Electric vehicles (EVs) may be transforming the automotive landscape, but with them comes a unique set of challenges. Of these, one of the most pressing is battery thermal management. Managing the thermal performance of batteries is crucial to their longevity, safety, and overall performance. Lithium-ion batteries are quite sensitive to temperature and must generally be kept within 15-35 degrees Celsius.
Become too hot and the battery can degrade, lose efficiency, or even go into thermal runaway and cause a fire. Conversely, cold temperatures affect performance and range. Striking the right balance is a complex task that involves continuously monitoring and controlling the battery’s temperature in real time. A single error could reinforce consumer doubts around EVs, which are generally concentrated around the battery.
An effective thermal management system must meet this challenge head-on but also be compact and suit the vehicle architecture. Johannes Helmich, Chief Technical Officer at TI Fluid Systems (TIFS), believes the best approach comes in the form of modular solutions. Modular thermal management systems offer flexibility, scalability, and improved performance while also allowing components to be easily replaced or upgraded. “At the same time, it is important to have a supplier that can provide everything you need for that modularity,” he tells Automotive World. “And that can promise its solutions will also reduce vehicle weight and come in at a decent price point.”
Safety comes first
The first and most important area to tackle, explains Helmich, is efficacy: “With the switch from internal combustion engines (ICEs) to EVs, the urgency to get thermal management right is so much higher. You can’t leave square one without ensuring that it is effective.” This means making sure that temperatures are kept within the optimal range regardless of the vehicle’s state, be it on the road or charging.
However, there is no one perfect solution that will suit all manufacturers and vehicle types. Some OEMs may opt for dual-circuit cooling architectures that possess separate cooling circuits for the battery during charging and driving. Others may prefer smart temperature control algorithms that dynamically adjust the cooling system based on real-time data or use external power sources to condition the coolant during charging cycles to save power.
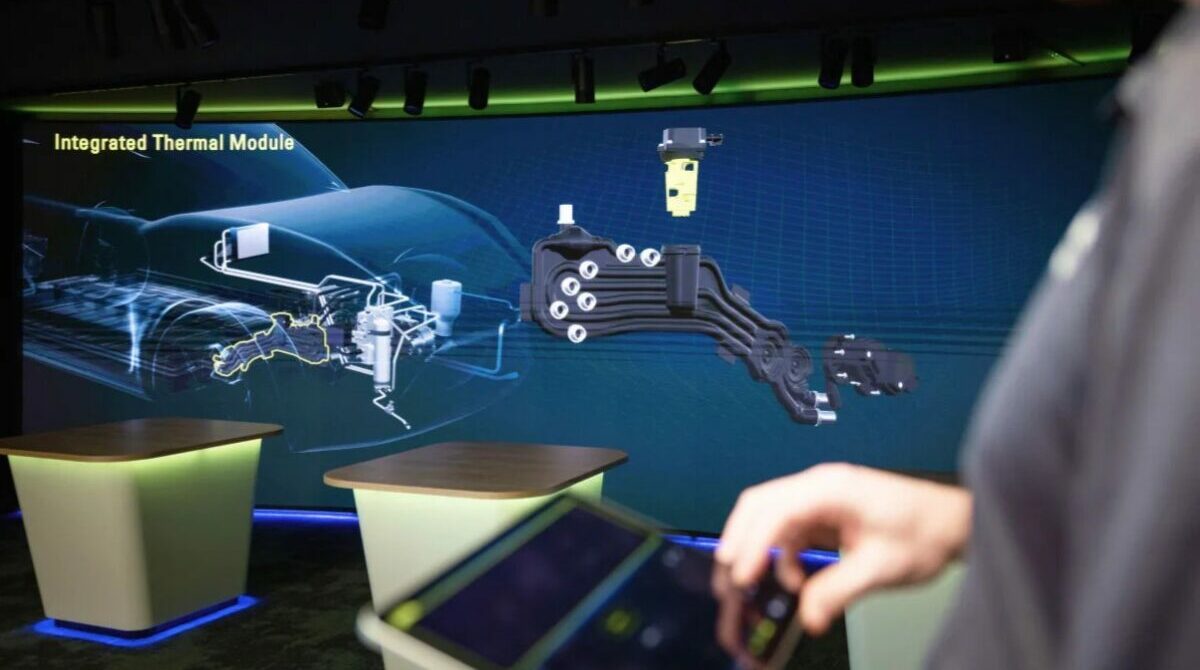
Helmich notes TIFS’ e-mobility innovation centres empower the company to develop modular products that match the specific needs of each automaker. “Instead of looking at our product and matching it to the need, we’re looking at specifically what is requested,” he explains. “We look at the physical architecture as-is and what efficient ways might exist using our toolkit to come up with a tailor-made solution.”
By offering a wide range of modular technologies, solutions and parts that are mutually compatible, TIFS believes it is possible to meet the thermal management challenges of virtually any EV battery system. “We’re a supplier that can provide the entire portfolio of thermal management parts,” states Helmich. The company is continuously broadening its ‘toolkit’ of applicable parts, from connectors, seals and valves to pumps, electronic control units, and entire modules.
Flexibility on the automaker’s preferred materials is a key aspect of TIFS’ approach to modularity. For example, in addition to silicone rubber cooling hoses—the tubes that direct the coolant where it needs to go—it also offers plastic rubber ones. Either solution can be preferable depending on the specifications around weight, range of movement, and cost. TIFS also works actively to develop new modular solutions in response to automaker feedback and meet the thermal challenges of future battery technologies like solid-state. “We are certainly looking ahead. Thermal management will always play a key role, no matter what technologies are used in the future.”
Automation and lightweighting
Regardless of the modular thermal management system, it must integrate with autonomous software that continuously monitors and adjusts battery temperature. All monitoring software collects data in real time from various sensors situated throughout the battery pack and generates a thermal map based on these inputs. More advanced iterations of the technology can also use predictive analytics to predict future trends around the battery’s behaviour and potential thermal runaway risks. This can be integrated with the battery management system directly to coordinate control of battery health and temperature. TIFS works to ensure its modular systems are fully compatible with its monitoring tools.
“You need to have active interaction between the environment and your desired thermal performance,” explains Helmich. “If you’re driving up a mountain, you will inevitably need to put more demand on the cooling. The vehicle should be able to quickly identify this and take appropriate action.” By ensuring that its software is compatible with the full range of potential thermal management configurations, TIFS believes it can remove a barrier to adoption around the modular approach.
At the same time, a modular system cannot compromise other design priorities. Instead, it should help enable them if possible. As an example, Helmich highlights lightweighting through the minimisation and substitution of unnecessary materials and parts. EVs typically weigh substantially more than their ICE equivalents—a Peugeot e-208 weighs 1,910 kg, almost double the 1,090 kg of its 1.2-litre gasoline-powered equivalent, the Peugeot 208. Much of the weight difference comes down to the battery, and offsetting this can boost vehicle range and lower wear and tear on components like the brakes and tyres.
You can bring the weight down by up to 60% using thermoplastic refrigerants
While tailor-made solutions can lower weight by providing only what is required to suit the customer’s vehicle architecture and thermal goals, further weight reductions are possible through material substitution. Helmich highlights that there are a number of solutions available that offer comparable thermal performance, including thermoplastic refrigerant lines and using aluminium instead of steel in certain components.
“You can bring the weight down by up to 60% using thermoplastic refrigerants,” Helmich notes. At the same time, he adds, it is crucial that these solutions remain competitive on price, otherwise automakers will look elsewhere. Meeting the criteria of thermal performance, cost-effectiveness, and lightweighting is core to TIFS’ modular approach. He further emphasises that these concerns remain secondary to effective cooling, but modular solutions make it easier to tackle several at once.
Ultimately, thermal management is as critical to electrification’s success as any other metric, like range or charging speed. They help ensure a battery’s long-term health and safety, and their success passively allows consumers to overcome their concerns. Adopting modular thermal management solutions could ultimately help automakers build that trust, while also meeting wider goals around vehicle weight and production costs.