It has always been important for automotive manufacturers to minimise vehicle weight to ensure the best performance and efficiency of their vehicles. The advent of battery electric vehicles (BEVs) has made lightweighting just as important for future vehicle efficiency. Automotive World asked Mark White, formerly Chief Engineer at Jaguar Land Rover and currently Technical Director for Alumobility, to explain the reasons behind lightweighting—and why he feels aluminium does the job best.
Why is it important to lightweight BEVs when fuel economy is no longer an issue?
Unless you are making anchors or steam rollers, there is always a need for lightweighting. Heavier vehicles use more power; that’s just the law of physics. Lighter vehicles use less energy to do the same task, so they use less fuel in internal combustion engine vehicles and produce less emissions. While the move to EVs means we don’t have to worry about fuel economy and emissions in the traditional sense of tailpipe emissions, we still use energy to power our vehicles, so minimising weight means less energy used.
As we reduce our reliance on fossil fuels and use more renewable energy sources, we can already see that there is a growing gap in energy supply and demand. This will drive up the cost of energy, so it is imperative we make lighter vehicles that use less energy, to reduce future running costs and infrastructure costs.
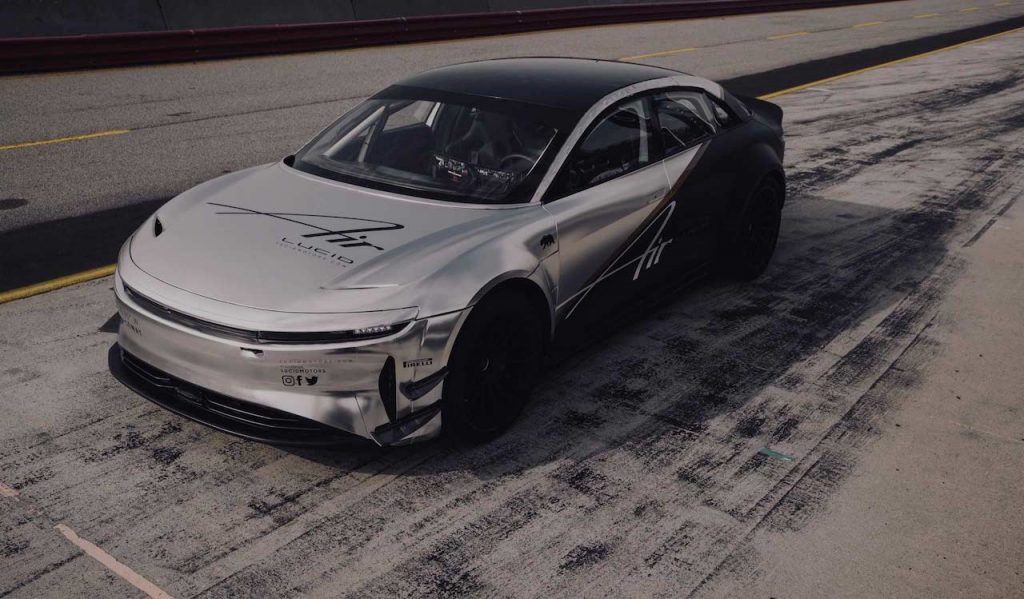
Moreover, lightweight vehicles are better for the environment. Even if we eliminate tailpipe emissions, vehicles generate other emissions, such as particles from tyre wear and brake pad wear, both of which get worse as the vehicle gets heavier. Vehicle production also generates emissions, and it is well documented that battery production and the elements that go into it can negatively impact the environment. Making a vehicle lighter can reduce the size of the battery pack, reducing total manufacturing emissions and energy consumption during the use phase. And you have less batteries to dispose of at the end of use phase.
What are other benefits of lightweighting vehicles?
For the past century, automakers have used aluminium to lightweight vehicles for a number of reasons: to achieve better performance, to make them accelerate and stop more quickly, to reduce the centre of gravity and improve the polar moment of inertia for better stability and handling. As mentioned, lighter vehicles also have less tyre and brake pad wear, which is good for the customer and for the environment.
For BEVs, a major issue for consumers is range and efficiency—they want to know they can drive until they reach their destination, without stopping to recharge. To make EVs efficient, the two key factors are aerodynamics and weight. You can make a BEV heavy if you want, it will emit no CO2e, but the battery will need to be bigger, and energy consumption will be higher. If a vehicle is lighter and more efficient, you can put in a smaller battery to get the same range, which reduces its cost. Or you can keep the same size battery for even greater range.
Just recently, the all-electric Mercedes Benz Vision EQXX concept car broke records by driving 1,000 km, from Sindelfingen, Germany, to Cassis, France, on a single charge. It was built using lightweight components, mostly aluminium, with only a 100kWh battery.
In the future, will lightweighting be achieved by a reduction in the volume of batteries, either through lightweight casing or better technology (e.g., Tesla’s new batteries with lithium-iron-phosphate (LFP) cathode)? And when batteries are lighter and more efficient, why will it still be important to lightweight vehicle bodies?
It is true that we must make our batteries more efficient and more sustainable in the future. However, battery technology is not like electronics; they need to be a certain size to provide enough energy. New battery technology, like LFP cathodes, increases efficiency, but it won’t double it. You’ll get maybe 10-15% more range.
Batteries are the most expensive part of the vehicle, by far. The cost to lightweight the body is substantially less, with the further opportunity of those secondary weight savings and related cost savings. Until the cost of lightweighting batteries is lower than the cost of lightweighting other major vehicle systems (such as the body structure, closures, and chassis), it is much better value for automakers to apply lightweighting to the primary vehicle systems to get the secondary weight benefits of smaller battery packs—smaller motors, smaller brakes, etc.—which all come with cost reductions that help offset any material cost increase of lightweight materials.
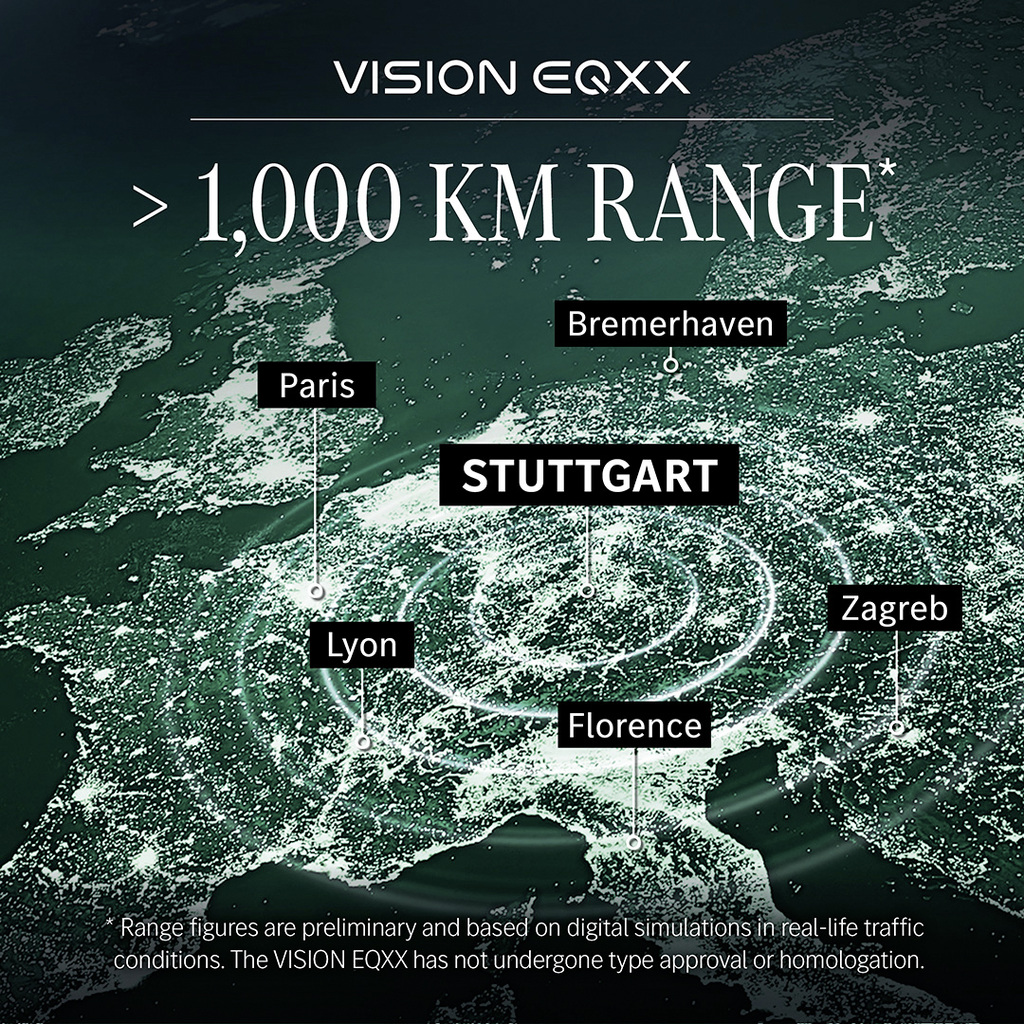
You mention the added cost of lightweight materials such as aluminium. Tesla, for example, used aluminium and advanced high-strength steel for its more affordable Model 3. Does this mean it no longer prioritises lighter materials?
Tesla has and continues to be an advocate of lightweighting. The Model 3 is a mix of aluminium and steel. The Model S and X are aluminium intensive, while the Model Y has aluminium in the structure as well as all-aluminium closures and chassis parts. This trend continues with aluminium giga castings being used more and more in Tesla vehicles, replacing mainly steel parts in their existing models. So in fact, aluminium content has been increasing in Tesla vehicles again.
And not just Tesla—if you look at the conversion from internal combustion engines to BEVs, we see a continuing trend of further aluminium adoption in BEVs, mainly to offset the increased weight of the powertrain (including the batteries) across all vehicle segments.
As long as battery costs are dominant, it is more efficient to make other vehicle systems from aluminuim. We are talking about at least another decade—and probably two—before battery technology will get to cost parity with lightweighting. So let’s act now, and in the future we can have both, and make our vehicles even more efficient than they are today.
As we move towards a circular economy and more recycling, does the choice of material used to make our vehicles matter less?
As we move towards a circular economy, automakers will use less primary material and more reuse and recycling of existing materials, to reduce the energy burden on the manufacture of vehicles. With its superior recyclability, aluminium is an ideal material for the circular system. Not only is it infinitely recyclable, but unlike other materials, it does not have to be downcycled—where the recycled material cannot produce the same performance or quality as the primary material. Aluminum as a secondary material uses only around 5% of the energy relative to the primary, and can match the quality and performance of the primary material grades it replaces, something few other materials can do in an affordable and sustainable way. It also requires less energy to recycle than other materials, as it melts at 650 degrees Celsius, compared to around 1,400 degrees Celsius for steel, making it better for the environment once again.
We don’t even have to wait to the end of a vehicle’s life before we can start the recycling process. We can reduce CO2e in automotive aluminium by adding closed-loop recycling into the part manufacturing process, ensuring any scrap is segregated and sent back to the material supplier for use in the next material supply. This system is already in place with automotive manufacturers such as Ford, Jaguar Land Rover, Volvo, and Nissan, and will become the industry standard as we move towards a sustainable manufacturing approach. This not only reduces manufacturing waste and emissions, but makes great business sense for automakers, and can be implemented relatively easily as they switch from steel to aluminium.
Aside from lightweighting and recycling, what are other benefits that aluminum brings?
Durability is one big benefit that may not be as obvious, but becomes clear when you compare a conventional 20-year-old steel vehicle with a 20-year-old aluminium intensive vehicle. Aluminium does not corrode in the same way steel does, so aluminium systems will have a longer service life than an equivalent steel system. When an aluminium surface is damaged, it forms a natural oxide layer protecting the material from corrosion. Steel cannot do this, so steelmakers use aluminium or zinc to protect the steel substrate. But if this is damaged or removed, then the steel will rust and continue to rust until it is repaired or perforates.
People may not be aware of the fact that aluminium absorbs more energy per kilogram than steel, making it not only lighter, but potentially safer in a vehicle crash. That is why there is a growing trend for more vehicle front and side crash structures to be made in aluminium. Aluminium also absorbs dings and dents better than steel, due to its Young’s Modulus, so it’s less easily damaged in car park and low-speed damage scenarios. Aluminium-bodied cars suffer less from stone chipping and general service damage than their equivalent steel-bodied vehicles. In short, there are many reasons that aluminium is becoming the preferred material for automakers as we move towards a sustainable future.