Just five years after the completion of Renault-Nissan’s greenfield factory in Tangier, Morocco, the millionth Dacia rolled off its production line early in July 2017.
This 300-hectare campus houses 8,000 employees, and comprises a 39,000m² press shop, a 75,000m² body assembly facility, a 38,000m² paint shop and a 90,000m² final assembly building. The plant is now running close to its production capacity of 340,000 units per year, with 1,150 cars produced each day. The first line opened in 2012 and facilitated the production of 50,000 cars. Line two opened a year later, doubling output to 100,000 units. As of July 2017, both lines are running three eight-hour shifts, six days a week, and the plant’s capacity could easily be extended to 400,000 units, plant officials say.
This is where the Sandero, Lodgy, Dokker and Logan MCV models touch down on Moroccan soil, but for most vehicles leaving the production line it is simply a fleeting visit. Almost all vehicles are exported (95%) out of the country via Tangier Port to 73 destinations, primarily Turkey and Europe, but also elsewhere in Africa and – indirectly – to the UK. Most Dacias sold in Morocco are imported from plants in Romania and Algeria.
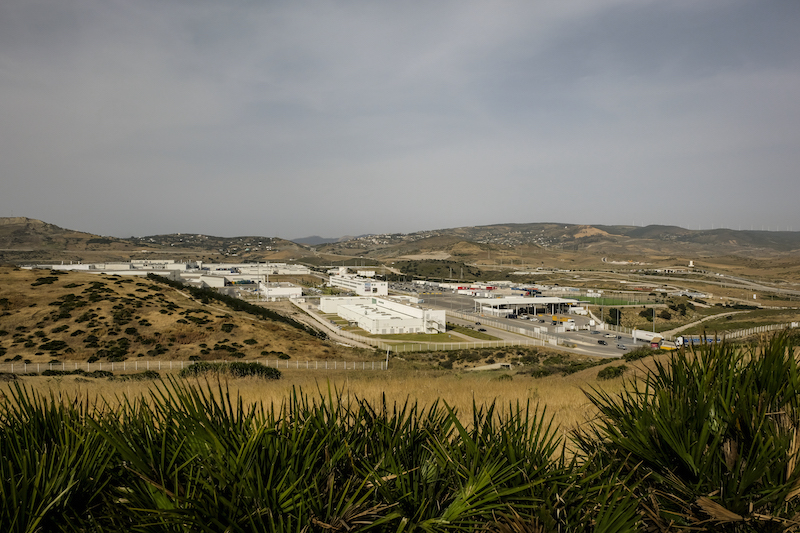
Situated at Morocco’s northernmost point on the Gibraltar Strait, one of the busiest shipping routes in the world, the plant’s location does indeed present an enticing export opportunity. Mehdi Tazi Riffi, a board member of the Tanger Med Special Agency (TMSA), which was established in 2003 to optimise industrialisation around Tangier Port, remarked that the Strait of Gibraltar “is essentially one of the busiest points in terms of global trade.”
Back at the Renault-Nissan plant, a vast storage compound holds up to 8,000 finished cars, and lies below a dedicated rail link to the port. Around 240 cars can be carried per train, with trains travelling back and forth between the plant four to five times each day.
Despite its Romanian heritage and French ownership, Dacia is seen as a Moroccan brand by locals, and is currently the market leader with a 29% share (42% when including Renault). While the Tangier site is littered with Renault-Nissan signs, 98% of the vehicles that leave the factory carry the Dacia badge, with the remaining 2% dedicated to Renault models. All Dacia models are top ten best sellers in Morocco, and are sold via the largest sales network in the country, with 80 points of sale overall and 17 dealerships between Dacia and Renault.
Pressing on
The birth of a Dacia starts at the press shop, a colossal building at the heart of the site that prepares imported steel coils from Armenia, Turkey, and elsewhere in Europe. In an alcove midway through the factory referred to as the ‘Dojo’, young workers are trained to handle these coils – which can weigh as much as 25 tonnes each – just metres from a giant cutting tool that slices sheets into workable lengths.
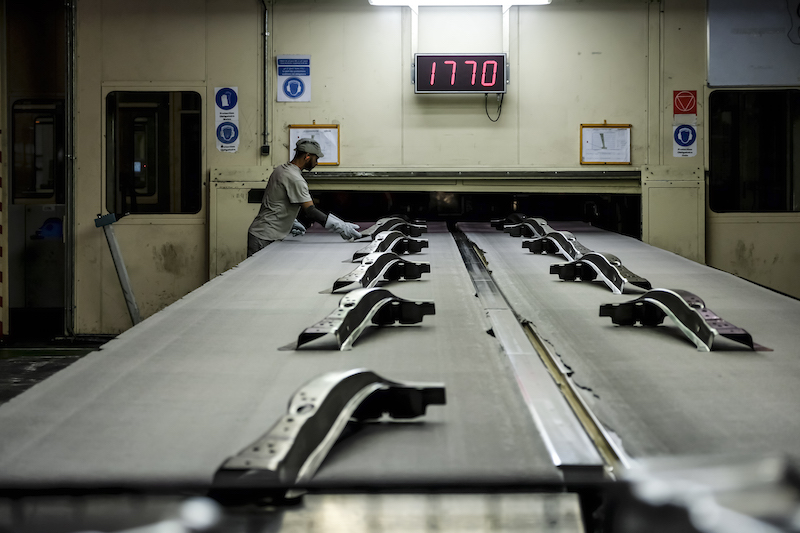
These sheets are then sent to one of five stamping lines, which use 15 tonne dies to stamp each part. Each line has as many as five stamping presses. The process is fully automated, a stark contrast from the body shop which is highly labour intensive and only 7% automated. At the end of the line, the stamped parts – such as B-pillars and body panels – are collected and quality checked by workers.
Next is the body shop, where all these parts are assembled in order to create the vehicle body. Parts that have been stamped are collated in stacks ready to be picked up, and are separated from smaller pre-stamped parts that have been bought in from local suppliers.
As with many vehicle manufacturers, localisation of the supply base is increasingly sought after and nearby suppliers have been encouraged to set up shop in Tangier to cater for the plant’s needs.
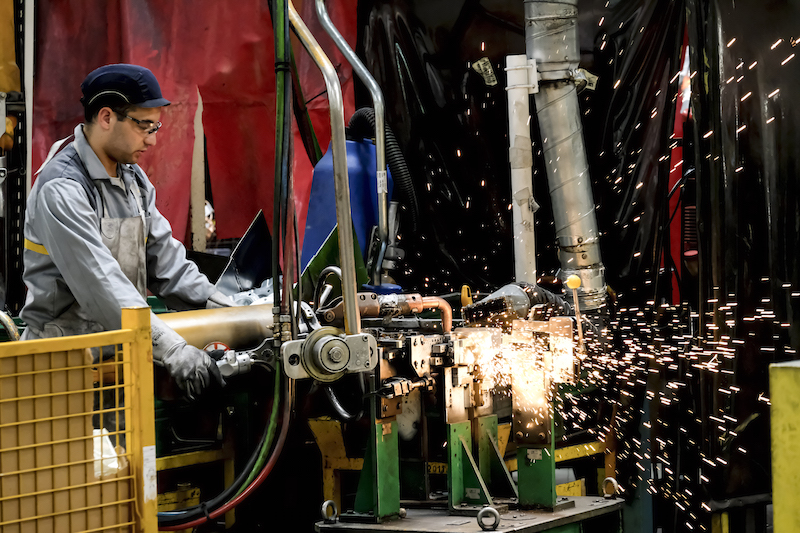
Sourcing local content is “extremely convenient” for the plant’s operations, Jean-Francois Gal, Director of the Renault-Nissan Tangier Plant told Automotive World. “It is our strategy to increase the number of locally sourced parts in our body shop,” he adds, with the number of local suppliers expected to double by 2023. Local content is currently hovering around 40%. Today, large parts such as engines and gearboxes come from Europe, namely Madrid and Seville respectively.
More than 4,000 welding points are made on a vehicle body, 93% of which are performed manually. In some areas, manual welding cannot physically be performed and so a robot will be used – most are supplied by Swiss specialist ABB. Welds are then checked thoroughly, and even the geometries of finished assemblies are measured to ensure they meet specifications. “We have a very severe monitoring plan,” affirms Gal.
90% renewable energy
The vehicle bodies are then transported via a tunnel to the paint shop where they are washed and coated via an electromagnetic painting process. This ensures that every inch of the body is coated by the paint, an important step in protecting against corrosion in future.
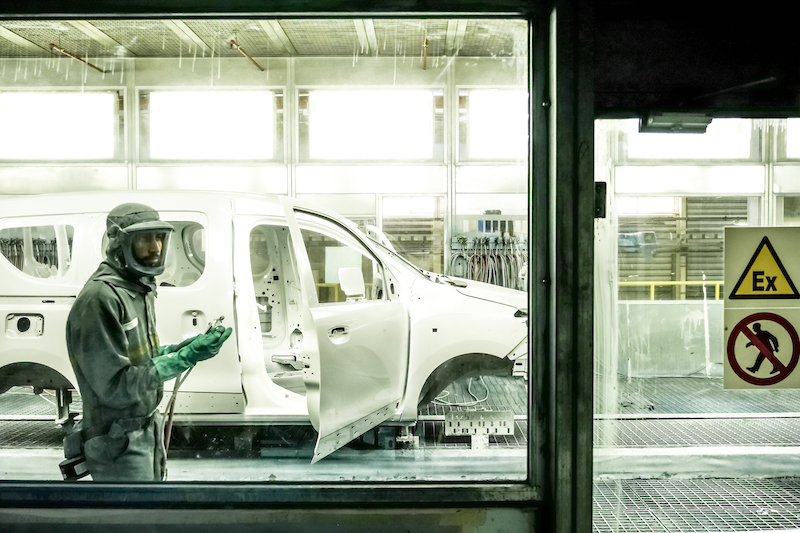
A 50-metre long oven then bakes the painted vehicle bodies at a heat of around 180 degrees Celsius, before extra layers and a varnish are applied. The paint process is one of a car plant’s greatest expenditures of energy and typically a ‘dirty’ procedure in terms of CO2 emissions, but the Tangier factory uses an innovative biomass heating plant.
“In any other plant, gas would be used to heat the paintshop boiler, but as this is an environmentally-friendly plant, it uses biomass to heat the ovens and the painting booth,” said Gal. “As Tangier is a greenfield site, it is easier to create a fully zero CO2 emitting plant. We have a lot of biomass material coming from Morocco’s oil industry, for example.”
Jean-Phillipe Germine, Head of the Renault Groupe’s Environmental Plan, added that using biomass to produce thermal energy for the paint process “remains a unique approach in the automotive industry.”
Other biomass sources such as wood, plastic, cardboard and even olive pulp are used both to keep the plant running and to supply outside recycling companies for profit. There is also a handful of wind farms on site that can provide additional electrical power, and overall, more than 90% of the plant’s needs are fulfilled by renewable energies.
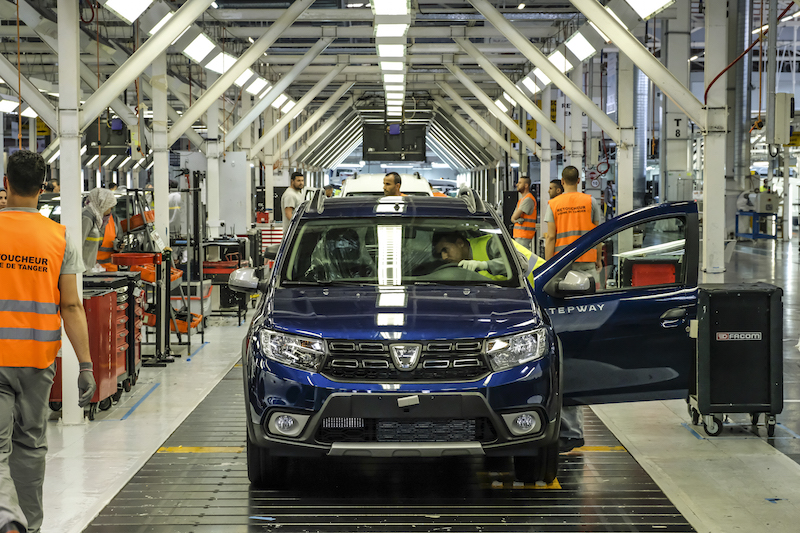
Trim and chassis processes follow the paint shop. Here, various parts are brought for ‘picking and kitting’. The production line snakes around the factory floor as parts are added, and is a primarily manual process, with workers stationed at different stages of the production line to add specific parts. Here, the ‘marriage’ of the chassis and the body takes place, where the engine, fuel tank, exhaust, gearbox and other parts of the chassis are assembled with the body.
Quality control processes at the Tangier factory aim to mimic standards of other plants under the Renault-Nissan Alliance. Every day, six finished cars are randomly selected to undergo a comprehensive inspection, with any defects scrutinised and investigated. Before leaving, all cars undergo a final check – such as for water tightness – and between 2015 and 2016, the number of defects was halved.
On the up
Situated around 20 miles (32km) from Tangier Port, the Renault-Nissan plant is also part of a ‘free zone’ where vehicles can be exported to Europe without import duty. The Moroccan government believes the success shown by this plant will spur further investments from other manufacturers, and is fiercely promoting industrial growth in other industries such as aerospace and electronics.
However, writing for Automotive World in February 2017, Ian Henry, Director of UK-based consultancy AutoAnalysis noted: “Renault’s Tangier plant benefits from being treated as part of the EU from a tax and duty perspective, but given what may well happen to Mexico, i.e. losing its tax-free status with the US, a similar rise of nationalist-protectionist policies in Europe could mean Morocco and Algeria losing their attractiveness for European vehicle companies to invest there.”
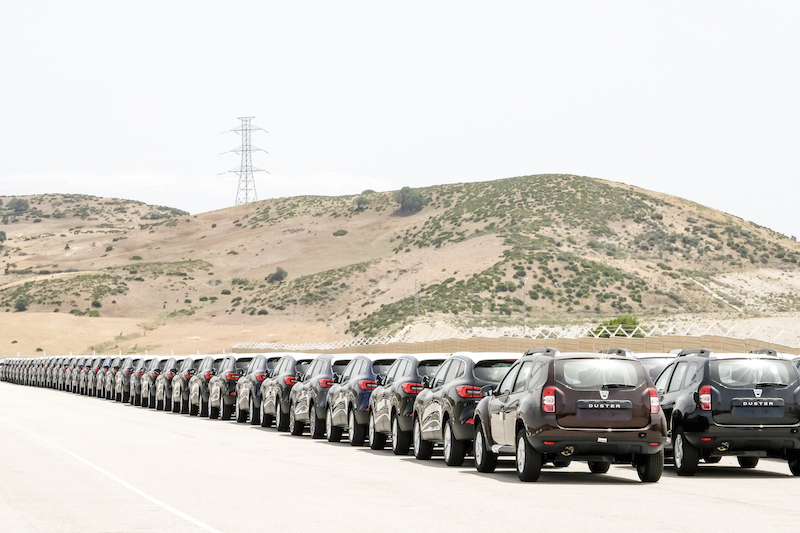
Speaking at a conference at the Renault-Nissan plant, Moulay Hafid Elalamy, Morocco’s Minister of Industry, Investment, Trade, and Digital Economy, noted that the government is “in communication with various car makers” considering investment in Morocco, but he could not reveal which specific brands. “Our purpose is to help Morocco get industrialised, and I am dealing with new and potential investors – many of which are foreign,” he said. “I can’t tell you names – you’ll have to put me in the electric chair to get that answer. We nearly cut a deal with another car maker a few years ago, but something crept up and got in the way.”
In May 2015, Jim Benintende, President of Middle East and Africa (MEA) at Ford, remarked that Morocco has “a growing automotive supplier ecosystem, access to ports, free and fair trade agreements and a very pro-business mindset.” The OEM has a purchasing office in Tangier that supplies parts to its assembly plants elsewhere in Europe, primarily Valencia, Spain.
There is no word on whether Nissan will utilise the plant in future, but PSA is one vehicle manufacturer that is openly developing its foothold in Morocco with the construction of a plant in Kenitra Province, estimated to have a capacity of 200,000 vehicles when fully operational post-2019.
The government has a clear incentive to support local manufacturers regardless of whether vehicles end up registered in Morocco or not. As Elalamy put it: “We as a government try to provide support to OEMs to set up shop and to be more competitive. If they are more competitive, they will pay more tax and create more jobs.”
However, from a commercial standpoint, Marc Nassif, Managing Director of Groupe Renault Morocco, is less enthusiastic for other players to enter the market. “Those who decide to set up shop alongside Renault are most welcome,” he said during the plant press conference. “But when you are a leader in a market, you want to remain as such.”