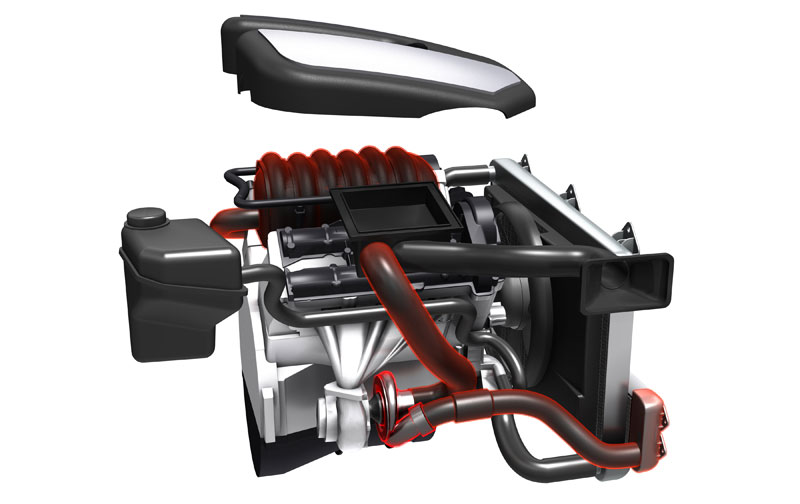
The use of turbochargers by automakers to boost a vehicle’s torque and horsepower in smaller engines is expected to increase rapidly over the next five years. Driving this growth are twin pressures on the global auto industry to reduce fuel consumption and exhaust emissions, which in turn are driving an industry-wide effort to downsize engines.
With more and more turbocharged vehicles on the road, BASF is focused on working with automakers to identify opportunities to lightweight engines while developing materials that can withstand the increased heat and pressure created by a turbocharger’s compressor.
Developing innovative materials, like Ultramid Endure, to meet customer needs and add value is what we do at BASF,” continued Schlicker.
According to Honeywell Turbo Technologies, a leader in turbocharging, this air is very dense and very hot, so it is passed through a charge-air cooler, where it cools and gains even higher density before entering the engine. The presence of this compressed air makes the fuel burn more efficiently, thereby delivering greater power while consuming less energy.
Hot compressed air from the turbocharger outlet is often routed in metal charge air ducts. However, with Ultramid® Endure, BASF offers a less expensive and lighter weight option that provides a great deal more design flexibility for automakers that want to replace these components with plastic.
“Five years ago, turbochargers were primarily just used on diesel engines and now we’re seeing estimates of 6.5 million turbocharged gasoline vehicles on the market in 2020,” said Scott Schlicker, powertrain market segment manager at BASF’s Performance Materials group. “With Ultramid Endure we have a thermoplastic that can withstand temperatures of up to 220°C and peaks of up to 240°C without degradation and it offers the automakers more design flexibility and the opportunity to easily integrate other components, like the surge valve and sensors.”
As a tier-two supplier to the automakers in this instance, BASF works together with automakers and key tier-one turbocharger system component suppliers to participate in the design, development and validation of these components.
“Developing innovative materials, like Ultramid Endure, to meet customer needs and add value is what we do at BASF,” continued Schlicker.
Possible applications include all components of the charge air system, including:
- charge air ducts
- intake manifolds
- intercooler end tanks
- resonators
- sensors and actuators