With charging times and range still key consumer concerns for adopting electric vehicles (EVs), the race is on to deliver the next generation of battery technologies. Technologies like all solid-state batteries draw splashy headlines but have yet to be seen in market applications. There’s a more pragmatic and commercially significant solution hitting the market now—second-generation silicon anodes.
Major cell manufacturers and automotive OEMs are increasingly investing in second-generation (Gen 2) silicon anode materials and production. These advanced silicon anodes overcome historical challenges seen with first-generation materials, enabling radically higher energy densities in battery cells—up to 50% more energy density than lithium-ion cells with graphite anodes—while utilising existing production lines.
Why Gen 2 silicon anodes are the future
Gen 2 silicon anodes have secured a significant place in lithium-ion cell manufacturer development roadmaps due to their ability to optimise both performance and cost with incumbent cathode materials. This balance of innovation and practicality is crucial for mass market adoption. The technology represents a major leap forward from its predecessors, primarily in its approach to managing silicon’s expansion during charge and discharge cycles. Gen 2 technology harnesses the power of silicon inside a more defined structure, effectively solving the expansion problem that plagues earlier generations. This is critical, as silicon can expand up to three times its original volume during charging cycles.
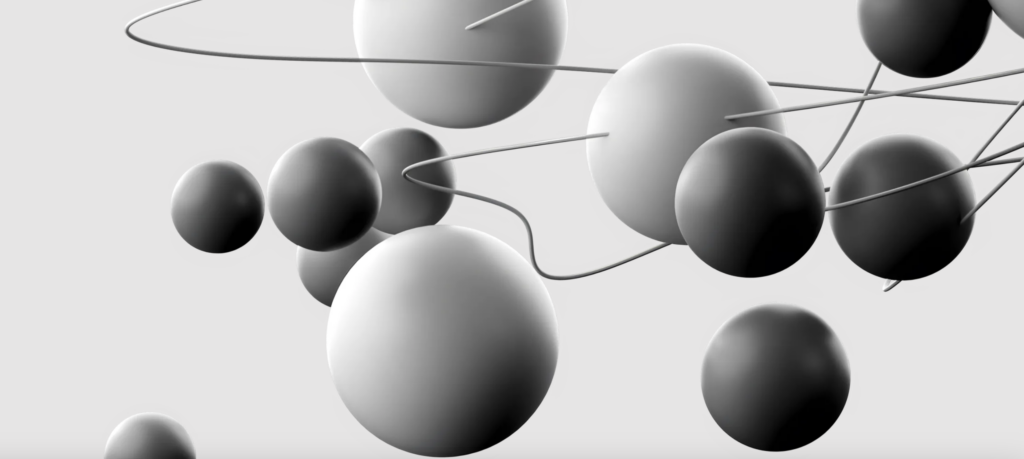
The benefits of this advancement are groundbreaking. Silicon anodes offer substantially higher energy capacity than traditional graphite anodes, allowing for better electrode layer design, improved cell charging, and lower internal resistance. The result is EVs with longer range and faster charging times—potentially as fast as 11 minutes to go from 20% to 80% state of charge. One of the most compelling aspects of Gen 2 silicon anodes is their compatibility with current lithium-ion cell manufacturing processes. This significantly reduces the barriers to adoption, allowing battery makers to enhance performance without overhauling entire production lines.
Beyond performance and manufacturing advantages, Gen 2 silicon anodes can help alleviate supply chain constraints by requiring less material. This is particularly important given that the synthetic graphite market is currently dominated by China. However, some companies, including Nexeon, are developing silicon anode materials using materials sourced from Korea and the US, offering a competitive advantage in both cost and supply chain diversity.
Silicon anodes offer substantially higher energy capacity than traditional graphite anodes, allowing for better electrode layer design, improved cell charging, and lower internal resistance
Additionally, the production of silicon anodes can offer a lower carbon footprint compared to traditional graphite anodes. While graphite production often starts with crude oil and requires high temperatures and energy inputs, silicon anode materials can be derived from more sustainable and regulated sources. This aligns with the core goals of the EV industry, to reduce environmental impact across the entire supply chain.
The path to mass adoption
While the technical barriers for implementing Gen 2 silicon anodes have largely been overcome, the industry still faces challenges in economic and risk assessment. However, these hurdles are typical of the normal three – to five-year adoption cycle for new battery technologies.
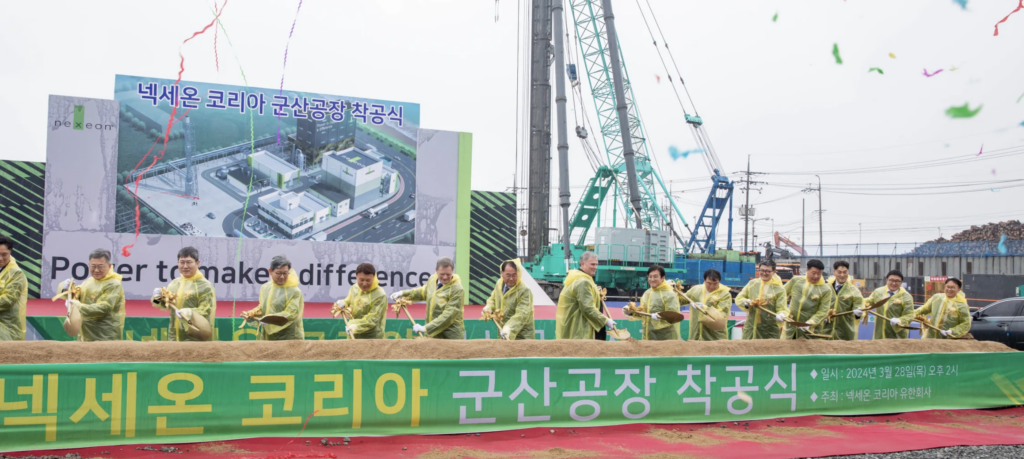
Early adopters, including major players like Panasonic, are already pioneering the integration of Gen 2 silicon anodes. As more manufacturers recognise the benefits, uptake across the industry could expand rapidly. Nexeon is preparing for such a market boom and recently broke ground on its first commercial production facility in Gunsan, South Korea, which is capable of producing well over 1,500 tons per year over time.
The promise of silicon
For automakers, the most compelling reason to adopt silicon anode technology is the potential for dramatically faster charging times in combination with extended range. This directly addresses the primary concerns of EV consumers, and the improved power capacity of silicon anodes translates to better acceleration and overall vehicle performance.
While all-solid-state batteries and other experimental technologies may promise revolutionary changes for the future, Gen 2 silicon anodes represent a pragmatic, commercially viable path to significantly improved battery performance today. Beyond this near-term value creation, Silicon technology will set the basis for improved next generation technologies as well.
Michael Lennartz is Chief Technology Officer of Nexeon