Manufacturing a car is both highly complex and expensive. It requires thousands of parts, including between 60 and 100 high-quality sensors, with many built into the engine to ensure that the owner can identify and prevent possible issues before they result in breakdowns and expensive repairs. Sensors are being deployed throughout the vehicle to meet evolving security and efficiency standards as well as to address environmental standards.
Sensors become essential
Engine sensors measure voltage, fuel temperature, oxygen levels and much more, ensuring that the vehicle is operating at peak efficiency. Their use in today’s “connected car” is already highly extensive and is set to increase exponentially. In a report last year, consultants Deloitte outlined the belief that by 2030, half the cost of a car will be accounted for by its electronics, of which sensors with semiconductors will be a major part. Consequently, these sensors will need to be protected to prevent increased breakdown. Deloitte and Gartner predict the use of non-optical sensors such as environmental sensors, fingerprint, inertia and magnetic sensors will increase at a compound annual rate of more than 7%. By next year, the semiconductor content of a car will average US$600, Deloitte calculates (although not all related to sensors).
Some suggest that the ideal solution to the high cost of car repairs is protection at sensor level
The rise of advanced driver-assistance systems (ADAS) has already vastly expanded the range of applications for sensors. ADAS technologies are totally reliant on sensors to automate or assist with a multiplicity of driver functions such as parking, blind-spot monitoring, safe braking and collision-avoidance. ADAS implementation, according to Deloitte, is growing at a rate of 24% a year.
This growth in the application of sensors will increase hugely with the switch to electric vehicles, one of the most significant developments in the entire automotive sector. Governments in developed economies are now actively promoting the changeover. For example, the UK government has forbidden the sale of diesel or gasoline cars by 2030. EVs will require a multiplicity of sensors as part of a new approach to operation, maintenance and sustainability.
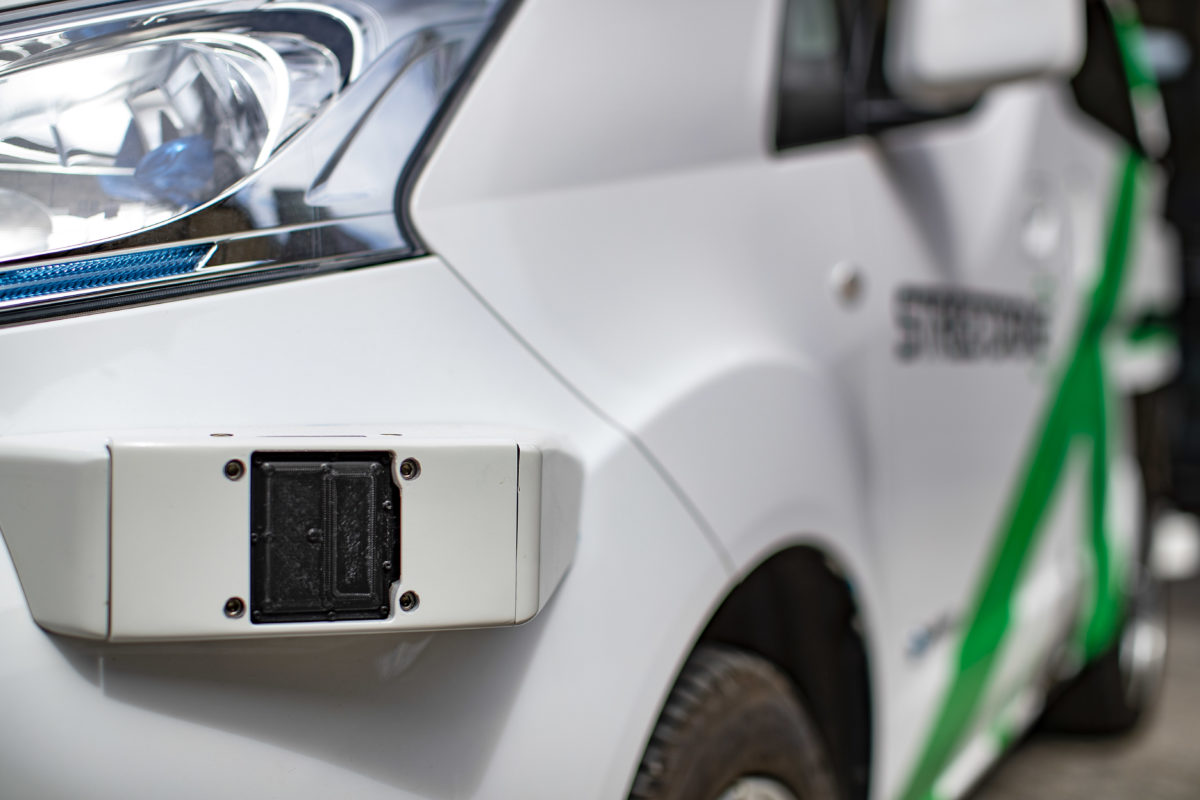
Looking further down the road, once autonomous vehicles have become part of the everyday reality, sensor technology will be as essential as the electricity in their batteries. Without camera, radar and LiDAR sensors, these vehicles are unable to function. Whatever the vehicle or its drivetrain, the problem remains that with many sensors necessarily exposed to the elements, something is bound to break, leak or need upgrading.
The increase in sensors is also being driven more recently by OEMs collecting data from their fleet on the road in order to report on malfunctions should they occur, as well as study the performance of their vehicles. The collected international data is then analysed by firms such as Tesla to understand how their products and systems are performing globally and to improve the design and manufacture of future cars.
When sensors fail
The failure of sensors brings multiple risks. The first is that it will result in damage to the car that will lead to the need for expensive repairs. Recent industry estimates indicate that some car parts can cost well over £1,000 (US$1,400) to repair or replace. The second is that it will render the car unusable even if there is nothing mechanically wrong with the rest of the vehicle. Either eventuality is likely to cause brand damage. Failing sensors can also inflict significant environmental damage by causing an increase in emissions, alongside performance and drivability problems. There is also the risk of reporting back ‘bad’, unclear or no data to OEMs that collect data of their fleet on the road; this could have an adverse impact on influencing the design and functionality of future products.
With many sensors necessarily exposed to the elements, something is bound to break, leak or need upgrading
The level of impact sensor-failure has on brand image becomes even clearer when the likely impact on the motorist is considered. When an individual is alerted to a fault with their car by a sensor, they have two options: get it looked at or not. If the fault allows them to continue to drive and it is not convenient for them to go get the car checked out, they will continue to drive the car, not knowing what damage they are doing. Faulty sensors also raise stress levels. Consumers will either think repairs are going to be very expensive or worry about being stranded if their car breaks down on the road. While the growth of ADAS is steady in vehicles, its associated functional features are becoming the new normal in the automotive market. Consumers’ reliance and their expectations on these features to be fully functional have been growing. The latter makes it vital for sensors to be durable in order to avoid adverse consequences should they get damaged and more importantly to preserve consumer confidence.
As vehicles become more dependent on sensors through the expansion of ADAS and replacement of combustion with electric motors, manufacturers may seek to reassure consumers by offering extended warranty periods in a bid to extend their market share. This may give confidence to some potential buyers, but no warranty or guarantee will be as effective in the market as technology that prolongs the life of devices and systems within each vehicle.
Protection at sensor level
Some suggest that the ideal solution to the high cost of car repairs is protection at sensor level, including liquid proof coatings as opposed to mechanical sealing or conformal coatings, which can degrade when exposed to heat or vibrations. Lasting protection can be provided using the latest nanocoating technology that chemically bonds the coating onto the printed circuit board assembly (PCBA) to give outstanding thermal durability. This solution trumps mechanical seals, which add extra weight and require more space as well as lower the vehicle’s energy efficiency and prevent automotive innovation.
Advanced but practical solutions like liquid proof coatings can enable manufacturers to make sensors repairable so they no longer require replacement. This will increase vehicle reliability—a vital factor in the considerations of car buyers. It will also ensure vehicles are sustainable and environmentally friendly. It will make manufacturers better understand the performance of their fleet on the road and improve future vehicle design at a time when the entire automotive market is under heavy scrutiny.
About the author: Simon Vogt is Chief Commercial Officer at nanotechnology development company P2i