As global shifts, trade disputes, and economic volatility continue to reshape global commerce, supply chain resilience has never been more crucial for the automotive industry. Tariffs have emerged as both a constraint and a prompt for companies to rethink sourcing strategies, deepen supplier partnerships, and strengthen procurement agility. Despite increased uncertainty, the World Trade Organization projects a 3% increse in global trade growth in 2025, resulting from decreased inflationary pressure. However, an air of unpredictability means this could all change in an instant.
The ability to anticipate and mitigate trade disruptions will define the competitiveness of automotive manufacturers and suppliers alike. Companies embracing flexibility and long-term collaboration in their procurement strategies will be best positioned to withstand uncertainty and maintain operational continuity.
A typical modern vehicle can contain between 15,000 and 25,000 component parts that often cross multiple global borders before final assembly. With even small changes in trade agreements, there can be ripple effects across the entire production process. The industry is at a heightened risk of increased costs, delays, regulatory hurdles, and production bottlenecks. These issues can no longer be treated as temporary changes but must be addressed through proactive risk management and strategic planning.
A new process for procurement
Historically, procurement in the automotive industry has been driven by price competitiveness. As traditional sourcing models are disrupted by the impact of changes in global trade, companies are finding a narrow focus on cost reduction can leave them vulnerable to sudden market shifts. Businesses are realising that a more sustainable approach prioritises supplier reliability, transparency, and shared business objectives.
Tariffs present the chance for the automotive industry to reassess its sourcing strategies and uncover efficiencies that may have previously gone unnoticed
Focusing solely on short-term cost savings in supplier selection, without considering broader factors such as reliability, transparency, and strategic alignment, can expose businesses to unnecessary risk. Cost competitiveness remains an important consideration, but it must be balanced with a supplier’s ability to support long-term operational continuity and shared business goals. Establishing deeper collaboration with key suppliers helps to ensure a steady flow of high-quality components while safeguarding against unexpected disruptions. A 2023 survey by Deloitte found that 79% of manufacturing executives believe supplier collaboration is critical to supply chain resilience, yet only 43% have structured programmes in place. A strong supplier relationship won’t happen overnight—it needs to be an evolving relationship built on mutual investment and a shared vision for growth.
One of the most effective ways to manage tariff-related risks is through structured supplier engagement programmes. Tiered supplier relationships—where businesses prioritise partners that demonstrate operational agility, proactive risk management, and long-term investment in innovation—offer a natural buffer against trade uncertainty. Companies that formalise supplier relationships will gain a significant advantage in managing trade-related disruptions.
Supplier engagement programmes create incentives for suppliers to maintain high performance and invest in shared business objectives, from technological innovations to sustainability initiatives. In return, suppliers benefit from greater transparency, access to executive support, and long-term business continuity. This reciprocal approach not only strengthens the supply chain but also ensures that companies can pivot more quickly when faced with external disruptions. Manufacturers can future proof their procurement strategies while fostering stronger, more aligned supplier relationships by integrating a framework that rewards innovation, agility, and reliability.
Adapting to a shifting market: the role of strategic sourcing
Tariffs present the chance for the automotive industry to reassess its sourcing strategies and uncover efficiencies that may have previously gone unnoticed. Some organisations are leveraging trade policy shifts to diversify their supplier base, reducing dependence on single-source suppliers and exploring alternative markets that offer competitive advantages. Nearshoring and regional manufacturing have gained traction as viable solutions, reducing logistics complexities and minimising exposure to volatile trade policies. Investing in regional suppliers not only mitigates risks associated with tariffs but also encourages economic growth in key markets.
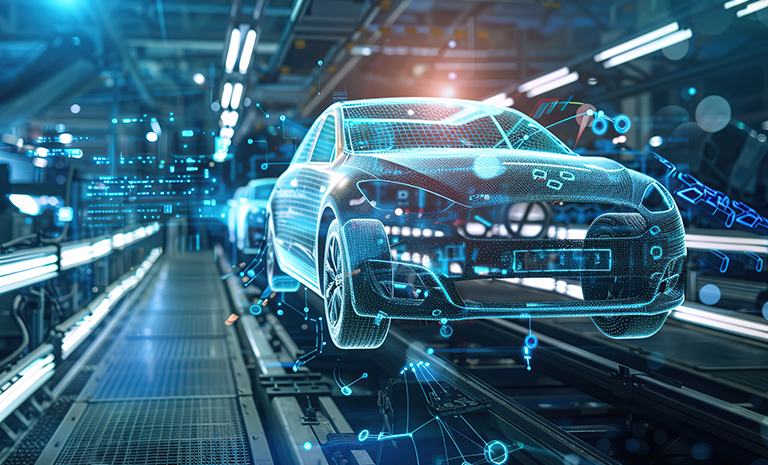
At the same time, the growing trend in some areas of the world toward reshoring manufacturing and reducing reliance on imports has the potential to reshape global supply chain dynamics. While this creates opportunities for local industry, it can also lead to constrained global sourcing options, capacity bottlenecks, and intensified competition for domestic supply. Companies must weigh the benefits of proximity and control against rising input costs and potential limitations in supplier availability. Balancing these pressures with strategic diversification remains critical to building long-term supply chain resilience in a more fragmented trade landscape.
Closer supplier collaboration can drive joint innovation efforts, particularly in areas such as value engineering, alternative materials, and localised production. By working together to optimise component designs and streamline manufacturing processes, suppliers and OEMs can uncover cost savings that help offset tariff-related expenses. This collaboration encourages suppliers to propose new materials or manufacturing techniques that enhance efficiency and sustainability. Auto companies that take a forward-thinking approach to supplier partnerships will be better positioned to capitalise on these opportunities while mitigating risks associated with shifting trade policies. The players that continue to operate with rigid, transactional relationships will struggle to adapt when new challenges arise.
Sustainability and supply chain resilience—mutually exclusive?
A significant part of the conversation around supply chain resilience must also include sustainability and ESG considerations. According to a recent report from BCG and CDP, Scope 3 supply chain emissions were, on average, 26 times greater than their emissions from direct operations. Despite this, Scope 3 emissions continue to be overlooked as only 15% of corporates have set a supply chain emissions target, according to the report.
As regulatory scrutiny on environmental, social, and governance factors increases, supplier selection should consider long-term sustainability commitments. Companies that align procurement strategies with sustainability goals will not only mitigate financial and regulatory risks but also position themselves favourably in an industry where environmental impact is under growing scrutiny.
Suppliers with a high share of renewable energy in their mix seemingly managed to get through the European energy crisis in 2022/2023 much better than those relying on gas and oil. Hence embedding sustainability into the supplier relationship framework ensures that resilience is truly built into the supply chain.
The road ahead for automotive supply chains
The automotive industry is no stranger to disruption. The current landscape, while challenging, presents an opportunity to rethink procurement strategies and build more resilient supply networks. Companies that remain flexible and invest in long-term supplier relationships will emerge stronger in the face of future trade challenges. The ability to turn uncertainty into opportunity will ultimately define success in the years to come. By embracing a mindset that prioritises collaboration, innovation, and agility, the automotive industry can create supply chains that are not only resilient but also primed for future growth in a sustainable manner.
About the author: Sebastian Dori is Chief Purchasing Officer at PHINIA