Alongside many other buzzwords today, ‘Industry 4.0’ has become a widely accepted term for the digitalisation of manufacturing. However, whilst various tiers of the automotive industry are vocal on the benefits of a ‘smart factory’, it is difficult to quantify exactly what these benefits will be for a large supplier or OEM at this point. At the same time, it is also unclear as to when Industry 4.0 will become a reality.
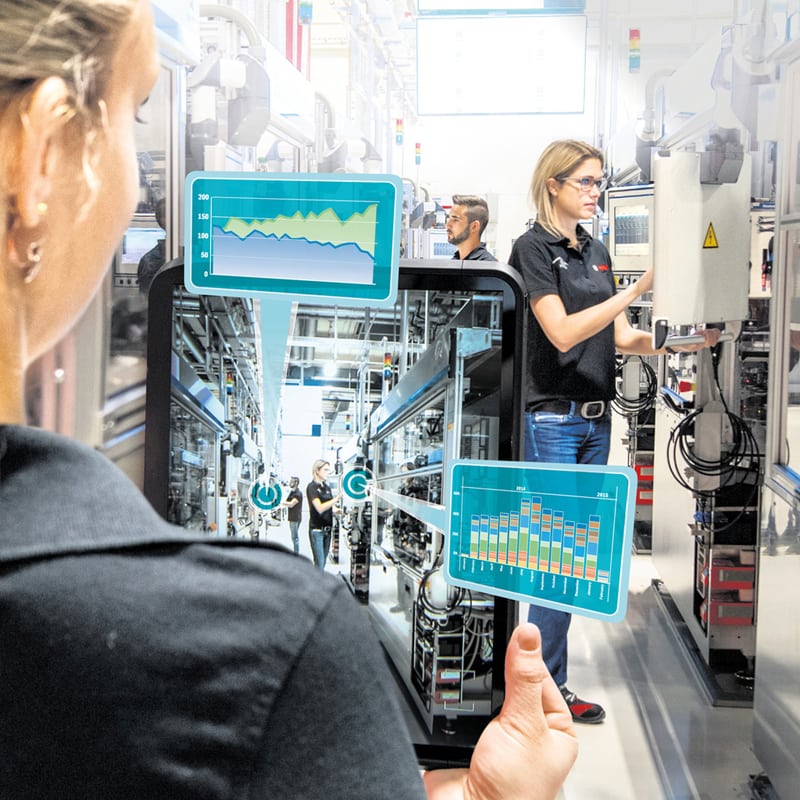
That was the sentiment shared by many industry figures during a panel discussion at Bosch Connected World 2018, a conference hosted by the German Tier 1 supplier in Berlin. Some cautioned that it is vital to develop more of a defined understanding of how Industry 4.0 will affect automotive manufacturing in order to realise its full range of benefits.
“Industry 4.0 is not a defined process, or a defined product,” remarked Rolf Najork, President of the Executive Board at Bosch Rexroth. “There are individual solutions that make sense, and many different use cases. But why should a customer invest billions to ensure a plant is 4.0 ready? This needs to be clear.”
The head of Daimler’s Industry 4.0 – Smart Operations unit, Günter Kruth, noted that Industry 4.0 has been interpreted as a marketing ploy by some, but highlighted some basic principles to the concept. “This digital transformation is about a dramatic change in demand. We not only have more products, but also more differentiated products,” he explained. “In terms of the potential, it is a question of efficiency and coping with this increased complexity.” Pushed further on his views, he conceded that “there is no single number that outlines the benefits of manufacturing digitalisation.”
“Why should a customer invest billions to ensure a plant is 4.0 ready? This needs to be clear.” – Rolf Najork, President of the Executive Board, Bosch Rexroth
Jörg Gnamm, Partner and Director at Bain & Company, underlined that there is still widespread uncertainty as to what Industry 4.0 can offer manufacturers in quantitative terms. “What do we mean when we talk about manufacturing 4.0? When I talk to ten people, I get 12 answers,” he remarked. “It varies between companies.”
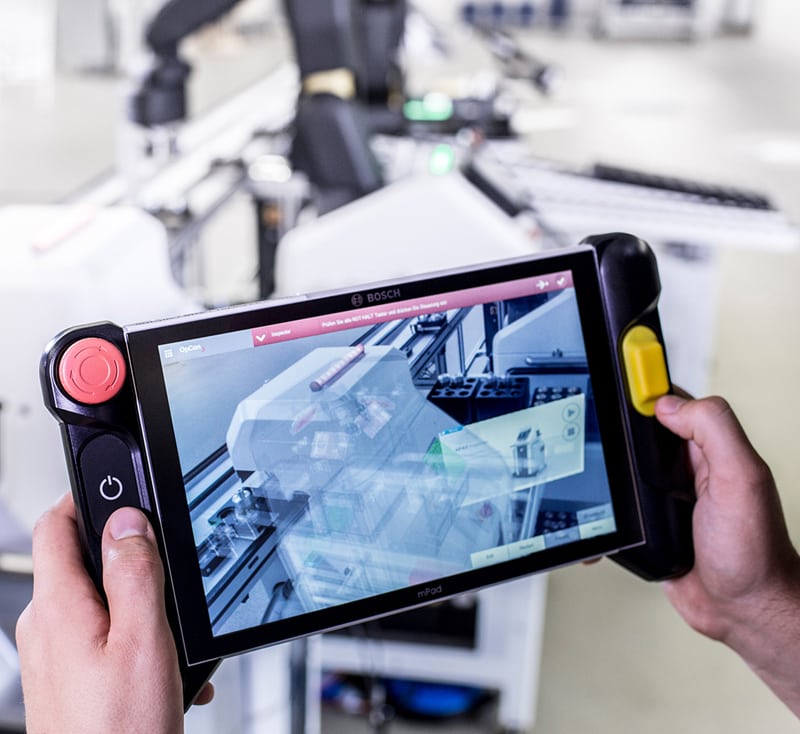
Increased efficiency
Despite such uncertainty, the industry is taking this trend seriously. In January 2018, Bosch formed a dedicated Connected Industry business unit to focus on Industry 4.0 activities and link the trend to Bosch’s various other business areas. By 2020, the supplier aims to ‘exploit’ Industry 4.0 to grow annual sales by more than a billion euros.
In qualitative terms, the underlying benefits of Industry 4.0 are a little more distinct: increased productivity, better capability to react to changes in demand and a faster time to market at a lower overall cost. Indeed, for most it simply boils down to increased manufacturing efficiency, but Bosch Rexroth’s Najork explained that even this is difficult to quantify. “If I gave you a number, it would probably be wrong anyway,” he said, but suggested “a double-digit percentage improvement in efficiency” would be a reasonable target as a result of Industry 4.0.
“There is no single number that outlines the benefits of manufacturing digitalisation.” – Günter Kruth, Industry 4.0 – Smart Operations, Daimler
As for the factories themselves, Najork suggested that they will not only be able to process vehicles and components at scale, but also adapt to certain ‘custom’ products such as a new small-batch vehicle. Factories will become ‘highly variable’ with changeover times of minutes, helped in part by new advances in 3D printing. Conductive charging could even be provided by the factory floor itself to power certain machines and robots.
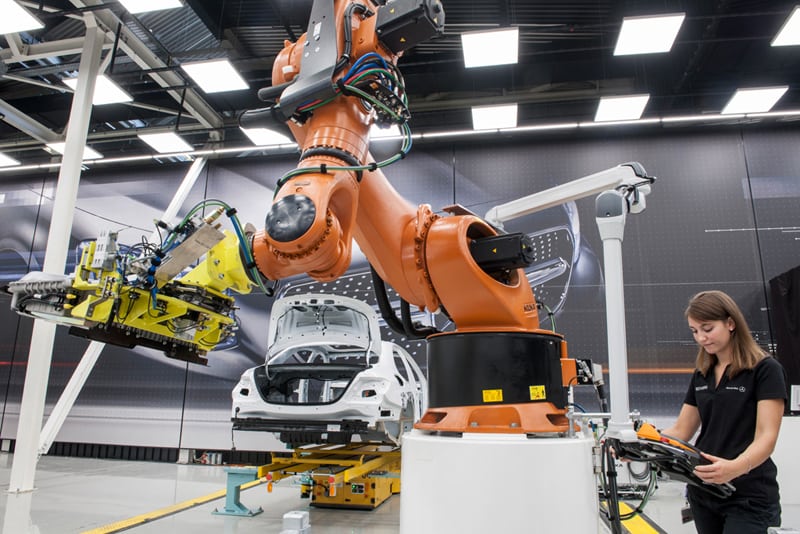
He also suggested that as part of this highly flexible approach to manufacturing, there would only be six fixed parts to the smart factory: four walls, the ceiling and the floor. “Everything else is flexible and dynamic,” said Najork. “But these trends are quite contradictory: high automation, but with high flexibility,” he observed. “In automotive, customers work with an eight to ten-year investment period, whereas the tech industry works in months or years.”
There will also be greater reliance on transport robots known as automated guided vehicles (AGVs) – which are already used by many factories today to transport parts around the factory. Artificial intelligence (AI) will also play a greater role, not only in the operation of machines such as welding robotics but also through predictive maintenance. This will allow machines to carry out their own wear and tear calculations to see how long they will last between services or to provide early warning of a shutdown. “If an operation comes to a standstill, that is a problem,” affirmed Najork. “We need predictive tools to make sure that does not happen.”
“There’s no cookbook to provide steps in the move toward Industry 4.0.” – Jon Sobel, Chief Executive of Californian manufacturing analytics firm, Sight Machine
Bosch Rexroth is currently working on a 5G internal connectivity service to be provided within factories, which would enable many new connected devices to run in harmony. As Najork puts it, this would create a ‘wireless’ factory. “This will be the biggest hurdle – we should not underestimate that,” he admitted.
More automation, fewer people?
There are concerns that Industry 4.0 may also have wider societal impacts, with greater use of automation and robotics eating up employment opportunities for humans on the factory floor. However, the dystopian view of a robot-run factory is unlikely. Instead, there will simply be a shift of competencies.
“We need to take people with us when we move to automation, and educate them about the impact and how it will work,” advised Daimler’s Kruth. He also pointed to the invaluable flexibility of a human operator, which cannot be affected by a glitch in software or a drop in power. “People are the focus. The manufacturing process will get more complex, but nobody is more flexible than our people,” he continued. “At the shop floor level, the manufacturing line is becoming more complex and we have to give our employees the tools to better handle that.” This should entail a mixture of both new skills and ‘tweaks’ to existing ones, he suggested.
Others agreed that while certain human roles could be phased out in the factory, they will be replaced by new opportunities elsewhere. “We will see a loss of jobs due to automation and robots, but also an increase in new ones,” remarked Bosch’s Widmer.
Jon Sobel, Chief Executive of Californian manufacturing analytics firm, Sight Machine agreed, noting that “when bank tellers were replaced by ATMs, that opened up new opportunities elsewhere in the banking business.”
There’s no cookbook for Industry 4.0
One of the primary hurdles in rolling out Industry 4.0 across the automotive sphere is encouraging change at a corporate level. Speakers at the event urged corporate executives to embrace connected factories in the way that they have with passenger cars and heavy trucks.
“The biggest challenge is not the technology, it is organisational change and the approach for a large company to bring in innovation,” explained Sobel. “There’s no cookbook to provide steps in the move toward Industry 4.0, but the best practices for Industry 4.0 from a corporate level would include strong leadership to knock down those walls and adopt these technologies,” he continued. “Companies need to think of the ability to change as a skill.”
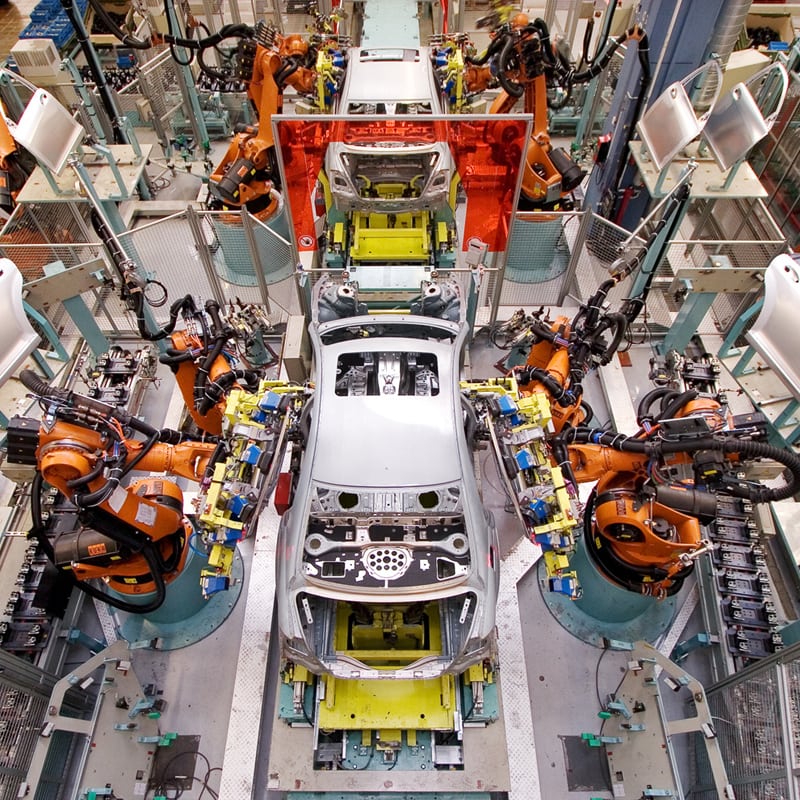
Najork noted that if corporations are to embrace Industry 4.0, the transition needs to be as painless as possible, and bring swift returns. “You can’t have a big lead time with manufacturing, and investments need to bring benefits very quickly,” he said. “It can’t take ten years to see the transformation.”
As for the current state of progress towards Industry 4.0, Thorsten Widmer, Vice President, Manufacturing Strategies and Investment Planning at Bosch, suggested that some automotive plants are already at ‘Industry 3.5’. While there may not be a cookbook that outlines the necessary elements and steps to achieve Industry 4.0, the recipe clearly contains two key ingredients: ambition, and uncertainty.
This article appeared in the Q2 2018 issue of Automotive Megatrends Magazine. Follow this link to download the full issue