The complexity of new vehicles has soared over the past couple of decades, and while this has enabled advances in efficiency and performance, the task of testing and validation has only become more challenging.
As a result, engineering firms are devising virtual simulation tools that can perform processes which would otherwise be carried out on the tarmac, at high cost, and at low speed.
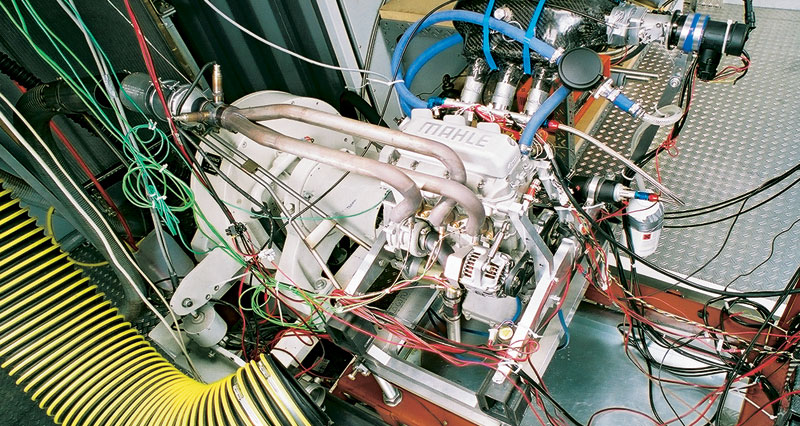
Powertrain development in particular can benefit from simulation techniques, removing the need for costly prototypes and ramping up productivity. While road tests remain vital, many procedures can be repeated using accurate software, thus slashing time to market. Part of this approach is being driven through a concept known as frontloading.
In essence, more work is carried out via simulation at the beginning, with fewer processes that use real-world prototypes overall—thus simulation is ‘frontloaded’. It is a U-turn from past approaches, where practically all development would be carried out through hardware testing. “It was very expensive” for automakers, said Christian Mayr, Project Manager, Integrated and Open Development Platform at independent engineering firm AVL during a recent Automotive World webinar. “All OEMs today have to reduce the cost, number of prototypes and time taken during development.”
‘Label’ is a term used to describe individual data values, and powertrain calibration processes have gradually become more time consuming as more labels are introduced. In 1995, an engine control unit (ECU) had around 500 labels, for example. One calibration engineer would work on a single engine and without any simulated processes.
In 2005, most ECUs had around 5,000 labels, at least two calibration engineers per engine, and a high number of engines variants to work on. At this point, virtual testing had still not been introduced in any meaningful way. By 2015, ECUs had soared to around 50,000 labels, with more than 30 engineers involved in each project. Simulation had finally been introduced in order to handle this growth in complexity, and the idea is to continue increasing the proportion of virtual testing.
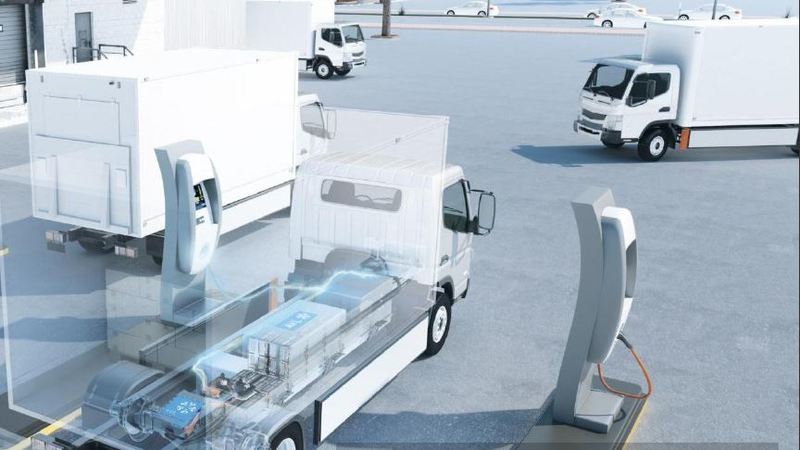
AVL has developed the Integrated and Open Development Platform (IODP), which allows developers to leverage simulation across all powertrain test cases. Mayr explained that while simulation plays a vital role in cutting costs associated with physical tests, they are ultimately unavoidable. This is why varying levels of simulation are introduced via the frontloading method.
An early stage process such as individual component testing can be carried out with a high degree of simulation, for example. A mid-way process, such as engine testing, can use an even mix of physical and virtual testing, whereas chassis dyno testing will involve more physical testing. In short, the closer the vehicle is to being tested on the road, the less virtualisation is used. The potential savings are staggering: a full vehicle prototype costs in the region of €250,000 (US$279,400) per physical test case, according to Mayer, while the same tests could be simulated at a cost of just €100 each. “Through frontloading, you can begin optimising through simulation right from the start of the pre-concept phase,” he added.
Simulation is used across the automotive industry to develop, calibrate and validate individual components, systems and finished vehicles. For example, virtualisation is used to gauge the viability of powertrain electrification in the commercial vehicle space; how electric vehicle (EV) batteries can be developed to prevent the risk of fires; and even to hone the capabilities of autonomous vehicles.