Steel has underpinned vehicle design since the industry’s earliest days due to its strength and cost-effectiveness. Despite growing interest in alternatives like aluminium and carbon-fibre, it remains the most widely used material in automotive production today. However, the process of making steel accounts for around 7% of the world’s carbon emissions.
The sector has seen notable advances in manufacturing techniques and both component manufacturers and automakers are increasingly prioritising the sustainability qualities of steel. But ‘sustainable’ covers a wide range of criteria under the ESG (Environmental, Social and Governance) umbrella. The question is, how to distinguish steel that has been produced in a responsible manner from steel that has not.
Setting the standard
ResponsibleSteel could be the answer. In December 2019, this not-for-profit organisation set out a standard for what ESG in steelmaking looks like. This global multi-stakeholder standard and certification initiative consists of 12 principles: corporate leadership; ESG management systems; occupational health and safety; labour rights; human rights; community engagement; climate change and greenhouse gas emissions; noise, emissions, effluent and waste; water stewardship; biodiversity; and decommissioning and closure.
“This came about as a consequence of customers asking us about ESG issues,” explains Alan Knight, Global Head of Sustainable Development and Corporate Responsibility at steel giant ArcelorMittal. Knight is also Co-Chairman of ResponsibleSteel and sits on the steering board of the Initiative for Responsible Mining (IRMA). “Customers wanted reassurance that nothing bad was happening at any of our steelmaking sites or the mine sites from which we buy. It wasn’t so much looking to go into deep eco-sustainability; at this stage, they just didn’t want to be embarrassed with bad things.” In the past there have been concerns about human rights abuses, child labour and environmental devastation at certain mine sites. And nobody, certainly not customer-facing brands, wants to be linked to that.
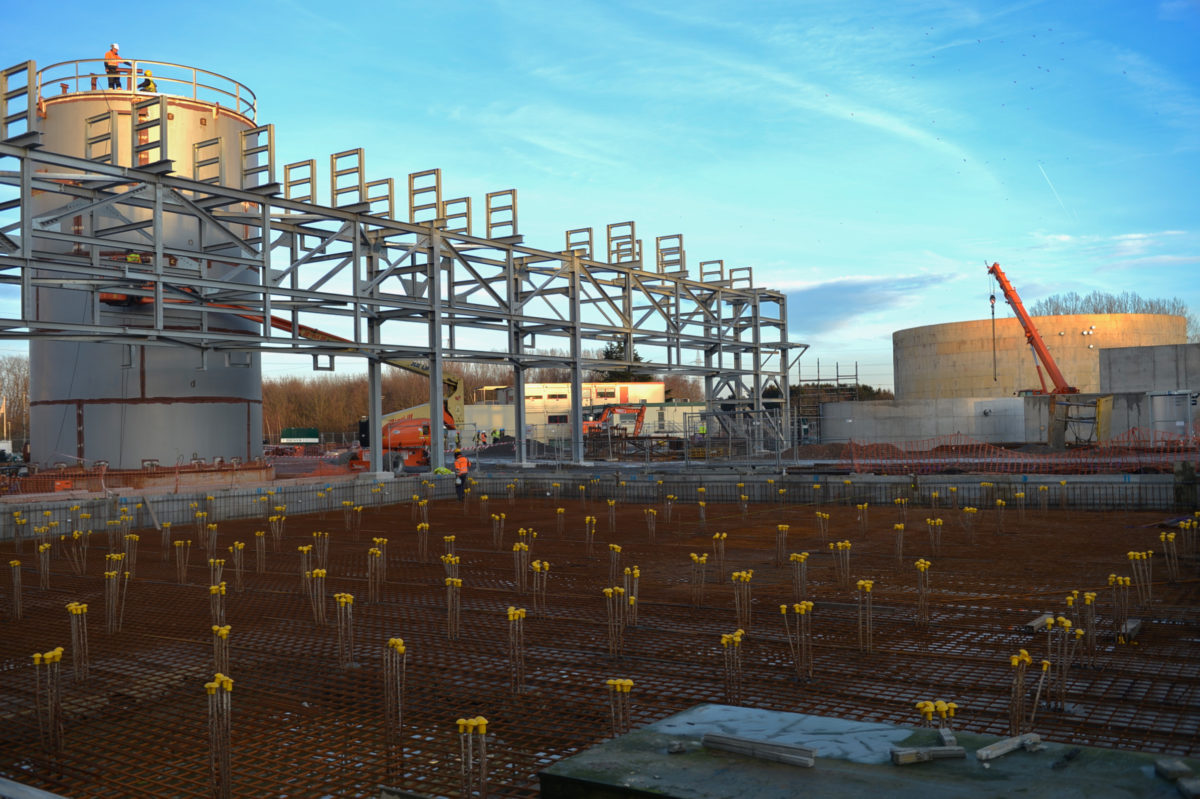
The challenge was on, and it proved incredibly complex. “You can’t just have a simple yes/no question for child labour, human rights or environmental degradation,” Knight points out. Luckily, he had experience on which to draw. Timber sellers in the 1990s faced the same problem of ensuring that their timber sourcing wasn’t resulting in destruction of the rainforest. Knight was involved in creating the Forest Stewardship Council, which developed a model to do that. This involved bringing together all the stakeholders—customers, suppliers, competitors, environmental and social groups—to agree what ‘good’ looks like and what issues need to be covered.
“You create a political process whereby that group agrees what’s good enough,” says Knight. “That then becomes the environmental and social standard for forestry. Now we’re looking at steel. In effect, the guts of ResponsibleSteel reflect what we did with the Forest Stewardship Council.”
Not just a gentlemen’s handshake
With the standard now set, the focus shifts to certifying sites that meet the standard. ResponsibleSteel oversees those independent site certification processes. By doing one very thorough audit, it avoids the need for an endless number of audits that potentially vary in breadth and depth from different customers.
ArcelorMittal, one of the leaders of the ResponsibleSteel initiative, began certifying its sites in Europe in early 2020. COVID-19 has slowed down the process—halting it entirely for a couple of months—as audits cannot be conducted remotely. It’s too soon to speculate on an industry-wide pass rate, but only those steel companies who think they can pass will go for certification; those that know they are nowhere near meeting it simply will not apply.
“You wouldn’t apply for something that you know you’re going fail. We are finding that our own sites in Europe have a good chance of passing but they have had to do some work on one or two principles,” Knight concedes. “As a board member of ResponsibleSteel, I see that as successful because it shows that the standard is of sufficient quality to detect minor non-conformances in a company. It’s not just a gentlemen’s handshake. It is thorough.” On average, an audit takes about 12 to 15 man days for a facility and is normally carried out by two people.
ESG doesn’t come cheap, but doing nothing can be costly
On the whole, the initiative is pushing this standard as a qualitative benchmark for which companies can aim. Very useful and efficient, but it comes at a cost. “Part of the motivation for this is to protect us from competitors that have bad things in their value chain and are enjoying lower costs because of that,” says Knight. “As we’re seeing with carbon, in steelmaking ESG doesn’t come cheap.” Steel is price sensitive but luckily there are customers that only want to buy a responsible product. Doing nothing will also come at a cost; it is about finding the mid-point.”
The initiative has attracted a number of big name global members spanning the whole spectrum of manufacturing. The automotive sector sees representation not only from ArcelorMittal but also Daimler, BMW, Tata Group and, most recently, Hyundai Group. European players dominate the member list, in part due to the heavy emphasis on ESG in the region, but with new members from Russia and Korea this will soon change. “We pretty much have the main players on the carbon debate,” he adds. “Given how sensitive people are to carbon in steel, that’s very important.” Looking forward, Knight anticipates welcoming more of the steel sector and its customer base.
Today, ResponsibleSteel certifies specific steelmaking sites, as opposed to steelmaking products. That could change. “There is an appetite to put a label on products and then pass it up and down the supply chain,” Knight tells Automotive World. The challenge is that this would entail coupling steelmaking with mine sites: confirming that a specific steel product has come from certified mines and certified production sites. “It means we have to think about the carbon footprint. That’s not just the carbon footprint coming out of our chimneys but would also include the shipping, the mining and all of that,” he adds. “The complexity of it all could be overwhelming but we are working on ways to make this work.”
Along with moving forward through the pandemic and growing membership, shaping a product standard, on top of the site standard that already exists, will be one of the initiative’s near-term focus areas. “At the moment there is a ResponsibleSteel carbon draft standard in circulation as well as a ResponsibleSteel raw material draft standard,” says Knight. “In the background, board members such as myself are talking about what the need is and how would we apply this. Ideally we want a label which helps the market buy the right stuff but we don’t want a label which is so complex that we seize up with the complexity.”
At some point, the industry could potentially see one label for the whole supply chain covering everything from carbon and raw materials to mine site certification. “We are handling it carefully,” he cautions. “It would be easy to make it overly complicated, but it would be fantastic if we get it right.”