Automakers in the US and Europe have been keenly aware that China is the global electric vehicle (EV) battery supply chain hegemon. Most lithium-ion chemistries currently use graphite for the anode due to its low cost, high energy density, and long cycle life. Graphite-based anodes contain up to 95% of the mineral, constituting 20-30% of an EV battery’s mass. China extracted 1.23 million metric tons of graphite in 2023—more than the other global top ten producers combined, according to Nasdaq.
As global trade constricts, there is precedent for bans on the export of raw minerals from China, which could leave OEMs in a vulnerable position. In January 2025, General Motors sought to extricate itself from this risk through a six-year, multi-billion-dollar contract with Vianode, an advanced battery materials company developing synthetic graphite.
Originally part of Norwegian industrial conglomerate Elkem, Vianode began to take shape in 2016 and completed a lab pilot three years later. The company was carved out in 2021, with a 2,000-tonne full-scale production facility—Via One—opening in Q3 2024 in Kristiansand. With Vianode making rapid progress, Chief Executive Burkhard Straube informs Automotive World why he believes synthetic graphite is a better and more secure basis for the EV industry’s future.
What are the advantages of using synthetic graphite instead of natural graphite?
Since it’s a synthetic man-made product, we can play around with different elements, raw materials, and process parameters to tweak synthetic graphite’s properties according to use case. For EV batteries, that could mean boosting a unit’s fast charging capabilities, range, safety, and lifetime. This level of control also makes it a highly quality controlled and reproducible product, whereas mined graphite will naturally contain variances.
Scalability is also of the utmost importance in e-mobility: growth will be tremendous, even if it’s been slower than some anticipated so far, and battery material supply chains need to move with it. Opening a new graphite mine can take more than a decade, but a synthetic graphite manufacturing plant can be operational in two or three years. At a time when automakers need to establish resilient material sourcing, moving away from natural graphite enables them to build up capacity in their home markets.
How can Vianode’s product help OEMs meet their sustainability goals?
The largest ‘burden’ of CO2 in an EV is the battery, and the anode by itself represents about up to 40% of the total emissions. By focusing on this one component, we can make EV manufacturing far more sustainable than it has been so far.
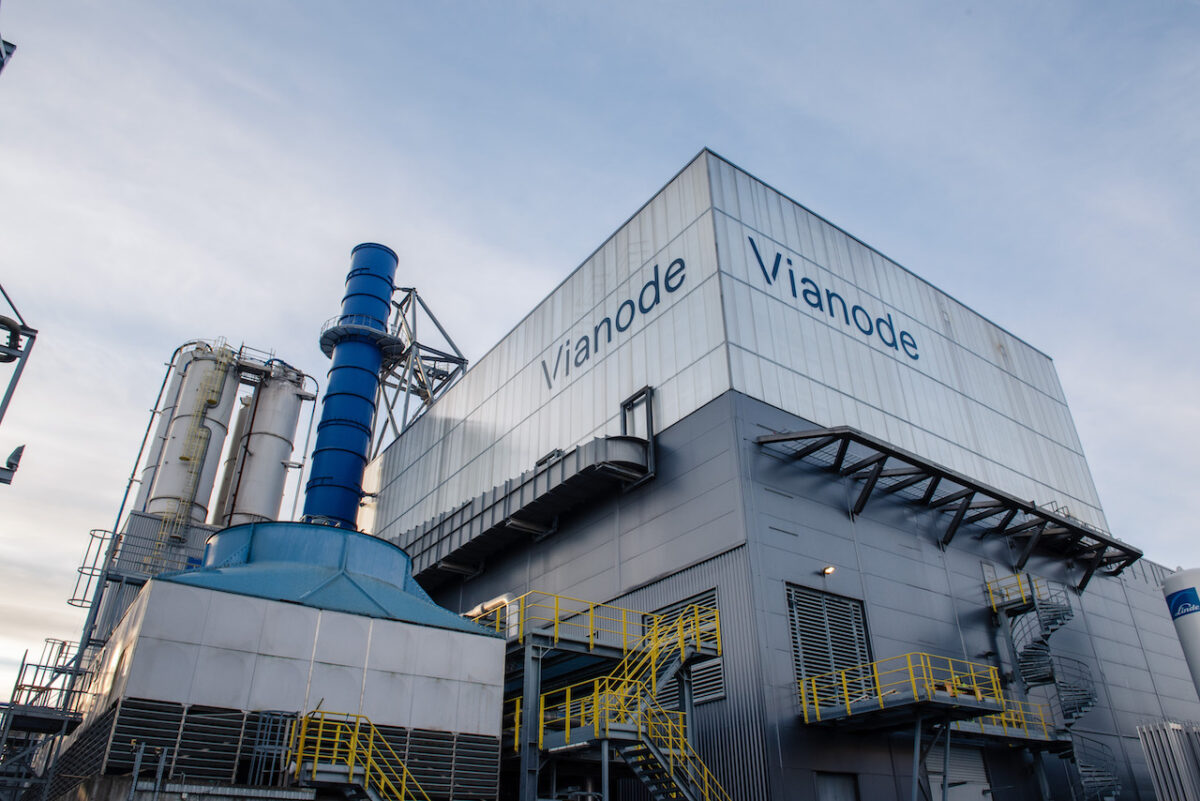
Around 60-70% of the graphite used in batteries today is synthetic, but most producers use huge, open pit furnaces. Vianode uses closed induction furnaces instead. This method eliminates diffused emissions, but it also grants us better control over the temperature and overall process. This results in a higher A-grade yield with less waste, reduced material consumption, and 40% less energy used. All of this combined with the use of ‘green’ energy at our plants means that Vianode’s graphite is 90% lower in CO2 emissions than comparable offerings on the market.
Is there any broader strategic value to choosing synthetic graphite?
The Western automotive industry is investing hundreds of billions of dollars into the e-mobility value chain, but all that funding hinges on reliably importing one product: graphite. In 2024, China limited export on several occasions, so building resilient local EV supply chains factors into what I call ‘strategic sustainability’ for automakers.
Are any automakers besides GM interested in working with Vianode?
Yes, although those talks are confidential at this time. We are going to build a plant in North America, which will go live in 2027, but we cannot disclose the location yet, as we are in final negotiations.
I believe the market for synthetic graphite will grow substantially in the near term. The first wave will focus on providing virgin material, but recycling will become more and more important from the mid 2030s. By the start of that decade, Vianode intends to achieve a capacity of 200,000-tonnes, which would be enough for three million EVs per year. From there, we plan to boost capacity even further in both North America and Europe.
What about the prospects for alternative anode materials like silicon?
Graphite is the workhorse of e-mobility; its main advantage is being battery chemistry agnostic, so it doesn’t matter if OEMs move towards lithium-iron-phosphate (LFP) or continue with nickel-manganese-cobalt (NMC) cells. I don’t think silicon can replace graphite. It’s expensive and has inherent structural deficiencies that cause the battery to degrade very quickly, making it unattractive for automakers that want long cycle life. Despite decades of research, these issues have not yet been resolved.
I think synthetic graphite is the only solution that can ensure Western supply chain resilience in an acceptable timeframe: years, not decades
On the other hand, even if industry-scale adoption looks unlikely, silicon does have potential as a ‘range booster’ by increasing battery capacity in some EV models, and Vianode is developing graphite materials with positive synergistic effects with silicon. On balance, silicon will probably co-exist with graphite, and that’s where the future of anode technology really lies.
How could synthetic graphite play an important role in growing global EV adoption?
Whether automakers want to improve their EVs’ charging abilities, safety or range, performance depends on the battery. Synthetic graphite can be tailored to brands’ individual requirements and help improve all of these aspects. By doing so, it mitigates the concerns of consumers and makes EVs more attractive as products.
Global anode supply chains are highly distorted today: there is massive overcapacity in China, which is becoming economically unsustainable for other markets. North America is actively tackling this issue, but Europe is not sufficiently engaged with levelling the playing field. Based on the current geopolitical situation, I think synthetic graphite is the only solution that can ensure Western supply chain resilience in an acceptable timeframe: years, not decades.