When it unveiled its Freightliner-branded SuperTruck concept at the 2015 Mid-America Trucking Show (MATS), Daimler Trucks North America (DTNA) illustrated the future technologies that it believes will enable the trucking industry to improve fuel efficiency.
The concept truck achieved some impressive figures, not least of which is its ability to return 12.2 mpg – double the current industry average.
Megatrends spoke to Derek Rotz, Senior Manager, Advanced Engineering at DTNA and Principal Investigator for the SuperTruck programme co-funded by the US Department of Energy (DOE). In the interview, Rotz outlined the challenges, hurdles and issues surrounding some of the technologies included in the SuperTruck.
What message does the SuperTruck convey to the industry? The Freightliner Supertruck concept suggests that a 115% freight efficiency improvement will be achievable in the near future.
SuperTruck is an R&D programme to investigate high-risk, high-reward technologies that improve the efficiency of Class 8 vehicles, and ones that Daimler may not have otherwise pursued. It is really about understanding what is technically possible, in addition to identifying existing hurdles that have prevented the adoption of various technologies.
We estimate that about 60% of the efficiency gains over the 2009 baseline model consist of current and near-term technologies – things that we either already see on the road today or could be ready within five years without major hurdles.
Do you believe 12.2 mpg will be reached and surpassed in future models through the advancements made in the SuperTruck programme?
The final SuperTruck demonstration vehicle contains a mix of technologies that contributed to the 12.2 mpg measurement. These include systems that are currently feasible, systems that have potential but where hurdles remain, as well as systems that are not feasible.
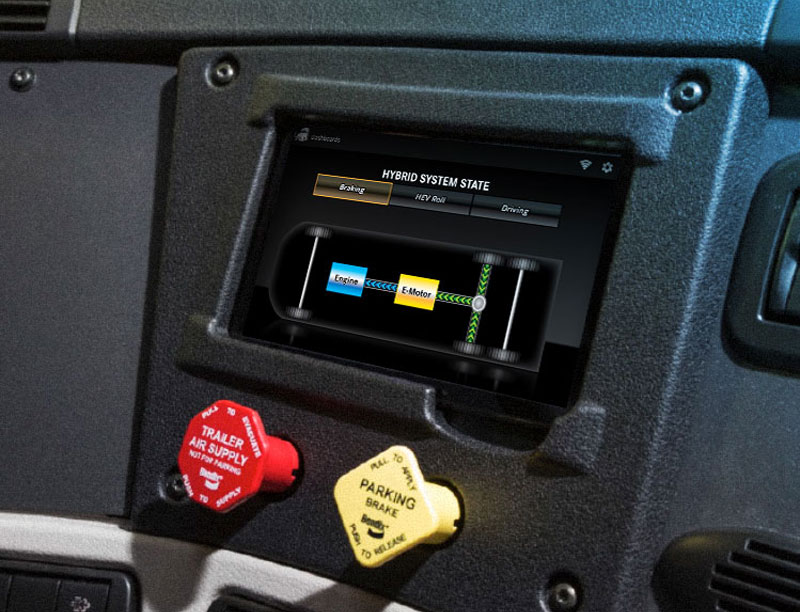
How did you decide which technologies to use for this concept truck?
Several SuperTruck solutions were ready for immediate technology transfer, including the aerodynamic package on the current Freightliner Cascadia Evolution and the integrated Detroit Powertrain launched earlier this year. In other cases technologies are not feasible, as they may still be too immature, or the customer payback period would not make economic sense. The hybrid electric powertrain, waste heat recovery and lightweight materials are examples of these.
Also, in other instances, such as the rearview camera systems, regulations that mandate mirrors impede technological progress. Current Federal Motor Vehicle Safety Standards won’t allow these camera systems, which could improve trucks’ efficiency by 1.5%. We [DTNA] have petitioned the National Highway Traffic Safety Administration (NHTSA) to modify the regulations to eliminate required exterior mirrors when replaced by cameras to improve aerodynamics and achieve optimal visibility.
In the future some of these concepts might mature and the ROI might improve, but for now the heavy system demands of a commercial truck and the costs of implementing these technologies don’t make them practical for deployment. The SuperTruck project gave us the opportunity to really explore and understand the potential and hurdles of these challenging technologies.
What are the primary components of the SuperTruck that improved its efficiency?
Major contributors to freight efficiency on the SuperTruck include enhancements to the core engine, external tractor and trailer aerodynamics, an improved powertrain including a 2.28:1 rear axle ratio, smart 6×2 axle configuration, eCoast, direct drive AMT and low rolling resistance tyres.
How do the SuperTruck and its technologies fit in DTNA’s portfolio? Will future models reflect the programme?
We have long been a leader in fuel efficiency for commercial vehicles. This is reflected in the success of our flagship products, including the Freightliner Cascadia and Detroit engines. The company continues to innovate and make constant improvements, most recently on the Cascadia Evolution, which was launched in 2013, and the integrated Detroit Powertrain launched earlier this year.
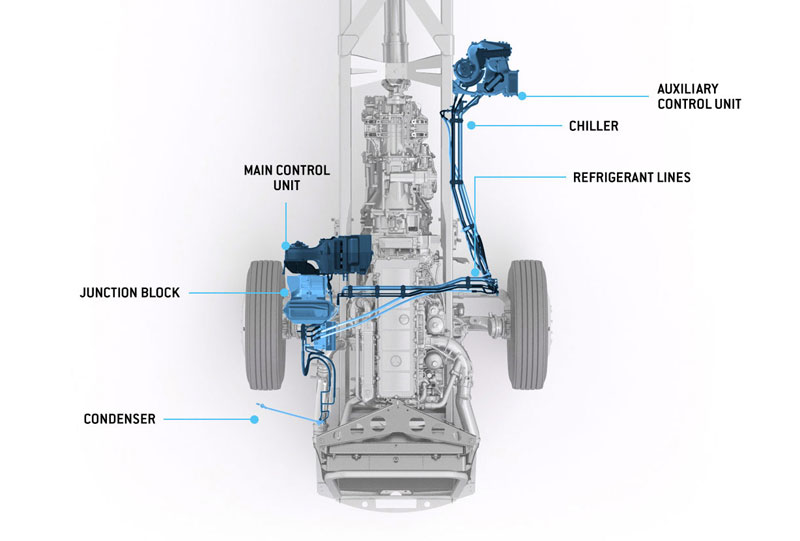
What is the benefit to Daimler of being so heavily involved in the DOE’s SuperTruck programme?
Daimler seized the opportunity to work on SuperTruck, since it is a natural extension of our core strategy to maintain fuel efficiency leadership. Efficiency is embedded deeply in the company’s DNA. It makes Freightliner products competitive, but equally important is the positive impact it makes on the profitability of our customers to reduce their operating costs as well as the environmental benefits provided by improved efficiency.
If you were to suggest one aspect of the SuperTruck for the industry to take on board in the next generation of trucks, what would it be?
Integration is one key takeaway that can make or break the SuperTruck design. Previously, we tended to think about efficiency as a collection of technologies that contribute more or less independently to efficiency. But that is only part of the story – it turns out with SuperTruck, system interaction also provides huge benefits.
For example, SuperTruck studied aerodynamics of the tractor and trailer systems. When looking at the tractor and trailer as a single unit, you can attack drag much more effectively. The team also discovered that improved aerodynamics opened up opportunities for the engine, and efficiency gains from aerodynamics mean less torque is needed to drive down the road. This allowed us to downsize and downrate the engine to match the SuperTruck, further reducing fuel burned.
If the components are all integrated, do they end up competing for the same job?
Yes. Integration doesn’t always amplify benefits, and multiple systems may in fact compete for the same inefficiency. A parallel hybrid electric powertrain was incorporated in SuperTruck to manage kinetic energy while driving across hilly terrain. Another onboard system, called ‘Predictive Technologies’, uses GPS, 3D-digital maps and clever software to adjust the cruise speed, shifting and coasting, optimising kinetic energy across terrain.
In one case, a large expensive and heavy system is used to save fuel across terrain. In another case, software alone is used to achieve the same ends.
How significant are the lessons learned from the SuperTruck programme for DTNA moving forward?
It is very significant to have a deep understanding about the potential of SuperTruck technologies and to have identified hurdles that prevent widespread adoption. For technologies that demonstrated a positive business case, the benefits can be seen in today’s product from Cascadia Evolution to the integrated Detroit Powertrain. As for other technologies, we now understand whether or not it is even possible to overcome the hurdles based on how significant they are.
What can we expect from the company next, in terms of bringing breakthrough technology to the truck segment?
Over the course of the programme, the knowledge gained from SuperTruck was used to support enhancements on production vehicles. Moving forward, DTNA will continue to refine what we’ve learned and achieved during SuperTruck, and use the knowledge, skills and tools we acquired in the process to bolster our leadership in fuel efficiency.
Michael Nash