Recent industry analysis from Versinetic, Key Barriers to EV Charging Infrastructure Rollout, highlights the most significant shortcomings that will affect the adoption of electric vehicles (EVs). From component shortages and lack of skilled workers to lithium-ion challenges and standards, these all threaten the charging infrastructure required to meet 2030 EV targets.
In Europe, car travel accounts for around 12% of all carbon emissions, while 29% of total US greenhouse gas emissions were generated from transportation. In line with the Paris Agreement, emissions from cars and vans will need to drop by more than a third (37.5%) by 2030. Brussels and EU member states are pouring millions into incentivising car owners to switch to electric. Some countries, such as the UK, are going even further, proposing to ban sales of diesel and gasoline vehicles.
The UK government, like many others, expects most charging to take place at home. However, the country’s Climate Change Committee suggests that 1,170 charge points are necessary per 100km of road by 2030. At the current rate of growth, only one-quarter (76,849) of public charge points necessary to meet anticipated demand (325,000) will be installed by 2032.
To plug the gap, the government aims to build a globally recognised EV charging network, supported by £1.3bn (US$1.7bn) in funding, covering costs for the strategic road network, homeowners, local authorities, and building owners, alongside regulatory changes. However, government funding isn’t all that is necessary.
EV production ramped up in 2021, especially in Europe and North America. However, EV and charge post manufacturers have been affected by the worldwide shortage of computer chips. Initially the result of coronavirus pandemic-related supply chain challenges; today, the industry faces issues with stockpiling of available components. During the pandemic, buyers over-ordered to minimise supply disruption, but the move away from JIT purchasing could prolong the world’s sluggish transition to EVs if chips remain scarce in the coming months.
There are numerous other headwinds. For instance, within the automotive sector there is a shortage of personnel with the necessary skills to develop, produce and maintain EVs and charging infrastructure. This includes mechanics, technicians and software developers. At the same time, chargers present a unique challenge as they are not manned in the same way as gasoline and diesel stations. Drivers rely on error messages to alert maintenance teams of any issues, such as incorrectly placed cables, breakage and flooding of holder and failing connectors.
New skills frameworks are now necessary. For instance, the WMG University of Warwick, The Faraday Institution and the High Value Manufacturing Catapult in the UK are looking to re-skill and up-skill workforces to meet demand at the point of need.
From component shortages and lack of skilled workers to lithium-ion challenges and standards, these all threaten the charging infrastructure required to meet 2030 EV targets
The grid
A common concern about EVs is the effect of drivers returning home and charging in the early evening, when demand is already at its highest. At the moment, the UK’s National Grid can cope with charging electric cars during an eight-hour period overnight, as it has a capacity of 63 gigawatts; but going forward, this will not be enough.
Electricity from the grid is “stepped down” at substations for distribution to homes and businesses at acceptable voltage levels. Substations have power output limits, so if everyone installs a typical 7kW EV charger, there could be too much demand for high levels of electricity at peak times, causing electricity overload.
As EV adoption grows, electricity demand will peak between 6 and 8pm as most workers return home and charge. They probably won’t need to do this daily, but are likely to, due to range anxiety. An increase in easy-to-use charging points at service stations, supermarkets and workplaces would reduce concerns about the range capabilities of EVs.
Intelligent charging solutions, or smart chargers, which deploy a flexible approach and smart technology are the key to balancing future demand. The recommendation of the UK government’s EV Energy Taskforce states that all future car chargers should be ‘smart by design’.
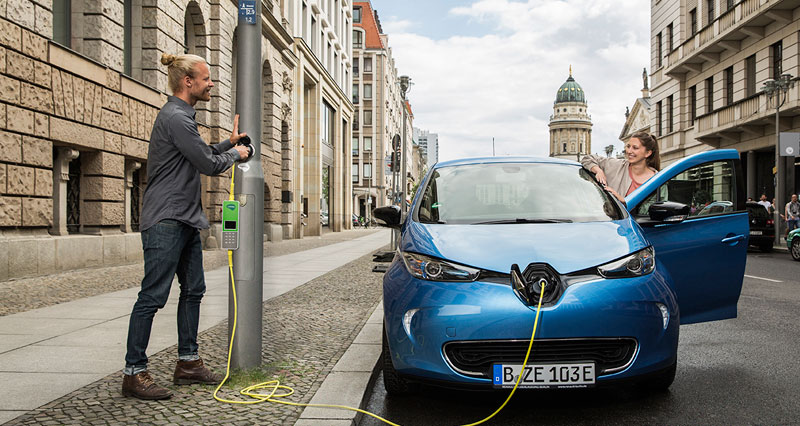
Materials
Demand for lithium has shot up; consequently, materials scientists face two big challenges. One is how to cut down on the metals in batteries that are scarce, expensive, or problematic because their mining carries harsh environmental and social costs. Another is to improve battery recycling, so that the valuable metals in spent car batteries can be efficiently reused.
At a conference in Washington in May 2019, Sarah Maryssael, Global Supply Manager of Battery Metals at Tesla, warned that after years of under-investment in mining, materials used to make the batteries could soon be in short supply and cause price rises.
Positively for the EU, lithium deposits have been discovered in Austria, Serbia and Finland, and the Portuguese government is preparing to offer licences for lithium mining to international companies in a bid to exploit its ‘white oil’ reserves. Sourcing lithium in Portugal offers Europe simpler logistics, lower prices, and fewer transport-related emissions. It also promises security of supply, ever-important in a world disrupted by supply chain volatility.
On-street chargers
The placement and frequency of on-street chargers presents a challenge. A busy street with new chargers could easily cause pavement clutter. EV owners without driveways may need to travel to neighbouring streets to charge or face ICE (internal combustion engine) cars blocking chargers. Additionally, councils will need to provide far more chargers, which will inevitably be an additional cost.
There are a number of innovative solutions to the problem, from wireless charging to using rising pillars, lances that plug into pavement-mounted plates, and street lamps to provide power. Neighbourhood EV charging hubs could take cars off the street too, reducing congestion and trip hazards from charging cables.
Standards
The development of EV charging standards is a vital requirement. Countries tend to follow their own set of standardisation rules and have regulatory bodies that oversee the technical specifications and approval of new technology. For instance, Japanese car manufacturers have developed their own connector and charge delivery mechanism called CHAdeMO; while the European-derived CCS is becoming the European standard on DC, with even Nissan moving over to it from CHAdeMO. It is the first system that can use Type 2 single-phase or three-phase chargers and, through the same connector, be used for DC rapid charging. In principle, CHAdeMO could also do this, but not through Type 2 for normal universal fast charging. In the US, a similar CCS is in use combined with a Type 1 connector.
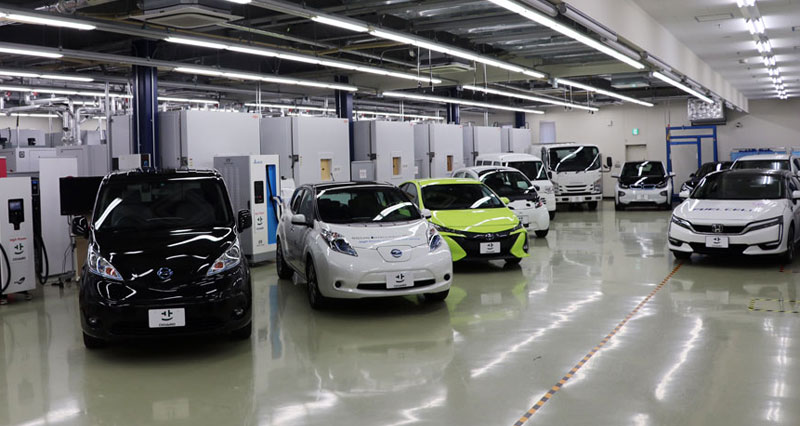
A unified standard would reduce capital investment and improve ease of access for all end users. Indeed, we have arrived at a comparable parallel point in history; the Betamax vs. VHS standardisation wars. Once one standard dominated and was accepted by the market (VHS), growth in personal video recorders and players grew exponentially.
As the industry moves further along the path to EVs dominating the roads, the pandemic has slowed down progress. Currently, shortages in components and skilled personnel are the tip of the iceberg. Grid challenges, while manageable today, need some consideration to ensure that, where possible, drivers can charge at home.
Predicted lithium shortages will drive innovation in battery recycling, while on-street charging plans are necessary for those unable to charge at home. Universal standards will also need to ensure interoperability. Against this background, even with funding and enthusiasm, innovation and collaboration remain the best routes to help us overcome these challenges.
About the author: Dunstan Power is Director at Versinetic