The use of simulation tools in an engineering and design context is nothing new. Valued at around US$13bn in 2023, the global simulation software market could be worth more than US$34bn by 2032, according to Fortune Business Insights. For teams designing the next generation of electric vehicle (EVs), the ability to replicate real-world physics like structural mechanics, thermodynamics, and electromagnetics is invaluable.
Cloud-native engineering simulation software provider SimScale estimates that one in 25 engineers might already have access to such tools. Chief Executive David Heiny acknowledges that there are many offerings on the market, yet progress is still necessary: “Making simulations faster, better, and more accurate is an endless task.” However, focusing on performance alone is not necessarily the most disruptive angle to help EV engineers.
“We believe in changing how simulation is used in the overall product development process,” he explains to Automotive World. “The complex and compute-intensive nature of modern simulation methods typically silo its use in small, specialised teams.” Needing to interface with these separate teams on design verification can extend overall project lead times and constrain EV innovation. As such, SimScale aims to make simulation tools a fully automated and accessible part of every engineer’s IT stack.
The need for speed
Today, an automaker’s simulation tools are often a heterogenous stack of off-the-shelf components arranged in a desktop application. The result can be both expensive and convoluted to use, with each validation step carried out manually. As an alternative, SimScale claims to have produced the first vertically integrated cloud-native software-as-a-service simulation application that can be deployed broadly, early and aggressively, while experts still maintain central governance.
“Teams get access to user, data and process management, as well as high performance computing and our AI model,” says Heiny. “We take over that complexity so engineers can focus on their actual engineering work.” SimScale’s decentralised simulation tools enable EV development teams to act faster by providing easier access to simulation insights. To push the pace of development even further, its platform uses machine learning models to provide almost instantaneous predictions for new design variants based on historical data. This enables it to predict the performance of simulated critical systems and components, including batteries, e-motors and inverters.
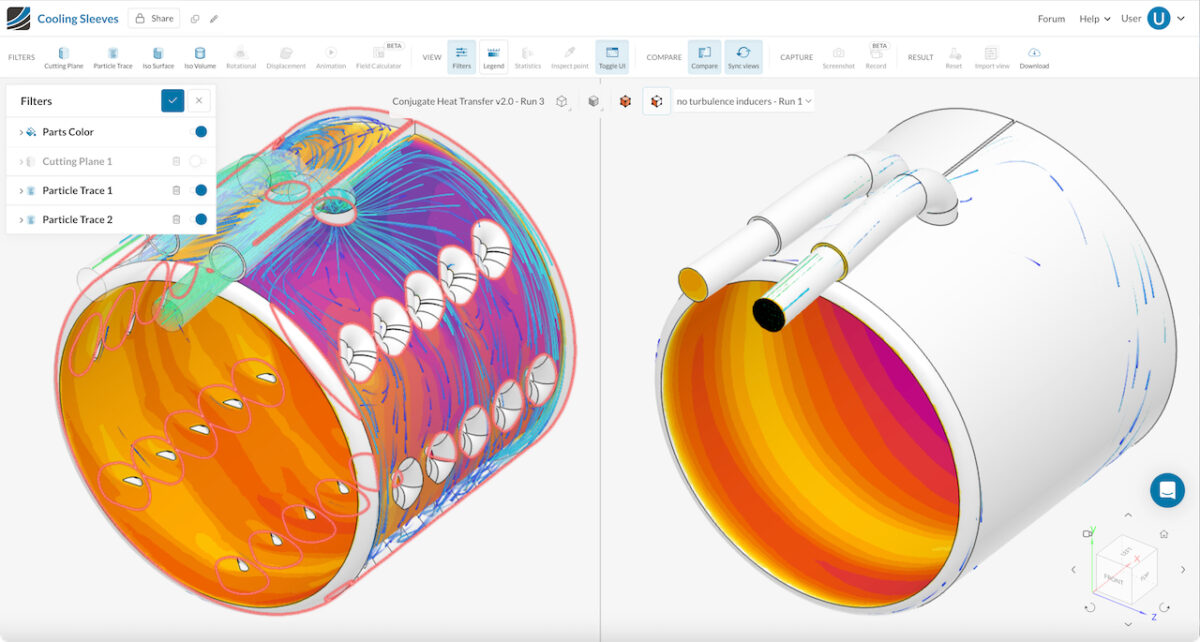
Heiny notes that SimScale was not exclusively conceived for automotive, though its benefits and utility for the industry became clear during the shift to electrification. As engineers help automakers make their often complex transition from internal combustion engines to EVs, time is not on their side. “The powertrain architecture is changing on a global scale, but OEMs and suppliers need to support legacy product lines in addition to designing new ones,” he says. “All the people we spoke to said they had a need for speed.”
Overcoming bottlenecks
Between 2020 and 2023, global EV sales accelerated from around 3.2 million units to 13.4 million (+319%). Although this growth rate flattened in 2024, some analysts expect it to start picking up again from 2025, as several entry-level models enter the market. Heiny states that the pace of vehicle R&D has become intense for suppliers and automakers alike: “Delivering a request for proposal (RFP) response used to take around three months, but EV programmes are so much faster—that same RFP deadline could now be three weeks.”
SimScale’s tools offer engineers a way to move faster without sacrificing quality. Heiny explains that simulation lead times—the interval between selecting and validating a design decision—can be reduced from days or weeks using standard practices to seconds through AI. “That’s significant because these lead times are the bottlenecks to product iteration, quality, and delivery. The faster a vendor can iterate, the greater their RFP’s chance of winning an automaker’s business.” Through its cloud-based API, SimScale facilitates the real-time collaboration necessary for a team to work collectively and validate its own design decisions while still giving simulation experts full oversight for quality control purposes.
It is equally valuable for automakers’ in-house R&D. In one prominent use case, Rimac Automobili’s engineers needed to evaluate new thermal management solutions to produce optimal EV battery performance across a unit’s operational lifespan while also ensuring user safety. The complete validation process inevitably required testing multiple variables (such as liquid- and air-cooled systems) and key parameters (maximum cell temperature, thermal gradient).
Satisfactory results through physical tests conducted serially could have taken up to 300 hours. SimScale notes that physical product geometry can both limit observation and restrict the variable range of parameters under investigation, which are not issues in virtual testing. However, the SimScale platform’s AI and high-performance computing capabilities enabled it to perform 30 simulations in parallel. The company states that it was ultimately able to complete testing in just 13.5 hours, representing a 96% time saving for Rimac.
Leader or laggard?
Former Stellantis Chief Executive Carlos Tavares once characterised the emerging EV era as “Darwinian”, where only the most dedicated and capable brands would survive. In 2025, even the segment’s pioneers are struggling to offer differentiated or advanced products, and existing EV technology is still far from attracting the mass market appeal necessary for sustaining growth. In this highly competitive environment, Heiny positions simulation tools as invaluable for resolving some of the most prominent EV engineering challenges.
Innovation will [determine success], and decentralised simulation tools can help [OEMs] achieve it at a faster pace
“There are a handful of pure EV players out there, but the vast majority find themselves in the middle. If they want to survive the EV powertrain shift, suppliers and OEMs will need to perform a ton of innovation in a highly compressed amount of time.” He envisions a future in which 99% of all product validation is performed digitally, with only the very last step requiring a physical test. It is by shortening lead times that automakers will ultimately be able to produce EVs in the timescales demanded by regulations and the market.
The stakes are high, and the approach an engineering team takes can mean the difference between success or irrelevance. “Change isn’t optional anymore; the global powertrain shift is going to happen, no matter what,” Heiny concludes. “Engineering teams need to decide if they want to be leaders or laggards; innovation will be the determining factor, and decentralised simulation tools can help them achieve it at a faster pace.”