Currently, electric vehicle (EV) development costs are incredibly high, driven mainly by the battery pack, and balancing model appeal and cost is a challenge even for established automakers. Needless to say, this is even more difficult for many small manufacturers and niche vehicle makers, who can easily be quoted up to £30m (US$37m) on battery pack design alone. While there is a clear need for more cost-effective, streamlined product development solutions, there are still few out there. When faced with designing a battery pack many are still unclear about where to start or what to prioritise.
Energy density is a key metric for many, and an obvious priority for manufacturers. A battery pack which is not energy dense may lead to a vehicle which is heavy, large, and hard to drive—not a strong sell for consumers. However, what’s often forgotten is that increasing voltage can aid in increasing energy density. Many approach battery production with an engrained idea that 400v is the limit for EVs. As EV voltage can increase up to 800 or 900 volts, settling for a voltage of 400 unnecessarily caps the potential of the vehicle. EVs with higher voltage can produce the same power with a lower current, meaning the cables, busbars, and other components can be smaller and the pack becomes lighter as a result.
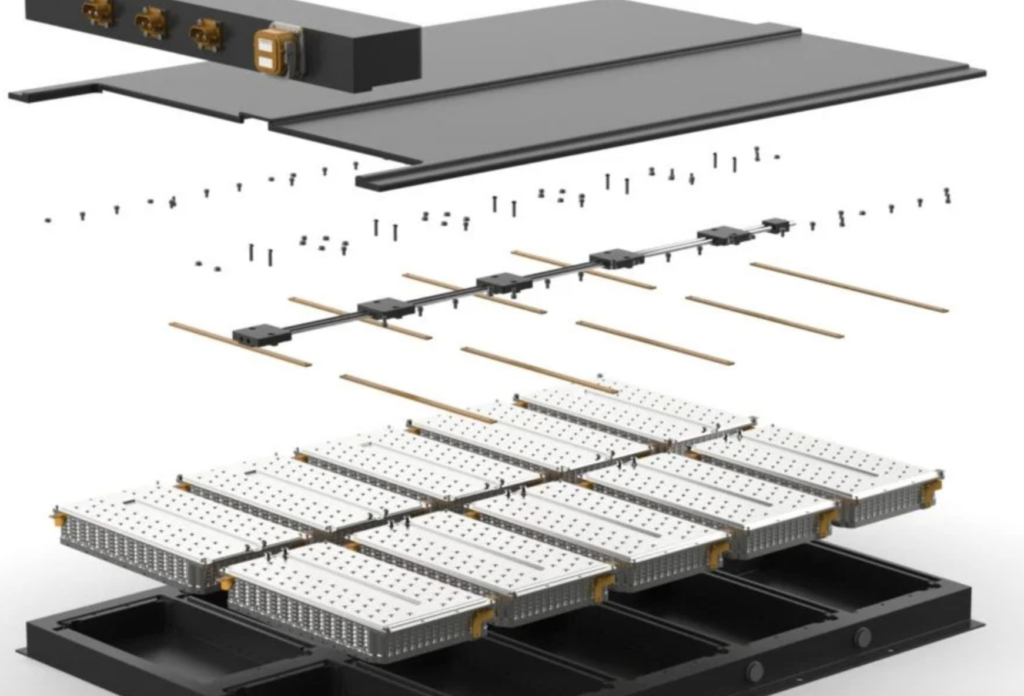
However, when it comes to designing a battery pack nearly every variable is dependent on another, and involves a trade-off of some sort. Voltage is not exempt from this. In general, as voltage increases, inverters and other components increase in size due to voltage isolation, and so the overall powertrain may become bigger.
This need to make considered trade-offs extends to other factors under consideration when designing a battery pack, and it’s important to understand that some combinations of parameters aren’t always attainable. The ability to consider design and truly understand what’s both important to your vehicle, and attractive to a consumer is pivotal. It’s often thought that a low charge time is incredibly desirable in an EV, and while this may be the case, faster charging can cause an increase in battery degradation and may see vehicle range reduce quicker over time. There are clever ways to achieve a good balance, such as engineering higher power thermal management systems which will allow for a decrease in charge time, but this can cause other vehicle systems to get larger and more expensive.
When it comes to designing a battery pack nearly every variable is dependent on another
While trade-offs are inevitable in most areas, safety is one area for no compromises. In general, most battery cells and modules have to meet UN38.3, but some regulations, such as UN ECE Regulation 100 may not immediately seem necessary, and smaller manufacturers may shy away from them as a result. While initially avoidable in very low volume, safety regulations may be avoided in favour of quicker and cheaper development, particularly by small OEMs who are under various pressures. However, building a battery pack which is as safe as possible is essential. Besides the obvious risks of producing an EV which has not been safety checked as thoroughly as possible, it’s important to consider that these are standard in mass production, so any level of scale will eventually require these tests. By avoiding safety testing many smaller manufacturers are creating larger problems for the future when the vehicle has been redesigned with these regulations in mind.
The next few years will witness large changes in the automotive sector. With unprecedented levels of consumer interest in EVs, the market is set to grow rapidly. It’s no surprise that this growth has attracted all types of OEMs, and more time and effort is being put into the EV market than ever before. To be successful, manufacturers need to develop a product which is competitive at launch and which remains competitive for years to come. Being clever and cost-effective, as well as understanding the needs of the battery pack is more important than ever before.
The opinions expressed here are those of the author and do not necessarily reflect the positions of Automotive World Ltd.
James Eaton is Chief Executive and founder of IONETIC, a UK-based start-up that makes it easier for automotive companies to electrify through the design and manufacture of battery packs
The Automotive World Comment column is open to automotive industry decision makers and influencers. If you would like to contribute a Comment article, please contact editorial@automotiveworld.com