Modern vehicles can often be made from more than 30,000 parts, which automotive manufacturers source from a global network of suppliers. The sheer scale makes the automotive supply chain extremely intricate, posing challenges from different perspectives: production, operational and compliance with supply chain regulations. The shift towards electric vehicles (EVs) has added to these pressures, increasing reliance on specialist materials and parts like semiconductors, rare earth elements, and aluminium. These are sourced globally, including from regions with records of alleged human rights abuses and poor environmental practices, which poses both a reputational risk and the prospect of non-compliance with recent modern slavery and corporate social responsibility regulations.
There has been a continued release of new regulations for UK car manufacturers to adhere to, such as the German Supply Chain Act and Corporate Sustainability Due Diligence Act. Yet understanding and adhering to a shifting legal framework can overburden risk and compliance teams, particularly when working across several jurisdictions. Nonetheless, the onus is on car manufacturers to comply, assess, understand, and mitigate risks and ensure they are not breaking the law and putting their business’ reputation on the line.
For automotive manufacturers to remain compliant with various regulations, it is important to adapt their approach to supply chain due diligence. Firms that embrace a data-driven, proactive approach that goes beyond traditional supply chain management can anticipate and address potential disruptions and bad practices before they occur.
An evolving regulatory landscape
The regulatory environment for automotive manufacturers is becoming increasingly complex as governments introduce regulations focused on human rights protections, environmental sustainability, and forced labour prevention. To comply with legislation, companies must adopt a holistic approach that extends transparency and due diligence practices across their entire supply chain. However, risks can become increasingly difficult to detect the deeper they lie within a supply chain.
Germany’s Supply Chain Due Diligence Act, introduced in 2023, requires companies to ensure compliance with human rights and environmental standards across their entire supplier network. Similarly, the EU’s Corporate Sustainability Due Diligence Directive mandates that firms operating within the EU conduct comprehensive due diligence across their “chain of activities” to ensure compliance with human rights and sustainability standards. Together, these laws signify a growing trend toward greater scrutiny of manufacturers vendors, and partners.
Greater supply chain transparency and accountability require car manufacturers to adapt compliance efforts to cover the entire network, including Tier N suppliers. This increased scrutiny is especially relevant in the procurement of materials for EVs, such as aluminium or nickel, which is at risk of being sourced from regions with reports of incidents of forced labour and human rights violations.
A combination of a proactive, data-driven approach and technological solutions will equip firms with the tools to build supply chains that are resilient, adaptable, and capable of navigating increasingly complex global landscapes
Facilities in these regions are reported to operate under a “production first, safety later” approach, where poor safety standards and inadequate protective equipment contribute to high-accident rates. Furthermore, these materials, which are essential to EV production, may be entering global supply chains without clear traceability, which creates obstacles for automotive manufacturers attempting to verify that their sourcing is free of violations.
The automotive industry also faces increasingly stringent environmental regulations. Beyond mandating stricter CO2 emission standards for vehicles, the EU’s 2020 new circular economy action plan announced several initiatives aimed at reducing the environmental impact of industries across the entire product lifecycle, including in the resourcing and supply chain stages. Regulatory requirements similarly extend to EVs, with the EU’s 2023 Batteries Regulation introducing sustainability requirements for batteries entering the market, which apply to all supply-chain operators.
Identifying risk in automotive supply chains
Companies that fail to meet regulatory requirements can face financial and reputational consequences. In one high-profile case, investigations revealed links between an automotive manufacturer and forced labour camps through a raw mineral sub-supplier. The case highlighted the issues car manufacturers can face in ensuring ethical practices within complex supply chains, particularly in places where government restrictions limit transparency and operational control.
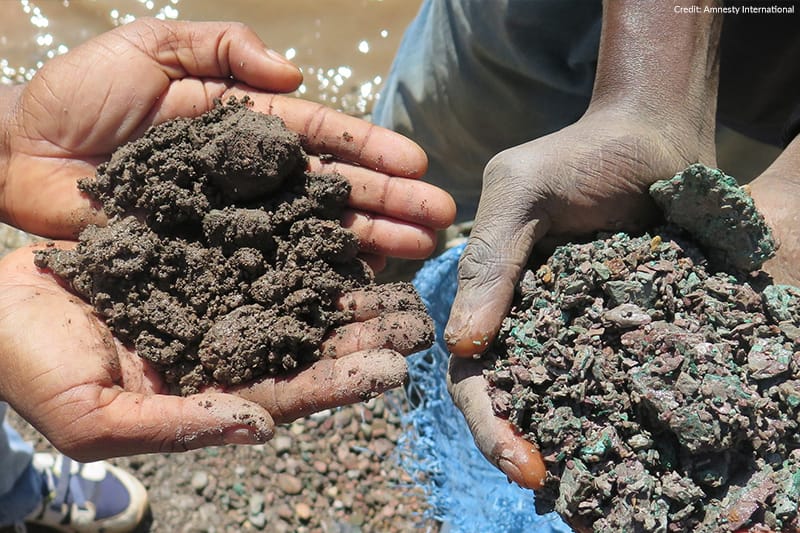
Yet human rights violations are a global threat. Incidents in the EU rose by nearly 17% between 2022 and 2023, and almost doubled over the past five years, according to data from Moody’s Grid database.
Climate-related risks also present supply chain issues to automotive makers. Recent flooding in Valencia inundated warehouses and distribution centres, halting operations, delaying the movement of parts, and forcing one manufacturer to shut down its plant, leaving hundreds of workers stranded. Traditional approaches to supply chain risk management are unable to accommodate the new and more frequent risks posed by climate-related incidents.
Economic policy changes, such as the potential introduction of new tariffs under the incoming US administration, could have implications for global supply chains. A potential 10% tariff on all non-US goods, specifically targeting German car makers, would significantly raise costs for companies exporting to one of their largest markets. As the automotive sector supply chain is so dependent on global networks to source parts, any financial deterrent may push automotive manufacturers to restructure their operations and diversify their suppliers.
Diverse risk factors within supply chains call for a comprehensive risk management strategy that considers every layer of a manufacturer’s operations. Adopting a proactive, data-driven approach can mean car manufacturers can establish more resilient frameworks to anticipate and address potential disruption and threats before they escalate. A holistic, integrated strategy not only helps ensure compliance with existing and new regulations, it also enhances resilience and operational agility, enabling companies to navigate an increasingly volatile global landscape with greater confidence.
Navigating supply chain complexity
De-risking begins with rigorous supplier evaluation, including financial stability, business practices, and relationships with potential illicit actors. Compliance teams should revisit these assessments regularly as risk factors evolve, as a single incident can jeopardise the entire supply chain leading to regulatory breaches, costly delays, and reputational harm.
Effective risk management demands technological solutions to help anticipate and mitigate potential threats. Automated solutions can play a crucial role by streamlining compliance processes and enabling continuous monitoring of supplier risk profiles across an entire network. These tools can curate risk profiles into a unified platform, which is continuously screened and updated with robust data on key risk factors such as negative news related to forced labour, sanctions exposure, and changes of ownership that may present a high risk.
Additionally, a ‘value at risk’ model offers strategic tools to help prioritise and address the most critical threats within a supply chain. By quantifying the financial impact of potential disruptions, the value-at-risk model enables firms to allocate resources more effectively, focusing on high-risk suppliers and scenarios. A combination of a proactive, data-driven approach and technological solutions will equip firms with the tools to build supply chains that are resilient, adaptable, and capable of navigating increasingly complex global landscapes.
The blueprint for more resilient automotive supply chains
The automotive industry stands at a critical juncture. Regulatory frameworks such as the EU’s Corporate Sustainability Due Diligence Directive and the EU’s Batteries Regulation emphasise the need for greater transparency and sustainability across every tier of a supply chain. Compliance with these laws is essential to avoiding financial and reputational damages and inadvertently perpetuating poor practices that can harm human rights or the environment. Compliance is therefore also crucial for maintaining trust with consumers and stakeholders who increasingly demand ethical and environmentally responsible practices.
About the author: Enrico Aresu is Compliance and Financial Crime Industry Practice Lead for the DACH and central-eastern Europe regions at Moody’s