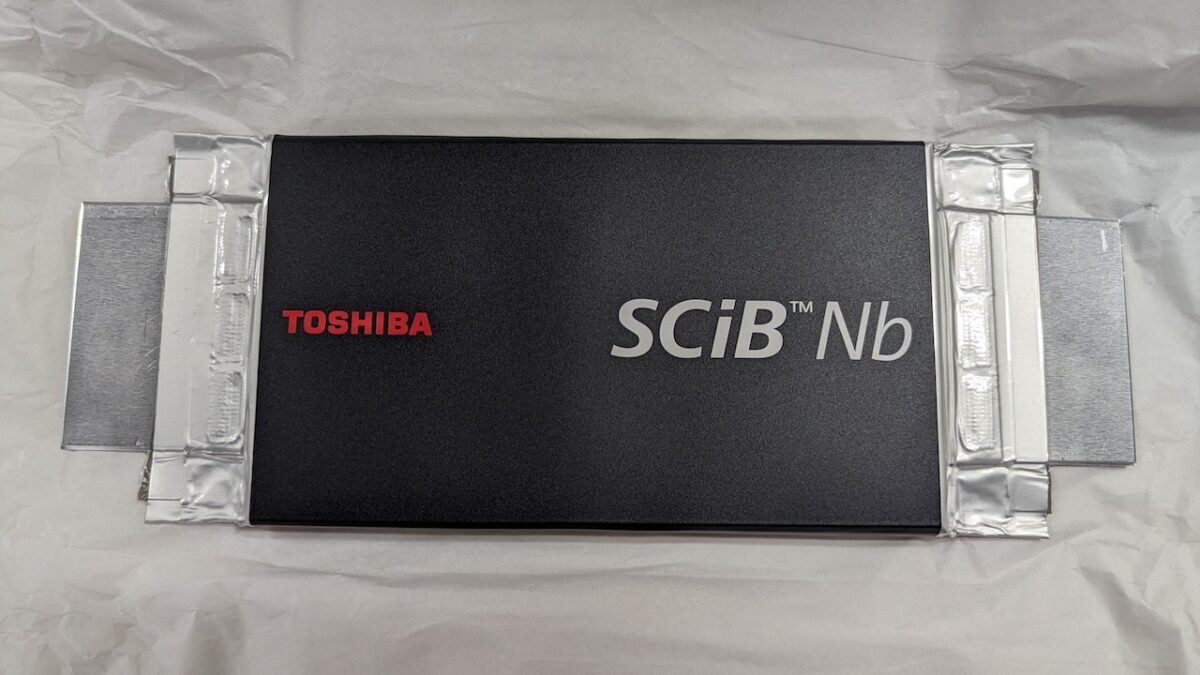
For its part, CBMM has created a new initiative called Battery Program to further research niobium’s use in e-mobility. Rogério Ribas, Technical Head of the Battery Program, states it has more than 40 such projects underway with research institutes, universities, and companies worldwide. Before the end of 2024, CBMM expects to open a Brazilian Real 265m (US$47m) industrial plant for niobium and “other oxides” in Araxá. With fast charging cited by some as the key to mass market EV adoption, Ribas anticipates “strong growth” for niobium oxide production, driven primarily by its use in LIB anodes. He projects 2025 sales of 800 tons, a 400% increase on 2024, with the potential to reach 20,000 tons by 2030.
Diversifying the battery mix
Although LIBs’ performance characteristics have made them the most widely adopted type of EV battery to date, there are still issues around safety, recycling, and the difficulty and expense of material sourcing. Sodium-ion batteries (SIBs) offer an easier-to-produce alternative—sodium is 90% cheaper than lithium and 1,300-times more plentiful. The first SIB plants have already started to emerge, but there are still design challenges to overcome.
Among the Chinese EV makers currently utilising SIBs—such as Jiangling Motors Group and JAC Group—the average range is 156 miles. “Sodium-ion’s energy density is about half of lithium-ion, which isn’t ideal for markets like the US,” states Darren Tan, Chief Executive of Unigrid, a California-based start-up currently developing SIBs. Instead of graphite, SIBs use a carbon anode, which has a lower density and takes up 60% of the total space. “Automakers actually run out of space integrating them in a vehicle.” Combined with a low voltage profile, SIBs currently struggle to deliver the power necessary for running EV systems.
In June 2024, Unigrid raised US$12m to develop SIBs initially for the data centre sector. Despite SIBs’ performance limitations, Tan remains optimistic about the technology’s future in e-mobility. “If the industry wants EVs to reach the masses, we need more affordable batteries.” Unigrid’s solution is a cylindrical cell with a new composition: a sodium-chromium-oxide cathode combined with a tin anode—tin is five-times denser than carbon and has triple the capacity. “Our solution shrinks overall anode size by 1,500%; you can put so much more energy into the cell,” explains Tan. “We could potentially double SIBs’ current range.” If so, this would make the batteries equal to the LIB average range of 300 miles.
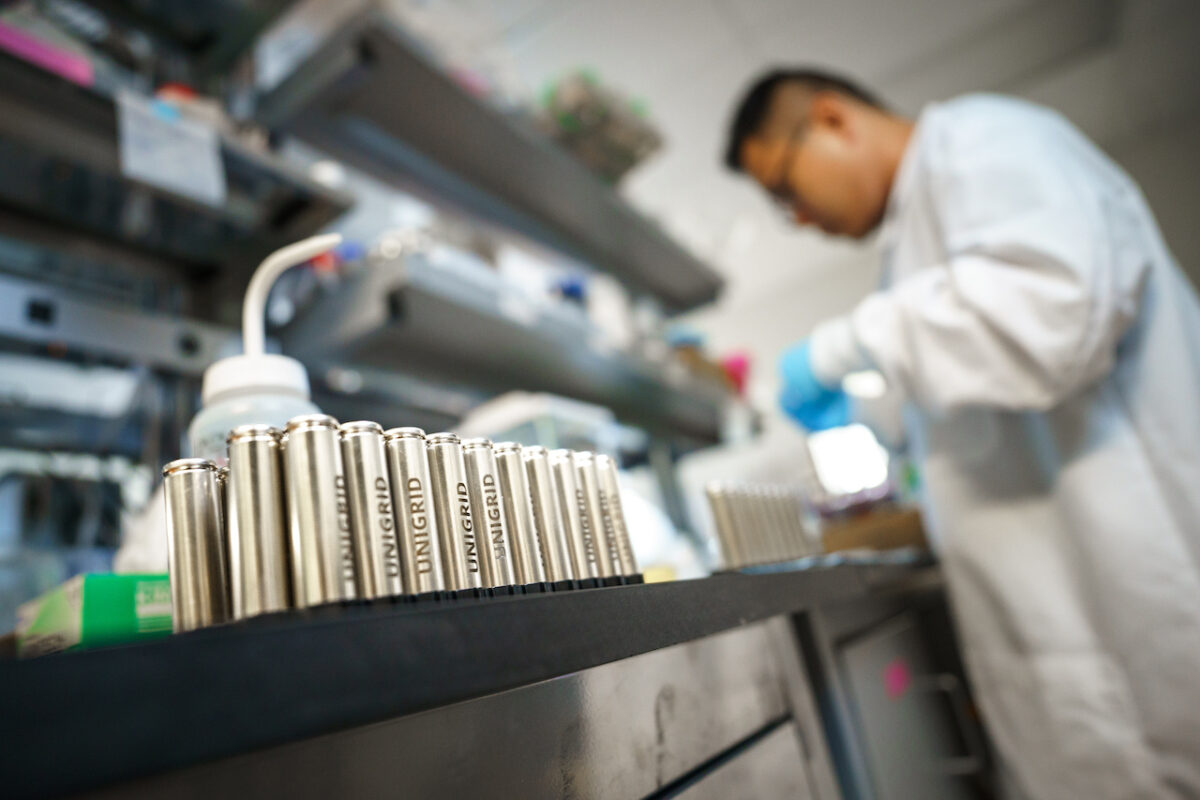
Since Unigrid is a cell, module and pack manufacturer, Tan states that its SIB technology can be easily transferred between industry applications. For automotive, he anticipates uptake in the two- and three-wheeler segments, particularly in Asia, where reduced power requirements could make a strong initial case study for SIBs. “But it’s important to note that SIBs won’t replace LIBs; no battery has ever totally displaced another.” Automotive use cases requiring high performance—luxury EVs, heavy-duty vehicles, etc.—are still likely to use LIB chemistries like nickel-manganese-cobalt. “Every type of battery will have its own role to play in the EV transition. What matters is that the right cells are available for each country’s mobility mix and transport goals,” he concludes.