Steel has been at the heart of vehicle manufacturing from the earliest days of the industry and, thanks to its strength, affordability and recyclability, looks set to remain so. While steel is also popular in the construction and infrastructure sectors, the automotive industry accounts for about 12% of the world’s total steel use.
Automakers have been under pressure to clean up emissions from both their vehicles and their manufacturing operations in light of growing environmental concerns. That includes sourcing from sustainable, low-carbon suppliers. According to estimates by the International Organization of Motor Vehicle Manufacturers (OICA), the 95.6 million vehicles produced in 2018 used an average of 900kg of steel per vehicle. Today, the process of making steel accounts for 7% of the world’s carbon emissions. “Because there is so much steel used—90% of all metal used in the world is steel—the steel industry has a big carbon footprint and, like all industries we need to reduce it,” states Alan Knight, Global Head of Sustainable Development and Corporate Responsibility at steel giant ArcelorMittal.
The challenge is on
The good news is that steel is infinitely recyclable, avoiding the end-of-life questions posed by some alternative materials such as carbon fibre. “All the steel used in all the millions of Model T Fords is probably still being used today,” says Knight. However, the industry simply doesn’t have enough scrap to replace all primary steel. ArcelorMittal forecasts that annual steel consumption will reach 2.6 billion tonnes by 2050, so clearly new material will be required. Making that steel with as small an environmental impact as possible is the aim.

ArcelorMittal is exploring several avenues. “Technological advances allow us to make steel with a much lower carbon footprint. Rather than just backing one technology at the moment, we are testing the different choices available,” Knight tells Automotive World. Carbon capture and storage (CCS) is one option, in which the company simply captures the CO2 and stores it underground. Some estimates suggest that up to 90% of carbon emissions from the industrial use of fossil fuels could be captured by CCS. While there have been studies concluding that CO2 can be stored safely underground for thousands of years, it remains a divisive approach with persistent concerns about the long-term safety. “We know why people are concerned about that but we’ll test how viable it is for us,” adds Knight.
Instead of storing the captured carbon, another approach is to convert it into ethanol, which can be used in many different processes, such as in making plastics and jet fuel. “Cars will always contain some plastic. Who knows, in 20 years’ time we might be making some of that plastic,” he suggests. “We are not committing to that, but it represents one of the solutions we have.”
Another angle is to replace coal with circular carbon, and ArcelorMittal’s circular carbon of choice is waste wood. “To get the wood, you grow a tree, which is sucking the CO2 out of the air. You then use that instead of coal, which is just a one-way process,” explains Knight. The company is setting up a €40m (US$44.4m) plant in Ghent to test the use of waste wood. Hydrogen can also be used as a replacement for coal, and ArcelorMittal is testing that in Hamburg. However, hydrogen availability could prove an obstacle. “You have to make hydrogen, and if you make hydrogen from natural gas you lose much of the carbon benefit,” he says. That means hydrogen has to be made from renewable electricity. At the moment there is not enough renewable electricity out there to make all the hydrogen required, but that could change at some point down the line.
“Technically, we think all these different technologies will work and our commitment is to build industrially sized pilots to see if they do,” asserts Knight. “That will give us a better sense of the costs and unintended consequences. The next step will be to have a conversation with policymakers. Do they want us to use all of this waste wood or hydrogen? Will there be policies in place to allow us to be competitive? Over the past 200 years, innovation has created a very efficient way of making steel, but carbon wasn’t a problem. We now have to reinvent our process to make it without carbon.”
Setting a standard
Cleaning up steel production is just the first step. The industry also needs some sort of standard to help buyers distinguish steel that has been produced in a responsible manner from steel that hasn’t. “We need a way to reassure our customers that all ESG (Environmental, Social and Governance) criteria are being adhered to,” says Knight. “Customers are increasingly asking us questions about health and safety, pollution, carbon, and raw materials. They want to know where our raw materials come from and if we can reassure them that our mine sites are free from child labour and conflict minerals.”
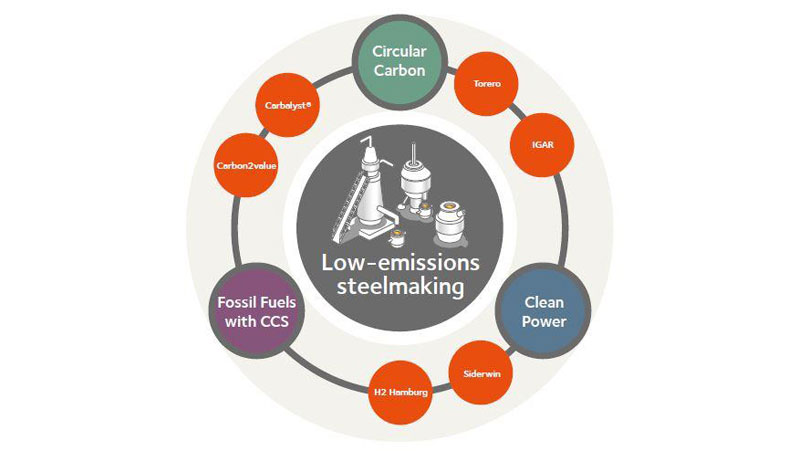
The problem is that different customers have different standards and protocols. A standard that covered all ESG issues both for mines and for steelmaking could help. Companies could then have their sites independently certified against that standard. They could also ask the mines from which they buy to meet the equivalent standard for mining. Then anyone could offer this certification as reassurance for their customers.
Enter ResponsibleSteel, a not-for-profit organisation that lays out the industry’s first global multi-stakeholder standard and certification initiative. The standard was announced in December 2019 and consists of 12 principles: corporate leadership; ESG management systems; occupational health and safety; labour rights; human rights; stakeholder engagement and communication; community engagement; climate change and greenhouse gas emissions; noise, emissions, effluent and waste; water stewardship; biodiversity; and decommissioning and closure. It has attracted a wide range of members, from automakers like BMW and Daimler to construction companies like Lendlease and banks like HSBC.
“Rather than asking us thousands of questions and performing audits, customers can just ask for the ResponsibleSteel Standard,” says Knight. ArcelorMittal has just committed the whole of its European business to go down this certification route. “Over time, more and more of our sites around the world will be certified against that standard. We started talking to our raw material suppliers about getting their mine sites certified against the mining standard too. We are really getting on with it. In a year’s time, there will be steel in the marketplace certified against the standard. With members like BMW and Daimler, we already know this is something the automotive sector will take very seriously.”
Costs and competitiveness
The cost involved in meeting this standard will depend on where a specific site is at the moment. “The top 25% to 33% of sites should find this relatively straightforward,” says Knight. “That was the benchmark against which it was written. If a company is already working to good standards and has already embraced ISO certification, this should not be a big cost. If you have never done ISO before and you have loads of pollution problems, then of course there will be a cost.”
There are also membership and audit costs associated with ResponsibleSteel, which parallel the costs tied in with ISO certification. Looking ahead, there are plans to test a model where the individuals who are doing the ISO certification also do the ResponsibleSteel certification at the same time, to keep down the costs of the audit process. “It doesn’t have to be as divisive as it sounds. The idea is that a fair, responsible buyer will give steel sites a chance to catch up,” he adds. “We want the whole industry to improve. If a site takes two or three years to improve because it has some capex to address, the customers would still buy from that site if there’s a clear roadmap towards improvements.”
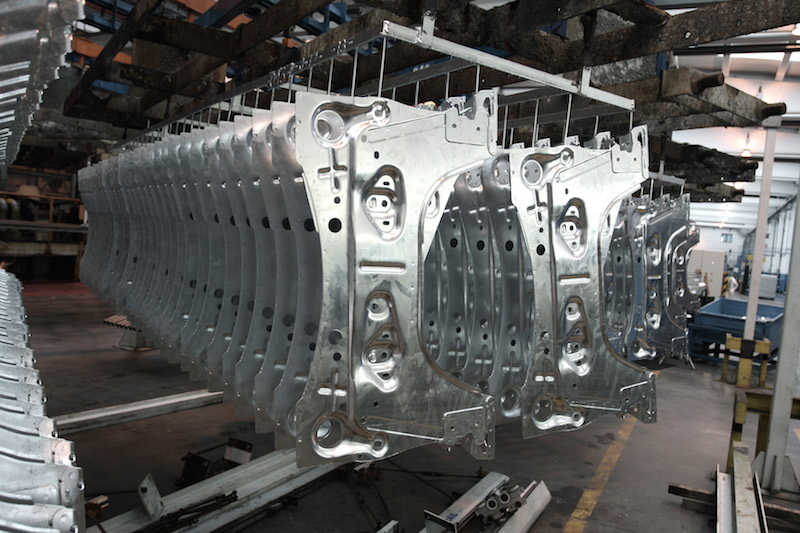
The challenge for many now is to remain competitive while paying the price on carbon, conducting R&D, and rolling out new technology. ArcelorMittal has been working with the EU on a campaign on the carbon border adjustment. Steel makers in Europe pay a high price on carbon, and many want steel brought into Europe to bear the same cost. “At the moment you can import steel into Europe and it doesn’t pay a price on carbon, but for steel made in Europe it does have to pay a price on carbon. How can that incentivise us to do more innovation? If you were one of our customers, what choice would you make?”
ArcelorMittal has been vocal in arguing that if a price on carbon is going to be one of the mechanisms to drive the transition to low carbon steelmaking, it has to be applied fairly. “Remember, we can buy steel globally. It’s not like electricity, which we can only buy from where it’s made. You don’t import electricity from China but you can import steel from China.”
The success of low-carbon steel will also hinge on the automakers, many of which have pledged to achieve net zero emissions as soon as 2030. But they have options in how they achieve that. “If the automakers have promised that there will be no carbon in their cars, then they have to decide what materials they will use,” he warns. “They will use steel because it makes cars strong and light.”
Will they preferentially choose advanced steels made by some of these new technologies? There’s no set answer at this stage, but Knight is cautiously optimistic. “Everybody would love the steel industry to be completely zero carbon by 2050. Is that realistic? Well, it is certainly possible,” he states, “but we cannot do this alone. While we can find the technology, we need policy to help ensure that this technology keeps us competitive. Hence the need for us to work with governments to create those policies whilst our commitment to helping ResponsibleSteel creates an auditable standard that will ensure that claims made by steel makers are consistent and accurate. Then we will give the automotive sector the ability to choose its steel based on its CO2 footprint.”